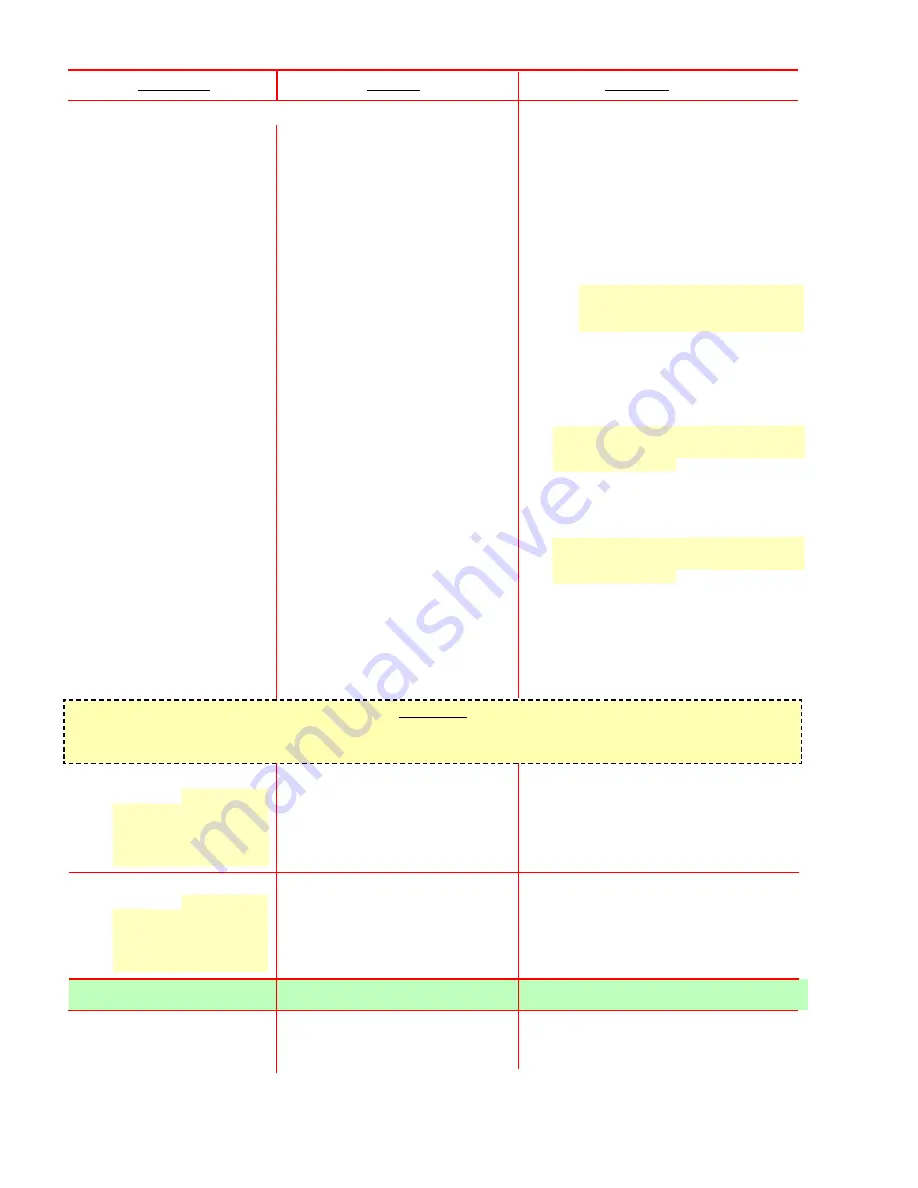
(Item 13.22 continued from previous page.)
D. Base refrigeration settings.
D. Load all Defaults to ensure factory
settings.
E. Hot gas valve is stuck open,
E. Recover refrigerant and remove
or debris is preventing valve
blockage or replace valve, if
from closing.
necessary. Recharge system with
48.5 oz. of R404-A.
F.
Expansion valve not opening.
F.
1.
Test expansion valve coil to
ensure it is receiving 24VAC.
Replace expansion valve if
plunger inside doesn't move.
Contact FBD Warranty
Dept. before tapping system,
if unit is under warranty!
Recover refrigerant and replace
valve. Recharge system with
48.5 oz. of R404-A.
2.
Test relay board for 24VAC
output and 5VDC relay coil
input. Replace, if necessary.
G. Expansion valve restriction.
G.
Contact FBD Warranty Dept.
before tapping system, if unit is
under warranty!
Recover
refrigerant and remove blockage or
replace valve if necessary.
Recharge system with 48.5 oz. of
R404-A.
H. Refrigeration leak or low
H.
Contact FBD Warranty Dept.
refrigerant charge.
before tapping system, if unit is
under warranty!
Put gages on
system and check pressures.
Single side suction
should be
32-35psi
, dual side 42-45psi.
Single and dual side
discharge
should be
275-300 psi
. Check for
and repair leaks, recharge system
with 48.5 oz. of R404-A.
CAUTION
DO
NOT
PRESSURIZE LOW SIDE (EVAPORATOR AND COMPRESSOR SUCTION) ABOVE 150 PSI
FOR ANY REASON! COMPONENTS WILL FAIL AND WARRANTIES WILL BE VOID.
13.23
High head/suction
A. Condensor air flow restricted.
A. Check for air flow restriction, clean
pressure.
Contact
condensor and air filter.
FBD Warranty Dept.
B. Compressor damage
B. Check amp draw on compressor
before tapping
(normal running 13 amps).
system, if unit is
C. High ambient temperature.
C. Temperature surrounding unit
under warranty!
should be less than 90°F.
13.24
Low head/suction
A. Low refrigerant level.
A. See item 13.22.H above.
pressure.
Contact
FBD Warranty Dept.
B. Compressor damage.
B. Check amp draw on compressor
before tapping
(normal running 13 amps).
system, if unit is
under warranty!
DRINK QUALITY
13.25
Drink too “Wet” or
A. Chamber not filled properly.
A. Defrost, then assure chamber is
“Liquid”.
90% full.
B. CO
2
check valve clogged.
B. Clean or replace check valve.
(Item 13.25 continued on next page.)
TROUBLE
CAUSE
REMEDY
25