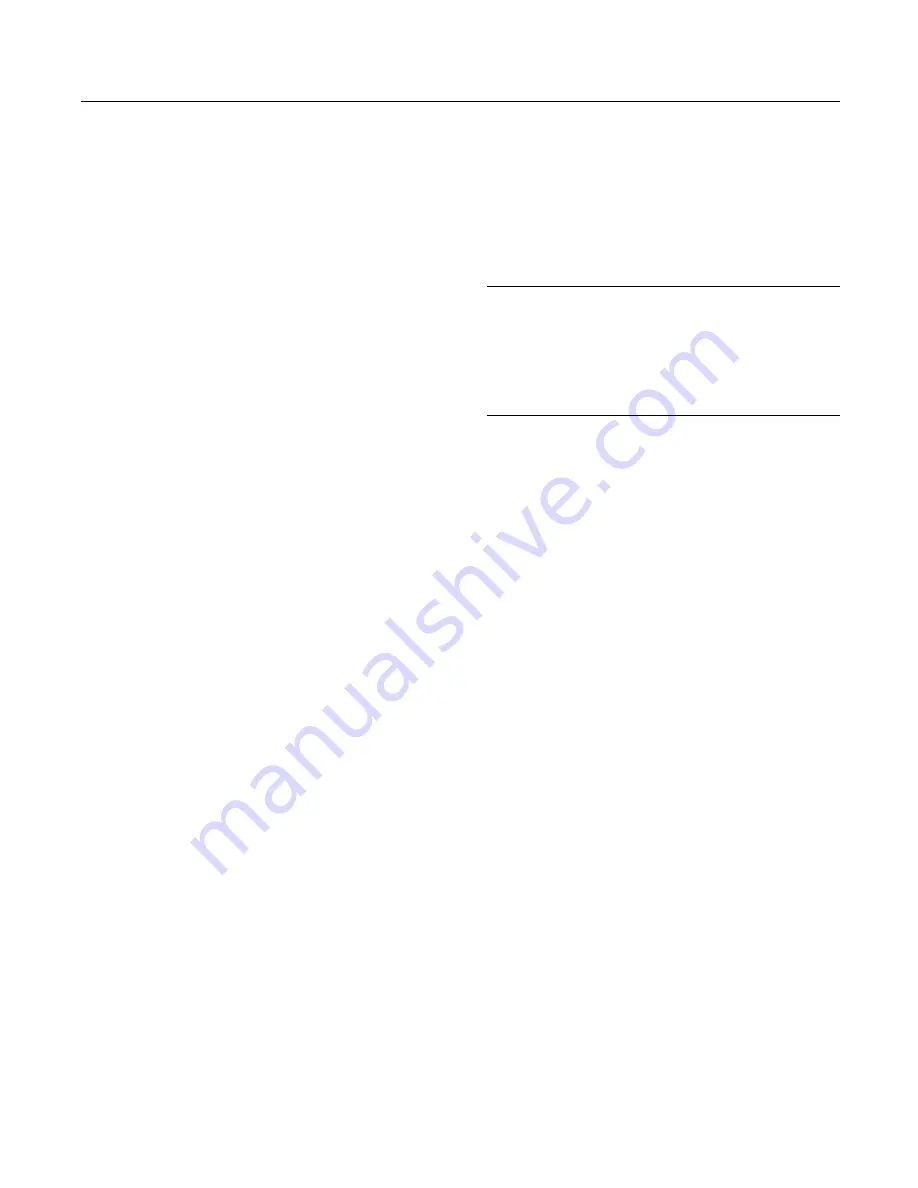
SEBU8325-01
45
Maintenance Section
Refill Capacities
Perkins recommends kinematic viscosities of 1.4 and
4.5 cSt that is delivered to the fuel injection pump.
If a fuel with a low viscosity is used, cooling of the
fuel may be required to maintain 1.4 cSt or greater
viscosity at the fuel injection pump. Fuels with a high
viscosity might require fuel heaters in order to lower
the viscosity to 4.5 cSt at the fuel injection pump.
Density
Density is the mass of the fuel per unit volume
at a specific temperature. This parameter has a
direct influence on engine performance and a direct
influence on emissions. This determines the heat
output from a given injected volume of fuel. This is
quoted in the following kg/m3 at 15 °C (59 °F).
