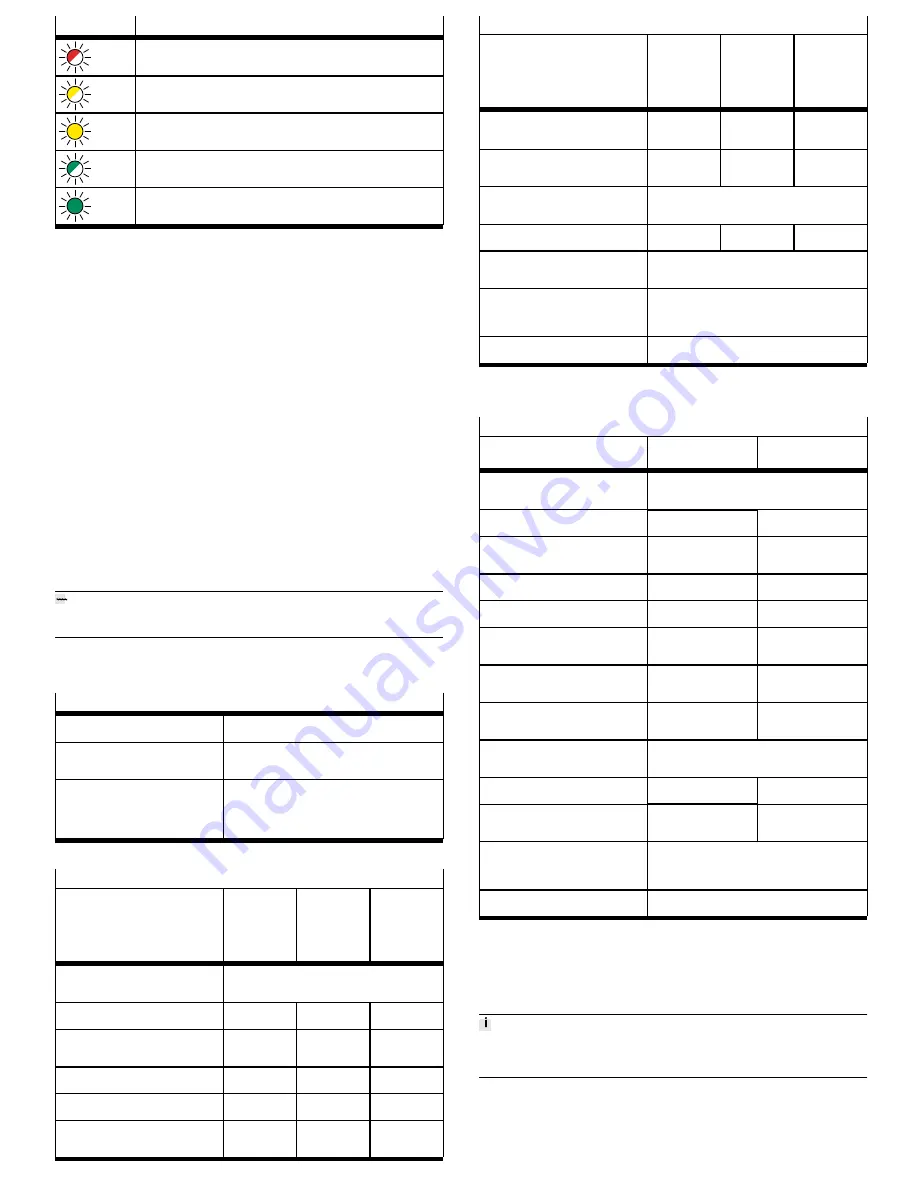
LED
Meaning
Flashes
red
Error in the safety part, or a safety condition has been violated.
Flashes
yellow
The safety subfunction has been requested but is not yet active.
Lights
up yel
low
The safety subfunction has been requested and is active.
Flashes
green
Output stage, brake outputs and safety diagnostic outputs are blocked (safety
parameterisation is running).
Lights
up
green
Ready, no safety subfunction has been requested.
Tab. 46 Safety LED
12.2
Repair
Repair or maintenance of the product is not permissible. If necessary, replace the
complete product.
1. If there is an internal defect: Always replace the product.
2. Send the defective product unchanged, together with a description of the
error and application, back to Festo.
3. Check with your regional Festo contact person to clarify the conditions for the
return shipment.
13
Dismounting
Disassemble in reverse order of installation.
Before dismounting
1. Switch off the power supply at the master switch.
2. Protect the system from being switched back on accidentally.
3. Wait at least 5 minutes until the intermediate circuit has discharged.
4. Let the device cool off to room temperature.
5. Before touching the power connections [X6A], [X9A], [X9B], check to ensure
they are free of voltage.
