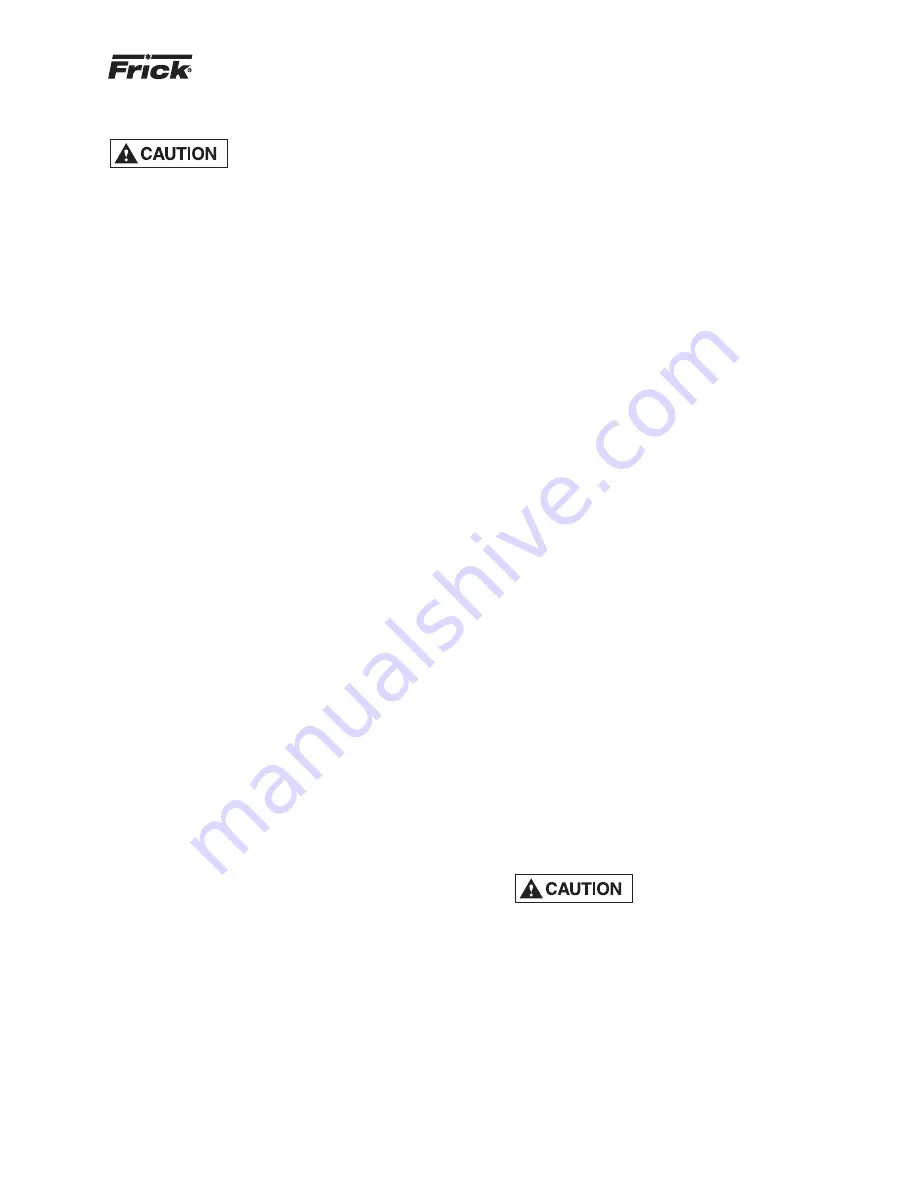
RWB II PLUS MICROPROCESSOR CONTROL
MAINTENANCE
S70-200 OM
Page 23
Testing Micro-Panel Alarms / Cutouts
The following are testing proce-
dures that may be used as a means
of testing the standard safeties pro-
vided on the RWB II Frick Rotary Screw Compressor
Unit with a RWB II Plus microprocessor. They should
only be completed by a competent individual with full
understanding of safe operating procedures as they
apply to industrial refrigeration. If there are any ques-
tions in regard to any one of these procedures, do not
attempt prior to consulting Frick at (717) 762-2121.
High Discharge Press. Alarm / Cutout
1. Once the machine is up and running and maintaining an
even discharge pressure, go to the adjustable setpoints
display (record the values for the Hi Disch Alarm and
Cutout).
2. Step down to the Hi Disch Alarm setpoint and enter a
value of 10 psig lower than the current running Discharge
Pressure.
