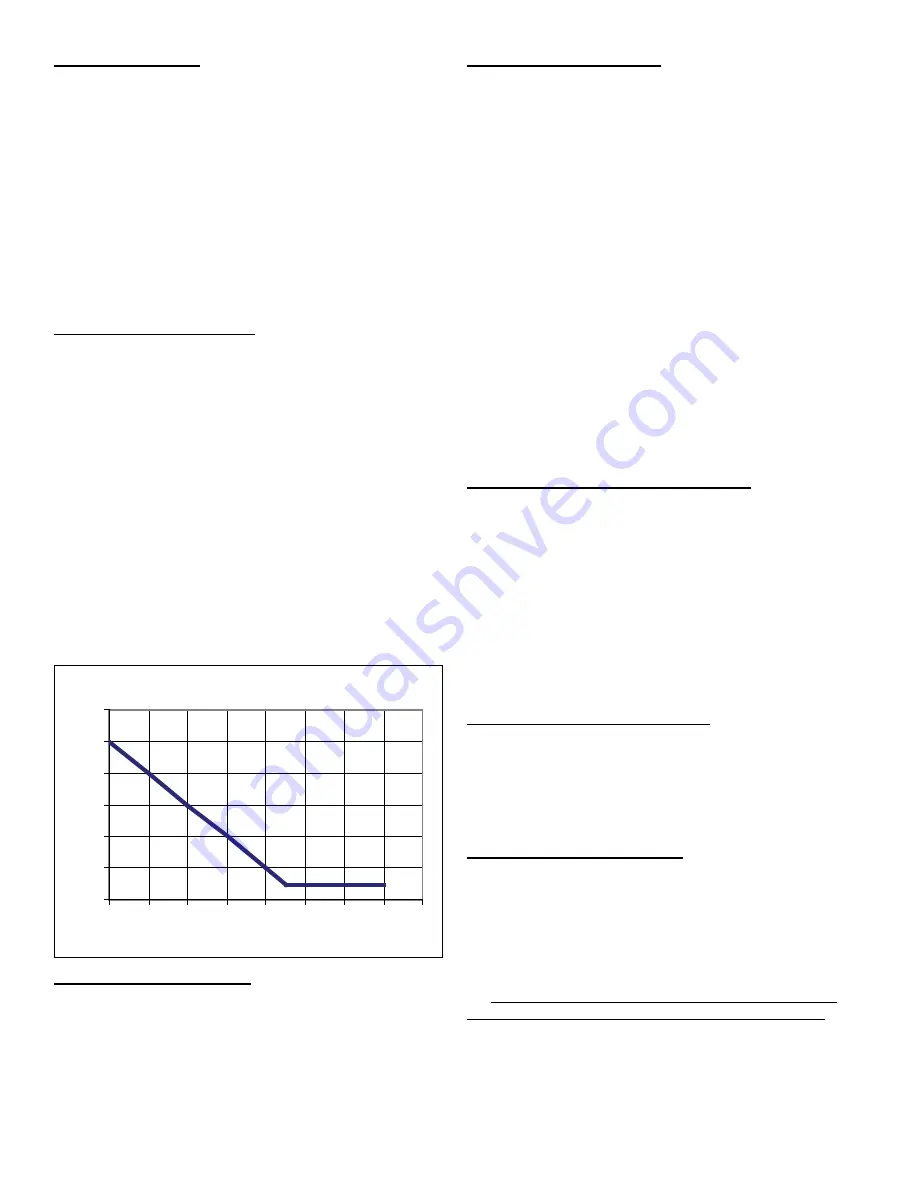
Flint & Walling © Copyright 2018. All rights reserved.
7
Underload Sensitivity
The controller is configured at the factory to ensure detection
of Underload faults in a wide variety of pumping applications
including dead head and run dry conditions . In very rare
cases (as with certain pumps in shallow wells) this trip level
may result in nuisance faults . If the pump is installed in a
shallow well, activate the controller and observe system
behavior . Once the controller begins to regulate pressure,
check operation at several flow rates to make sure the default
sensitivity does not induce nuisance Underload trips . If it
becomes necessary to desensitize the Underload trip level,
please call of Technical Support at 800-742-5044 for further
details .
