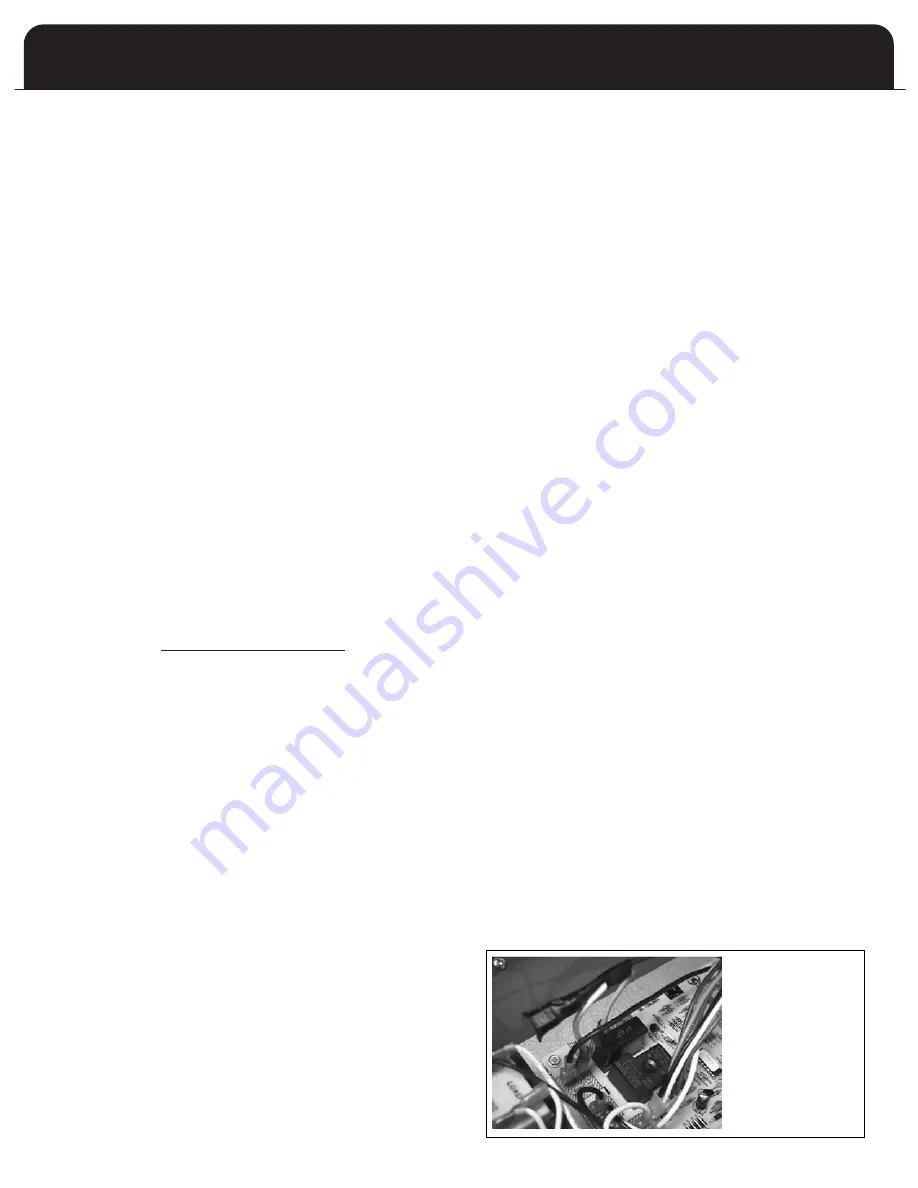
18
WARM AIR FURNACE
Figure 10:
Piggyback
Connector
Remove blue wire
from HEAT terminal,
tape it off, and
replace it with a
jumper. Connect the
black wire and
jumper to COOL.
CHECKING FURNACE INPUT
• The natural gas supply pressure should be a maximum of
7 inches w.c. and minimum of 5 inches w.c.
• The burner manifold pressure is normally set to 3.5 inches
w.c. for natural gas
• The input rating of the furnace is based on 1075 / BTU/cu.
ft. gas with a specific gravity of 0.60
Since heating values for the gas vary geographically, the
actual furnace input and output will vary accordingly.
For example, natural gas with a 1000 BTU / cu. ft. heating
value will reduce the input to 93% of the rated input.
