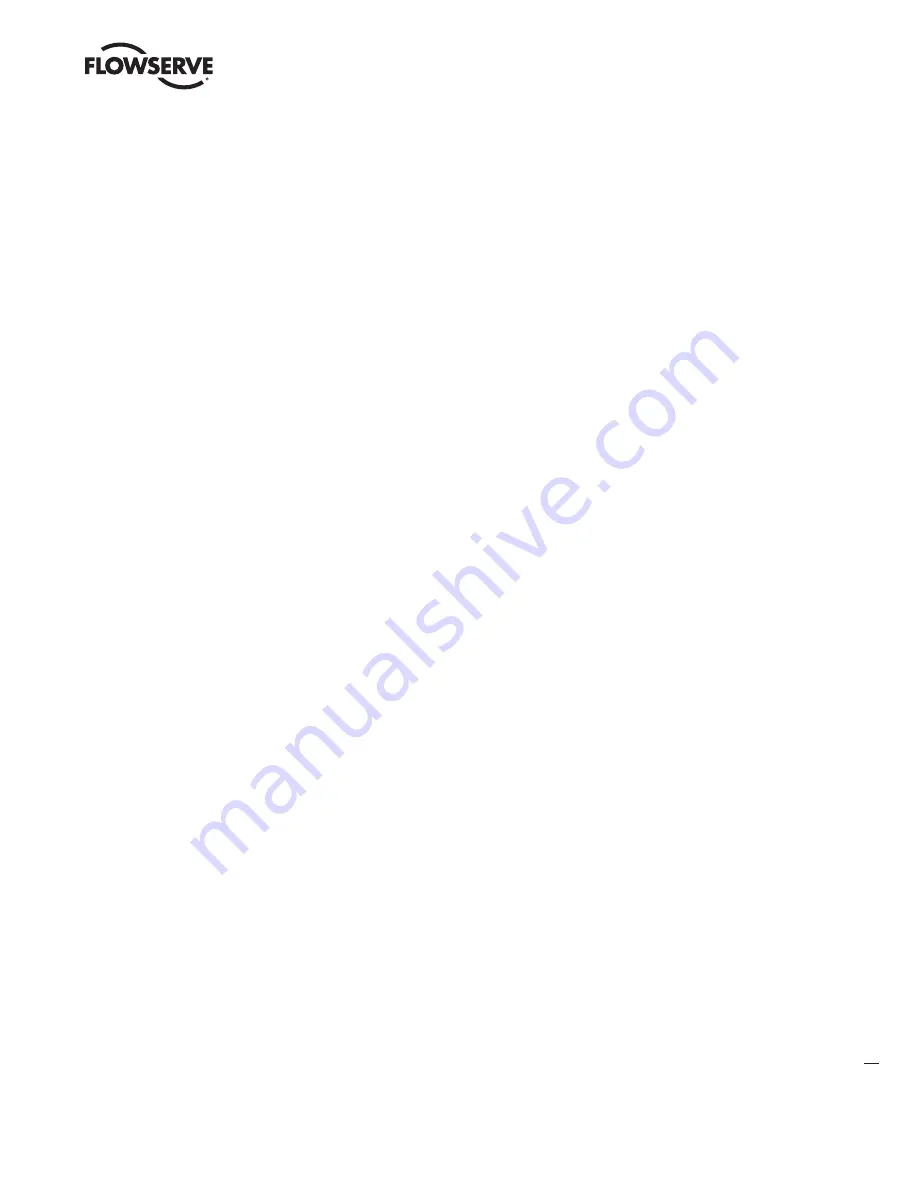
35
Logix
®
420 Digital Positioner FCD LGENIM0106-07-AQ – 10/15
flowserve.com
YYGY
VALVE CLOSED TOO FAR WARNING
VALVE OPENED TOO FAR WARNING
Description: While the valve was in use, it closed or opened farther than
it did at the last calibration by 0.5%.
Possible Solutions: Check the feedback arm linkage and ensure the
valve stem connection is tight. Recalibrate the stroke. If the process
cannot be interrupted a service technician may be able to adjust the
calibration.
YYYR
MEMORY ERROR WARNING
Description: The microprocessor's memory has a problem.
Possible Solutions: Error may clear with time. If error persists, cycle
power and complete a QUICK-CAL. If the error still persists, perform a
factory reset, reprogram or replace the main circuit board.
YYRG
SOFTWARE ERROR WARNING
Description: There has been a watch dog time out, stack overflow
warning, or CPU usage warning.
Possible Solutions: If the problem persists, perform a factory reset. If it
still persists, reprogram or replace the main board.
YRGG
PILOT RELAY RESPONSE WARNING
Description: The pilot relay is sticking or slow to respond. This affects
the responsiveness, increases the chance of limit cycling and excessive
air consumption. The pilot relay is part of the inner loop and consists of
the driver module assembly with piezo (I-P relay) which is coupled to
the spool valve or poppet. The value of this indicator corresponds with
inner loop lag. Delayed response can be caused by a partially clogged
piezo or debris, oil, corrosion, or ice on the spool, or low supply
pressure.
Possible Solutions: Check response of the valve. If OK, adjust Pilot
Relay Response limits. Check supply pressure. Check the spool or
poppet for debris, oil, corrosion, ice on the spool. Clean or replace
the spool or poppet assembly. Replace the piezo or driver module
assembly. Maintain a clean, water-free air/gas supply.
YRRY
PIEZO VOLTAGE HIGH WARNING
PIEZO VOLTAGE LOW WARNING
Description: If the voltage to the piezo is to high, this could indicate an
error with the relay or the main board. This may result from an extended
period of inactivity, but in this case should not persist for more than
30 minutes when the valve is controlling. The positioner may still be
functioning, but have reduced performance under some circumstances.
If the voltage to the piezo is too low, the piezo may be damaged. This
may prevent the proper failure position upon loss of signal/power. This
condition may occur briefly on an air-to-close valve that is held for long
periods of time in the closed position, or an air-to-open valve held in the
open position.
Possible Solutions: Ensure the supply pressure is not low. If alarm
persists for more than 30 minutes, the Piezo assembly is damaged.
Replace the pilot relay.
RGGG
COMMAND INPUT BELOW ADC RANGE
COMMAND INPUT ABOVE ADC RANGE
COMMAND INPUT RANGE TOO SMALL
Description: During Command Loop Calibration, the signal was out
of the Analog to Digital Converter (ADC) range, or difference between
the signal at 0% and the signal at 100% was too small. The system is
designed to accept a difference greater than 5 mA and between 10 and
4085 ADC.
Possible Solutions: Recalibrate making sure to use valid command
signal values.
RGGY
POSITION RANGE TOO SMALL
POSITION SENSOR ABOVE ADC RANGE
POSITION SENSOR BELOW ADC RANGE
Description: During calibration, the range of motion of the position
feedback arm was too small for optimum performance or the feedback
sensor moved beyond its range of operation.
Possible Solutions: Check for loose linkages. Adjust the positioner
mounting. Adjust the feedback pin back into range. Adjust the feedback
pin to a position closer to the follower arm pivot to create a larger angle
of rotation and recalibrate. The minimum angle of rotation should be
greater than 15 degrees. Briefly pressing the QUICK-CAL/ACCEPT
button acknowledges a small range and the positioner will operate
using the short stroke calibration if otherwise a good calibration.