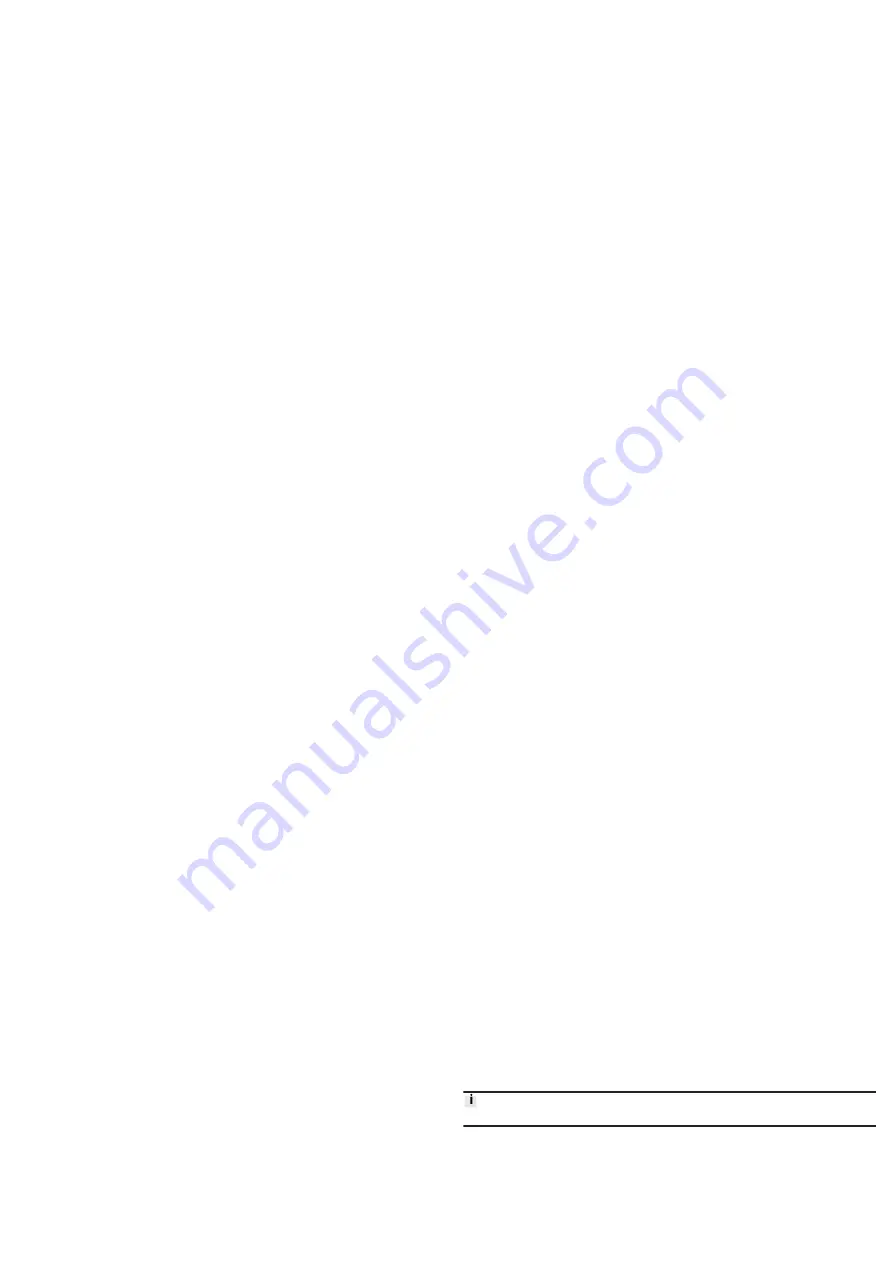
–
This product can generate high frequency malfunctions, which may make it nec-
essary to implement interference suppression measures in residential areas.
–
Wear required personal protective equipment during transport and during
assembly and disassembly of very heavy product versions.
–
Never remove or insert a plug connector while live.
–
Do not loosen any screws on the product other than the following:
–
Earthing screw on the cooling element for mounting the PE connection on the
mains side
–
Retaining screws of the shield clamp on the housing front
–
Only when used in IT networks: screw for connecting the internal mains filter
to PE
–
Install the product in a suitable control cabinet. The minimum degree of protec-
tion required for the control cabinet is IP54.
–
Once installed, only operate the product if all the necessary protective meas-
ures have been implemented (
è
EN 60204-1).
–
Fully insulate all conducting lines on the product. We recommend wire end
sleeves with plastic sleeves for wiring power connections. During wiring, please
observe the necessary strip lengths.
–
Information on strip length
è
Manual Assembly, Installation.
–
Ensure correct protective earthing and shield connection.
–
Prior to commissioning, ensure that the resulting movements of the connected
actuator technology cannot endanger anyone.
–
During commissioning: systematically check all control functions and the com-
munication and signal interface between controller and servo drive.
–
The product is equipped with DC link capacitors, which store dangerous voltage
for up to 5 minutes after the power supply is switched off. Before working
on the product, switch off the power supply via the main switch and secure
it against being switched on again unintentionally. Before touching the power
connections, wait at least 5 minutes.
–
Take into consideration the legal regulations for the installation location.
–
Keep the documentation somewhere safe throughout the entire product life-
cycle.
In the event of damage caused by unauthorised manipulation or any use other
than the intended use, the guarantee will be invalidated and the manufacturer will
not be liable for damages.
In the event of damage caused by using unauthorised software or firmware with
the device, the warranty will be invalidated, and the manufacturer will not be
liable for damages.