Natural gas with a 1100 BTU / cu. ft. heating value will
increase the input to approximately 103% of the rated
input. This is not usually a problem; however, adjustments
to compensate for this can be made by minor adjustments
to the burner manifold pressure or by changing the burner
orifice size.
In the previous example where the heating value of the gas
is 1100 BTU / cu. ft., the burner manifold pressure can be
reduced .3% to 3.4% w.c. which is within the ±0.30 inches
w.c. specification to bring the input into compliance. Refer
also to Setting the Gas Pressure, and contact the fuel
supplier for specific gas heating content values.
If using a gas meter to check the furnace input, be sure that
all gas fired appliances other than the furnace are off
during the test.
Any adjustments to the burner manifold pressure should be
carried out with the use of a manometer or calibrated
magnehelic gauge. Do not adjust the gas valve pressure
regulator more than ± 0.30 inches water column.
The formula for determining the furnace input via the gas
meter test dial is:
Where:
Input is expressed in BTU / Hr.
Heating value of the gas is expressed in BTU / cubic feet
Time means time required for the test dial to indicate 1
cubic foot in seconds.
If using a gas meter with SI (metric) units:
1 cubic foot = 0.0283 cubic meters.
1 cubic meter = 35.315 cubic foot.
0.01cubic meter = 0.3531 cubic foot.
0.5 cubic meter = 1.766 cubic feet.
Input
Heating Value of Gas
3600
Time in Sec. for 1 cu. ft
=
X
VALUES
H
VALUE OF NATURAL GAS in BTU / FT_
1000
1050
1100
46,512
48,837
51,163
65,116
68,372
71,628
125,581
131,860
138,140
TEMPERATURE RISE CHECK
When the duct system is complete and the air filter or filters
are in place, determine if the airflow is correct.
1. Insert a duct thermometer in the supply air duct. The
thermometer should be placed as close as practical to
the furnace, but out of the "line of sight" of the heat
exchanger (this prevents false readings owing to
radiant heat). Ensure that the thermometer location is
within the duct air stream. Avoid locations such as the
inside radius of an elbow, etc.
2. Insert a duct thermometer in the return air duct as
close to the furnace as practical. Ensure that the
thermometer location will be unaffected by humidifier
bypass ducts, etc. Choose a location well within the
main air stream.
3. Operate the furnace long enough to obtain steady
state conditions.
4. When the two thermometers have stabilized, usually
within 5 - 8 minutes, compare the two readings.
Subtract the return air temperature from the supply air
temperature. The difference is the temperature rise,
also called
∆
T.
5. Compare the measured
∆
T to the temperature rise
range shown on the rating plate.
Unless stated differently on the rating plate, the
temperature rise should normally range between 30° to
60°F or 35° to 65°F. When adjusting the temperature rise,
the ideal temperature is approximately mid-range.
If the measured
∆
T is above the approved temperature
range, there is too little airflow. The airflow must be
increased by selecting a faster fan speed, removing
restrictions in the ductwork, or adding supply or return
ductwork.
If the measured
∆
T is too low, there is too much airflow.
Use a lower speed tap on the multispeed motor. The blow-
er speed is changed at the integrated furnace control.
Remove the wire from the “HEAT-H” terminal of the
50A55-20 integrated furnace control and plug in the
desired wire on the “HEAT-H” terminal. When this config-
uration is used, the following color codes are used: Black -
High Speed, Blue - Medium-High Speed, Yellow - Medium-
Low Speed and Red - Low Speed. The unused leads are
connected to the M1, M2 terminals on the 50A55-20 inte-
grated furnace control.
IMPORTANT:
If the heating speed and cooling speed are to
be the same, remove the cooling lead from the control,
tape it off, then install a "piggyback" connector from the
control "HEAT" terminal to the "COOL" terminal. UNDER
NO CIRCUMSTANCE MAY TWO MOTOR WINDINGS BE
POWERED SIMULTANEOUSLY.
The piggyback connector is used for both types of motor
wiring configuration wiring block and permanent lead, see
figure 10 below.
IMPORTANT: NEVER ADJUST THE INPUT OF THE FURNACE
TO EXCEED THE INPUT SHOWN ON THE RATING PLATE.
Содержание F80A
Страница 24: ...23 MODEL F80A 50V51 250...
Страница 26: ...25 MODEL F80A R R 3 FACTORY SETTING...