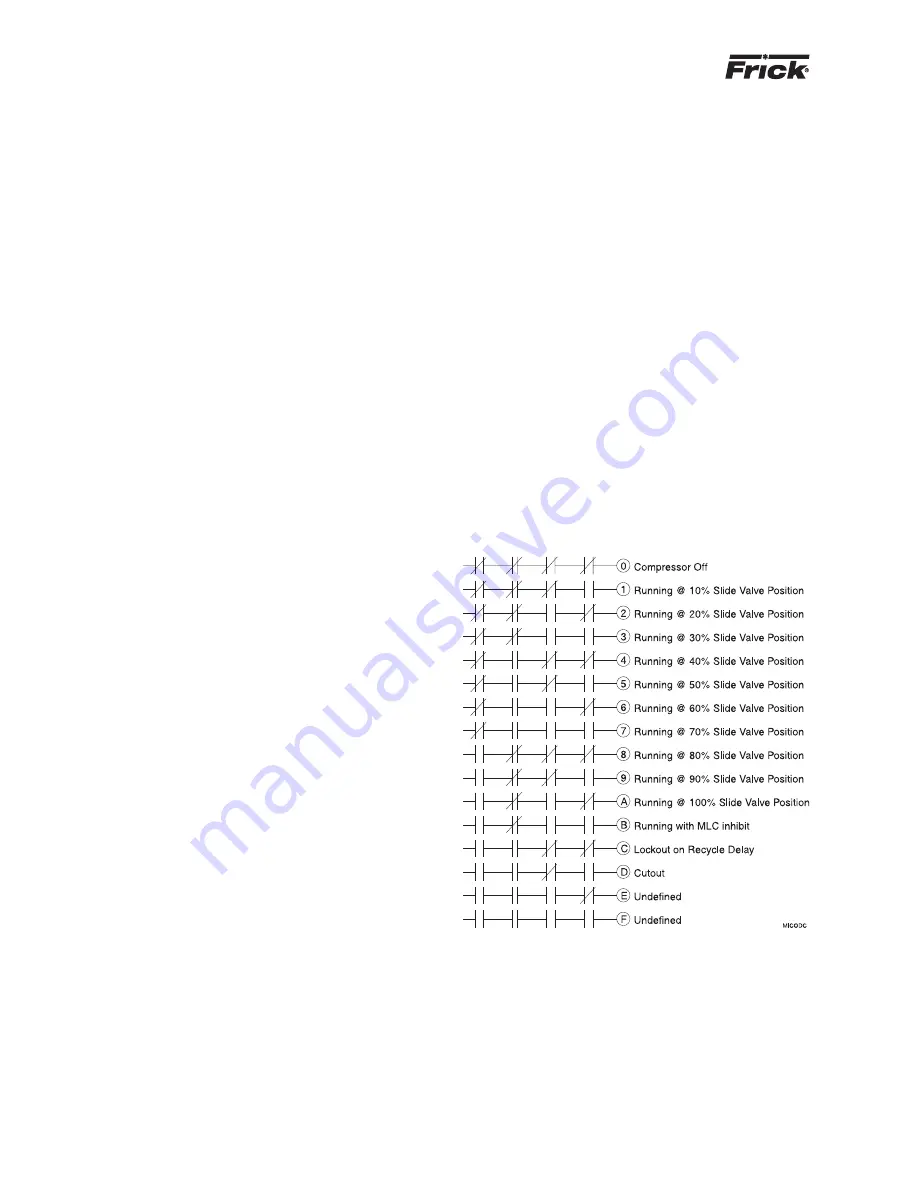
RWB II PLUS MICROPROCESSOR CONTROL
OPERATION
S70-200 OM
Page 14
A typical example of how the microprocessor responds can
be illustrated by the responses generated by the micropro-
cessor as oil temperature increases. Assume that the ambi-
ent temperature and compressor unit temperature are 45
O
F
and you have just pressed the [RUN] key to start the com-
pressor unit:
AT 45
O
F.
The microprocessor receives information that the oil
temperature is below 49
O
F, the Low Oil Temperature Cutout
setpoint, and and shuts down the unit. The microprocessor
will prevent the compressor package from running. The
microprocessor also instructs the oil heater(s) output to ener-
gize the oil heater(s).
AT 50
O
F.
When the oil temperature reached 50
O
F the microprocessor
would allow the Low Oil Temperature Cutout to be cleared
and the compressor unit could now be started. (Assume that
the [RUN] key has been pressed and that the compressor
has now started.) The Low Oil Temperature Alarm would
still be engaged and cannot be cleared until oil temperature
exceeds 58
O
F. The oil heater(s) shut off on compressor start.
AT 113
O
F
The microprocessor instructs the liquid-injection solenoid
output to deenergize the liquid-injection solenoid.
AT 122
O
F
The microprocessor instructs the liquid-injection solenoid
output to energize.
AT 110
O
F TO 150
O
F.
Normal operating range. The microprocessor continues
monitoring oil temperature and reporting this information on
the Operating display.
AT 158
O
F.
The microprocessor triggers the High Oil Temperature Alarm
and displays the alarm on the Operating display and the
Annunciator display.
AT 167
O
F.
The microprocessor instructs the compressor motor to shut
down and displays a CUTOUT indication on the Operating
display. It stores the operating conditions at the moment of
cutout in the Freeze display. Information regarding the cut-
out will also be retained by the Annunciator and the Shut-
down Record displays.
NOTE: If the operator makes an error by attempting to
start the compressor under conditions outside safe
normal operating conditions, the microprocessor will
prevent start-up and advise the operator of the fault.
MULTIPLE COMPRESSOR SEQUENCING
FOR RWB II COMPRESSOR UNITS WITH
MICROPROCESSOR CONTROLS
A - The standard microprocessor panel includes:
1. Remote Run Input
2. Remote Load Input
3. Remote Unload Input
The remote run input is only recognized when the remote
run mode has been selected by pressing the “remote start”
key on the front panel of the microprocessor.
The remote load and unload inputs can only be recognized
when the “remote” key in the slide valve column on the front
panel of the microprocessor has been pressed.
B - If master sequencing between multiple compressors in
parallel on a common suction is desired. This output data
will permit the compressor microprocessor to be interfaced
with a master sequence controller. See electrical diagram
for details.
SUGGESTED PROGRAMMABLE
CONTROLLER PROGRAM TO DECODE
MICROPROCESSOR OUTPUT DATA CODES