Safety instructions for the safety sub-functions
It is only possible to determine whether the product is suitable for specific appli-
cations by also assessing further components of the subsystem.
Analyse and validate the safety function of the entire system.
Check the safety functions at adequate intervals for proper functioning. It is the
responsibility of the operator to choose the type and frequency of the checks
within the specified time period. The manner in which the test is conducted
must make it possible to verify that the safety device is functioning perfectly in
interaction with all components. Time period for cyclical test
data, safety engineering.
Prior to initial commissioning, wire the control inputs of the safety sub-functions
STO and SBC. The safety sub-functions STO and SBC are available on the CMMT-
AS on delivery without the need for any additional parameterisation.
2.2
Intended use
The servo drive CMMT-AS is intended for supply and control of AC servo motors.
The integrated electronics permit regulation of torque (current), rotational speed
and position.
Use exclusively:
–
in perfect technical condition
–
in original condition without unauthorised modifications; only the extensions
described in the documentation supplied with the product are permitted
–
within the limits of the product defined by the technical data
–
in an industrial environment
The safety function might fail and malfunctions might occur if you do not comply
with the parameters required for the ambient and connection conditions.
The CMMT-AS-...-S1 supports the following safety sub-functions in accordance
with EN 61800-5-2:
–
Safe torque off (STO/Safe torque off)
–
Safe brake control (SBC/Safe brake control)
–
Safe stop 1 (SS1/Safe stop 1), achievable with suitable safety relay unit and
appropriate circuitry of the servo drive
The safety sub-function STO is intended to switch off the torque of the connected
motor, thereby preventing an unexpected restart of the motor.
The safety sub-function SBC is intended to safely hold the motor and axis in
position at standstill.
The safety sub-function SS1 is intended for performing a rapid stop with subse-
quent torque switch-off.
2.2.1
Application areas
The device is intended for use in an industrial environment and with appropriate
measures in commercial, residential and mixed areas.
The device is intended for installation in a control cabinet. The minimum degree of
protection required for the control cabinet is IP54.
The device can be operated in TN, TT and IT systems if certain requirements are
met.
Information on allowed and prohibited mains types of system earthing and neces-
sary measures for use in IT networks
è
Manual Assembly, Installation.
Safety sub-functions may only be used for applications for which the stated safety
reference values are sufficient
13.1 Technical data, safety engineering.
2.2.2
Permissible components
The logic power supply must meet the requirements of EN 60204-1 (protective
extra-low voltage, PELV).
If holding brakes and clamping units without certification are used, a risk assess-
ment is required to assess their suitability for the related safety-oriented applica-
tion.
In addition to the requirements of EN 60204-1, the following requirements apply
to other components of the drive system from EN 61800-5-2:
–
Annex D.3.5 and D.3.6 for motors
–
Annex D.3.1 for motor and brake cables
–
Annex D.3.4 for mating plugs
Components approved by Festo for the CMMT-AS fulfil these requirements.
2.3
Foreseeable misuse
Foreseeable misuse, general
–
Use outside the limits of the product defined in the technical data.
–
Cross-wiring of the I/O signals of more than 10 servo drives CMMT-AS.
–
Use in IT networks without insulation monitors for detection of earth faults.
If the device is operated in IT networks, the potential conditions will change in
the event of a fault (earth fault on the feeding mains supply). As a result, the
rated voltage of 300 V to PE – which has important implications for the design
of insulation and network disconnection – will be exceeded. This error must be
detected.
–
Use of a diagnostic output for connection of a safety function.
The diagnostic outputs STA and SBA are not part of the safety circuit. The
diagnostic outputs are used to improve diagnostic coverage of the related
safety sub-function. The diagnostic outputs may only be used in combination
with the related safe control signals (AND operation) plus a reliable time moni-
toring function in the safety relay unit for the purpose of switching additional
safety-critical functions.
Foreseeable misuse of the safety sub-function STO
–
Use of the STO function without external measures for drive axis influenced by
external torques.
If external torques influence the drive axis, use of the safety sub-function STO
on its own is not suitable for stopping the axis safely. Additional measures are
required to prevent dangerous movements of the drive axis, such as use of a
mechanical brake in combination with the safety sub-function SBC.
–
Disconnection of the motor from the power supply.
The safety sub-function STO does not disconnect the drive from the power
supply as defined by electrical safety.
Foreseeable misuse of the safety sub-function SBC
–
Use of an unsuitable holding brake or clamping unit, also in view of:
–
Holding or brake torque and emergency brake characteristics, if required.
–
Frequency of actuation
–
Use of an unsuitable logic voltage supply
2.4
Training of qualified personnel
The product may be installed and placed in operation only by a qualified electro
technician, who is familiar with the topics:
–
installation and operation of electrical control systems
–
applicable regulations for operating safety-engineering systems
Work on safety-related systems may only be carried out by qualified personnel
trained in safety engineering.
2.5
CE marking
The product has the CE marking.
The product-related EC/EU directives and standards are listed in the declaration
of conformity
2.6
Safety engineering approval
The product is a safety device in accordance with the Machinery Directive. For
details of the safety-oriented standards and test values that the product complies
with and fulfils, see
13.1 Technical data, safety engineering.
2.7
UL/CSA certification
Technical data and environmental conditions may be subject to change in order to
comply with Underwriters Laboratories Inc. (UL) certification requirements for the
USA and Canada.
Deviating values
13.4 Technical data UL/CSA certification.
3
Additional information
–
Contact the regional Festo contact if you have technical problems
–
Accessories and spare parts
Firmware, software or configuration files
4
Product overview