Perkins recommends a value of density of 841 kg/m3
in order to obtain the correct power output. Lighter
fuels are acceptable but these fuels will not produce
the rated power.
Sulfur
The level of sulfur is governed by emissions
legislations. Regional regulation, national regulations,
or international regulations can require a fuel with
a specific sulfur limit. The sulfur content of the fuel
and the fuel quality must comply with all existing local
regulations for emissions.
In some parts of the world and for some applications,
high sulfur fuels above 0.5% by mass might only be
available. Fuel with a high sulfur content can cause
engine wear. High sulfur fuel will have a negative
impact on emissions of particulates. High sulfur
fuel can be used if the local emissions legislation
will allow the use. High sulfur fuel can be used in
countries that do not regulate emissions.
When only high sulfur fuels are available, it will be
necessary that high alkaline lubricating oil is used in
the engine or that the lubricating oil change interval
is reduced. Refer to Operation and Maintenance
Manual, “Fluid Recommendations (Lubricant
Information)” for information on sulfur in fuel.
Lubricity
This is the capability of the fuel to prevent pump
wear. The lubricity of the fluid describes the ability of
the fluid to reduce the friction between surfaces that
are under load. This ability reduces the damage that
is caused by friction. Fuel injection systems rely on
the lubricating properties of the fuel. Until fuel sulfur
limits were mandated, the lubricity of the fuel was
believed to be a function of fuel viscosity.
The lubricity has particular significance to the current
low viscosity fuel, low sulfur fuel, and low aromatic
fossil fuel. These fuels are made in order to meet
stringent exhaust emissions.
The lubricity of these fuels must not exceed wear scar
diameter of 0.46 mm (0.01811 inch). The fuel lubricity
test must be performed on an HFRR, operated at
60 °C (140 °F). Refer to “ISO 12156-1 ”.
NOTICE
The fuels system has been qualified with fuel hav-
ing lubricity up to 0.46 mm (0.01811 inch) wear scar
diameter as tested by “ISO 12156-1 ”. Fuel with higher
wear scar diameter than 0.46 mm (0.01811 inch) will
lead to reduced service life and premature failure of
the fuel system.
In case of the fuels which do not meet specified
lubricity requirement appropriate lubricity additive can
be used to enhance the lubricity of the fuel.
Contact your fuel supplier for those circumstances
when fuel additives are required. Your fuel supplier
can make recommendations for additives to use and
for the proper level of treatment.
Distillation
This is an indication of the mixture of different
hydrocarbons in the fuel. A high ratio of light weight
hydrocarbons can affect the characteristics of
combustion.
Classification of the Fuels
Diesel engines have the ability to burn wide variety
of fuels. Below is a list of typically encountered
fuel specifications that have been assessed as to
their acceptability and are divided into following
categories:
Group 1: Preferred Fuels
The following fuel specifications are considered
acceptable.
Fuels meeting the requirements that are listed in the
table 16.
“EN590 - Grades A to F and class 0 to 4”
“ASTM D975 Grade No. 1-D and 2-D”
“JIS K2204 Grades 1, 2 & 3 & Special Grade 3”
acceptable provided lubricity ware scar diameter
does not exceed of 0.46 mm (0.01811 inch) as per
“ISO 12156-1”.
“BS2869 - Class A2 Off Highway Gas Oil, Red Diesel”
Содержание DB 460
Страница 2: ......
Страница 4: ......
Страница 6: ......
Страница 22: ......
Страница 48: ...48 3 SAFETY PRECAUTIONS id DB 460 REV 00 02 01 2015 VEHICLE EXTERIOR ...
Страница 110: ......
Страница 154: ......
Страница 166: ...166 TECHNICAL ANNEXES DB 460 REV 00 02 01 2015 id HYDRAULIC DIAGRAM ...
Страница 168: ......
Страница 169: ...SEBU8325 01 July 2012 Operation and Maintenance Manual 1104D Mech Industrial Engine NK Engine NL Engine NM Engine ...
Страница 252: ... 2012 Perkins Engines Company Limited All Rights Reserved ...