6. Disconnect all electrical lines.
To dismount the device
•
Loosen retaining screws (2x) and remove the device from the attachment sur
face.
14
Disposal
ENVIRONMENT!
Send the packaging and product for environmentally sound recycling in accord
ance with the current regulations
è
www.festo.com/sp.
15
Technical data
15.1
Technical data, safety equipment
General safety reference data
Request rate in accordance
with EN 61508
High request rate
Reaction time when the
safety subfunction is
requested
[ms]
<
10 (applies for STO and SBC)
Error reaction time (how long
it takes for the diagnostic
output status to become cor
rect once the safety subfunc
tion has been requested)
[ms]
<
20 (applies for STA and SBA)
Tab. 47 Safety reference data and safety specifications
Safety reference data for the safety sub-function STO
Wiring
Without high
test pulses,
without or
with STA
evaluation
With high
test pulses
and with STA
evaluation
1)
With high
test pulses
and without
STA evalu
ation
Safety subfunction in
accordance with
EN 6180052
Safe torque off (STO)
Safety integrity level in
accordance with EN 61508
SIL 3
SIL 3
SIL 2
SIL claim limit for a subsys
tem in accordance with
EN 62061
SIL CL 3
SIL CL 3
SIL CL 2
Category in accordance with
EN ISO 138491
Cat. 4
Cat. 4
Cat. 3
Performance level in accord
ance with EN ISO 138491
PL e
PL e
PL d
Probability of dangerous fail
ure per hour in accordance
with EN 61508, PFH
[1/h]
3.70 x 10
–11
9.40 x 10
–11
5.90 x 10
–10
Safety reference data for the safety sub-function STO
Wiring
Without high
test pulses,
without or
with STA
evaluation
With high
test pulses
and with STA
evaluation
1)
With high
test pulses
and without
STA evalu
ation
Mean time to dangerous fail
ure in accordance with
EN ISO 138491, MTTF
d
[a]
2400
1960
1960
Average diagnostic coverage
in accordance with
EN ISO 138491, DC
AVG
[%]
97
95
75
Operating life (mission time)
in accordance with
EN ISO 138491, T
M
[a]
20
Safe failure fraction SFF in
accordance with EN 61508
[%]
99
99
99
Hardware fault tolerance in
accordance with EN 61508,
HFT
1
Common cause factor for
dangerous undetected fail
ures
β
in accordance with
EN 61508
[%]
5
Classification in accordance
with EN 61508
Type A
1) Safety subfunction STO tested and STA diagnostic output monitored by the safety controller at least 1 x
every 24 h.
Tab. 48 Safety reference data for the safety subfunction STO
Safety reference data for the safety sub-function SBC
Wiring
Two brakes
1)
with
SBA evaluation
2)
One brake
3)
without
SBA evaluation
Safety subfunction in
accordance with
EN 6180052
Safe brake control (SBC)
Safety integrity level in
accordance with EN 61508
SIL 3
SIL 1
SIL claim limit for a subsys
tem in accordance with
EN 62061
SIL CL 3
SIL CL 1
Category in accordance with
EN ISO 138491
Cat. 3
Cat. 1
Performance level in accord
ance with EN ISO 138491
PL e
PL c
Probability of dangerous fail
ure per hour in accordance
with EN 61508, PFH
[1/h]
3.00 x 10
–10
9.00 x 10
–8
Mean time to dangerous fail
ure in accordance with
EN ISO 138491, MTTF
d
[a]
1400
950
Average diagnostic coverage
in accordance with
EN ISO 138491, DC
AVG
[%]
93
–
Operating life (mission time)
in accordance with
EN ISO 138491, T
M
[a]
20
Safe failure fraction SFF in
accordance with EN 61508
[%]
99
87
Hardware fault tolerance in
accordance with EN 61508,
HFT
1
0
Common cause factor for
dangerous undetected fail
ures
β
in accordance with
EN 61508
[%]
5
Classification in accordance
with EN 61508
Type A
1) One brake connected to BR+/BR− and a second brake connected to BREXT; 2channel wiring and request
via #SBCA and #SBCB.
2) Safety subfunction monitored by the safety controller via the SBA diagnostic output at least 1 x every
24 h.
3) Brake connected either to BR+/BR− or to BREXT; 1channel request via the safety controller using #SBCA
and #SBCB; both inputs must be bridged externally.
Tab. 49 Safety reference data for the safety subfunction SBC
The technical data for the safety subfunction SS1 must be calculated individually
according to the application. Use the specified safety reference data for STO and
SBC for the calculation.