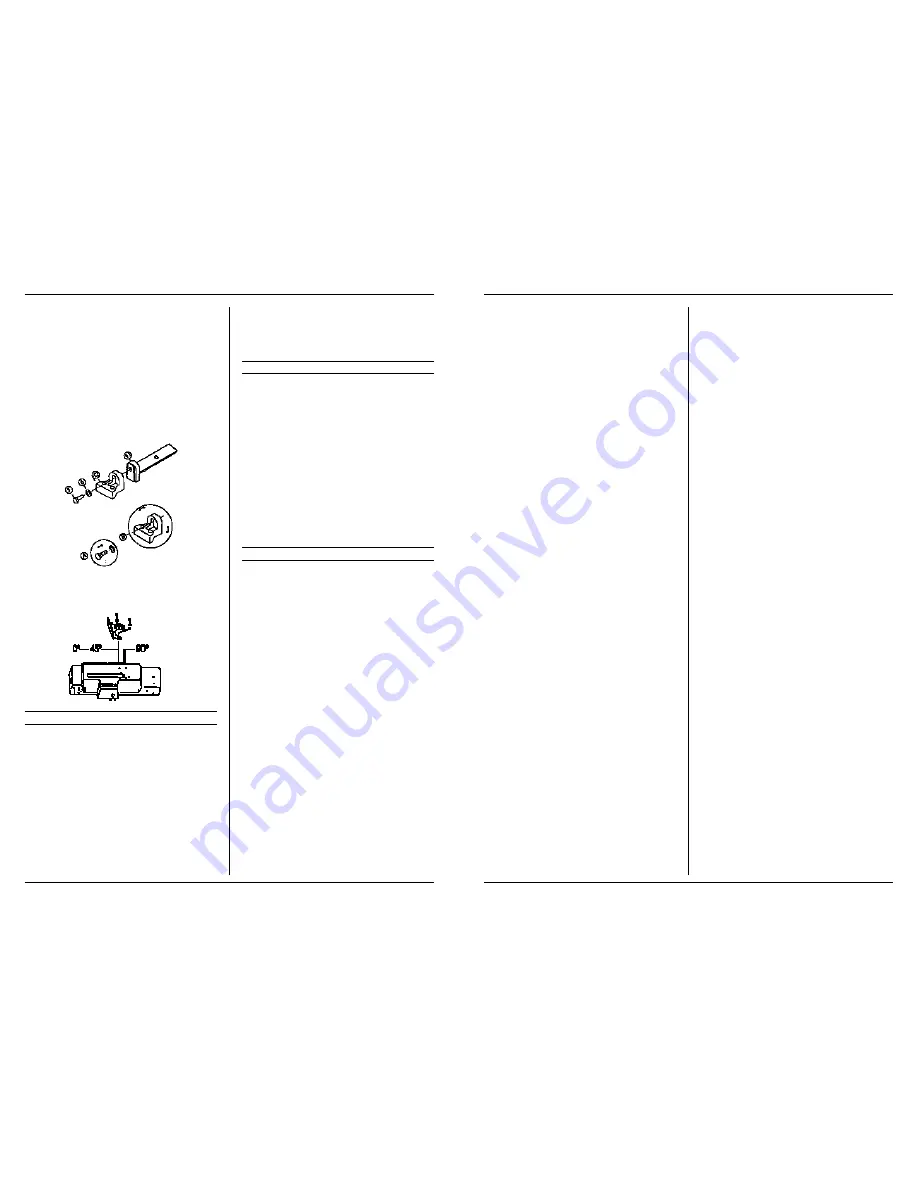
Ferm
25
This adjustment has been completed and power-tested
at the factory. The need for adjustment should rarely oc-
cur when the saw is used properly. If the tracking goes out
of adjustment the blade will leave the wheel and damage
will result. The method of adjustment is shown below:
METHOD OF ADJUSTING BLADE.
1. Loosen the screw (5).
2. Adjust the blade adjustable seat (42) to make the
blade vertical to bed.
3. Place the square on the bed to check if the blade is verti-
cal, if not repeat the process 1 to 3.
4. Tighten the screw (5).
Fig. 3: Adjusting the blade
When cutting 45 degree, please remove vice to front po-
sition.
4. OPERATION
HORIZONTAL CUTTING OPERATION.
Before operating, please read instruction manual and
examine every part including speed, blade selection, gui-
de assemble, position etc. Operation is as follows:
WORK SET UP.
1. Raise the saw head to the vertical position.
2. Open the vice to accept the piece to be cut by rotating
the handwheel at the end of the base (counter-clock-
wise).
3. Place the workpiece on the saw bed. If the workpiece
is long, support the end.
4. Clamp the workpiece securely in the vice by rotating
the handwheel clockwise.
CUTTING.
Close switch, letting the head down slowly onto the
work. Do not drop or force, let the weight of the saw-
head pro-vide the cutting force. The saw automatically
shuts off at the end of the cut.
5. MAINTENANCE
LUBRICATION.
Lubricate the following components using Apone 90 as
noted.
1. Ball bearing
: none
2. Blade guide bearing
: none
3. Drive wheel bearing
: none
4. Vice lead screw
: as needed
5. The drive gears run in the oil bath and will both requi-
re a lubricant change more often then once a year.
When needing a change, first put down the head to a
horizontal position, then loosen the 4 screws of the
gearbox and open the cover. Place a pan under the
tight lower corner of the gearbox. Slowly raise the
head until the oil flows out. Lower head. Wipe up ex-
cess oil and foreign matter with soft rags. Then add lu-
bricant into the gearbox until it is full and not flow
over. Close the cover, tighten the 4 screws.
6. TROUBLESHOOTING
1. Excessive blade breakage.
Material loose in vice.
- Clamp workpiece securely.
Incorrect speed or feed.
- Adjust speed or feed.
Blade teeth spacing too large.
- Replace with a small teeth spacing blade.
Material too coarse.
- Use a blade of slow speed and small teeth spacing.
Incorrect blade tension.
- Adjust to where blade just does not slip on wheel.
Teeth in contact with material before saw is started.
- Place blade in contact with work after motor is started.
Blade rubs on wheel flange.
- Adjust wheel alignment.
Misaligned guide bearings.
- Adjust guide bearings.
Blade too thick.
- Use thinner blade.
Cracking at weld.
- Weld again, note the weld skill.
2. Premature blade dulling.
Teeth too coarse.
- Use finer teeth.
Too much speed.
- Decrease speed.
Inadequate feed pressure.
- Decrease spring tension on side of saw.
Hard spots or scale on material.
- Increase feed pressure by reducing spring tension.
Work hardening of material.
4
Ferm