3. Then go back to the operating display to check for an
alarm. If no alarm exists, ensure that the current discharge
pressure is indeed above the new alarm value.
4. If you do have an alarm, go to Hi Disch Cutout and reset
the value to 5 psig below the current running pressure.
5. You should instantly receive the cutout. If the cutout was
not received, ensure that the value is still lower than the
running pressure.
6. If a cutout was received return to the adjustable setpoints
screen and reenter the original alarm and cutout value.
Clear the alarm and cutout.
7. Allow the recycle delay to elapse and proceed to the next
test.
Low Suction Press. Alarm / Cutout
1. With the machine running and maintaining an even suc-
tion pressure, go to the adjustable setpoints screen
(record the values for the Lo Suct Alarm and Cutout).
2. Step to the Lo Suct Alarm and enter a value 3 psig or 3
in. hg higher than the current running pressure.
3. Return to the operating display and check for an alarm. If
no alarm exists check to ensure that the current running
suction pressure is indeed lower than the new alarm value.
4. If an alarm was received, go to the Lo Suct Cutout and
set the value 5 psig or 5 in. hg higher than the current
running pressure.
5. Once the cutout occurs, go back and reset to the original
values, and clear the cutout and alarm. Allow the recycle
delay to elapse and proceed.
Note: The Lo Suct Cutout has a 90 second delay.
Oil Pressure Alarm / Cutout
1. Push the +/- button and record the Oil Pressure value
from the analog offset display (Example: +2).
2. With the machine running and maintaining good, even
oil pressure, push the [+/-] button to access the analog
offset screen.
3. Step to the oil pressure value and max it out to +9. This
must be done to avoid a sensor fault failure.
4. At the transducer manifold, close the valve for the oil pres-
sure transducer (PE-1) and then open the vent valve which
exposes the transducer to atmosphere.
5. Once the time delays have expired (30 seconds for the
alarm and an additional 10 seconds for the cutout), an
alarm and cutout will occur.
6. Place valves back into their operating position and re-
place the pipe plug in the vent.
7. Return to the analog offset screen and reset the offset
back to the original value.
8. Clear the alarm and cutout. Allow the recycle delay to
elapse, then proceed to the next test.
Hi Oil Temp Alarm / Cutout
1. Record the values for Hi Oil Temp Alarm and Cutout
stated on the fixed setpoints display.
2. Carefully remove temperature probe TE-3, located down-
stream from the oil filter.
3. Slowly apply heat to the probe with a forced-air device
such as a heat gun or blower dryer.
4. Once the temperature rises to the alarm value stated on
the fixed setpoints display, an alarm should be received
with no delay.
5. Allow the temperature to continue rising until the cutout
temperature is met and the cutout is received with no
delay. Allow probe to cool then reinstall in the well.
6. Allow the recycle delay to elapse and proceed with the
next test.
Lo Oil Temp Alarm / Cutout
1. Record the values for Lo Oil Temp Alarm and Cutout
from the fixed setpoints display.
2. Carefully remove TE-4 from the belly of the separator and
immerse the probe into a crushed ice water bath.
3. Once the temperature drops to the alarm value the alarm
will be received without delay. Allow the temperature to
continue falling until the cutout value is met and occurs
without delay. Reinstall TE-4.
4. Clear the alarm and cutout. Allow the recycle delay to
elapse and proceed to the next test.
Hi Disch Temp Alarm / Cutout
1. Record the Hi Disch Temp Alarm and Cutout values
from the fixed setpoints display.
2. With the machine running, remove the discharge tem-
perature probe TE-2 located on the discharge pipe be-
tween the compressor and the separator.
3. Using a forced-air heat source, such as a heat gun or
blow dryer, slowly add heat to the probe and monitor the
operating display until the temperature exceeds the alarm
value and the alarm sounds.
4. Continue adding heat until the cutout value is met and
exceeded. The cutout should be received without delay.
Reinstall TE-2.
5. Clear the alarm and cutout. Allow the recycle delay to
elapse and proceed to the next test.
Never expose the probe to a direct
open flame during test. Rapid tem-
perature rise could cause the probe
to stick or short in the closed position which would re-
quire the probe to be changed.
Comp. Auxiliary
1. Remove #20 wire from terminal strip P3 and place a wire
nut over the end.
2. Push the RUN button.
3. If the input #5 does not receive a signal from the Com-
pressor Auxiliary Contact, the machine will cut out 16 sec-
onds after 2CR is energized.
4. Replace the #20 wire.
5. Clear the Cutout.
6. Allow the recycle delay to elapse and proceed to the next
test.