UNDERLOAD INTELLIGENT RESET
(Display shows Dry Well Trip)
If a motor Underload fault condition occurs, the most likely
cause is an over-pumped well (dry well) or loss of incoming
feed water to the pump . In a dry well situation to allow
the well to recover, the controller will wait 30 seconds to 5
minutes, determined by the amount of time the motor had
been running before sensing the dry well, before restarting
the motor . For example, the first time the fault occurs and
the pump has been running 6 minutes, the controller stop the
motor and will wait 30 seconds before attempting to restart
the pump . If the system would then run for 2 minutes and an
dry well fault recurs, the controller will wait 3 minutes before
attempting to restart the pump . This schedule allows for the
minimum off-time possible based on the recovery time of the
well .
If there is an obstruction (such as a closed valve) between
the pump and the pressure switch/transducer, the controller
will also sense an underload deadhead condition stopping the
motor to avoid damaging the pump .
0
1
2
3
4
5
6
0
1
2
3
4
5
6
7
8
IL1448
Run Time (Minutes)
O
ff
T
im
e
(M
in
ut
es
)
“Intelligent Reset” Recovery Time
Over Temperature Protection
The controller is designed for full power operation in ambient
temperatures to up to 125°F (50°C) as long as the input
voltage is at 230V . Under severe thermal situations, the
controller will reduce power output by reducing the output
frequency in order to avoid shutting down . Full speed output
is restored when the temperature cools .
External alarm trip terminals
The control is fitted with an Alarm In terminal block on the
display board . Using these terminals, an external control
switch can be wired to the drive . With this connection, an
external control such as an over pressure, under pressure,
timer, low level switch, etc . can be used to trip the drive with
an “External Fault” trip . For this connection to work properly,
the Alarm in Relay contact condition setting in the Advanced
Features Menu must be set to match the switch position
to activate the drive . (Example: An irrigation timer closes a
contact to single the drive to run, the Alarm In Relay setting
should be set to NC (Normal Closed) for the drive to be active
during the irrigation cycle .)
This connection can also be used with the “External Control”
feature in the advanced options menu to put the drive in
standby rather than causing an external fault trip .
Caution: The external control must be a dry contact
(i.e. no voltage applied to the Alarm In terminals of the
controller) to not damage the drive circuit boards. An
external control with voltage can only be used with the
controller if an isolation relay is used in conjunction with
the voltage source. Contact technical support for more
information.
Leaky Systems (Pressure Switch Control)
Leaky water systems might keep the controller running due
to the accurate pressure sensing capability of the pressure
switch . Continuous running or starts and stops do not hurt
the controller, pump or motor . However, to reduce the on-time
of the controller/pump/motor, a “Bump-Mode” has been
programmed into the drive . During very low flow (or leaky)
conditions this feature periodically increases the speed of the
pump several PSI above the set point and shuts off the pump .
This adds some time to bleed off before the system starts
up again . This “Bump-Mode” can be turned off or adjusted if
desired . Please call Technical Support at 800-742-5044 for
further details .
Fill Pipe Mode (Transducer Control)
At initial power up, the drive is automatically in the Fill Pipe
Mode for 3 minutes . This allows a new installed system to
fill the pip and build up pressure without having the pump
trip out because it is sensing low pressure . If additional time
is needed, this mode can be turned back on and the time
increased in Parameter menu #7 .
Use of Engine Drive Generators
There are several technical issues that go into correct sizing
of a generator for use with a VFD controller . Since the VFD
is a “non-linear load”, the generator needs to be oversized
considerably for proper operation . Listed below is minimum
recommended sizing of a generator for each drive rating if the
VFD controller is the only load on the generator . Because of
the variation in design of voltage controls used in generators,
the generator manufacture should always be contacted to
verify the correct sizing when used with a VFD controller .
For best results when used with a generator in the Advanced
Features Menu the
Powered by Generator option needs to
be set to “Yes”.