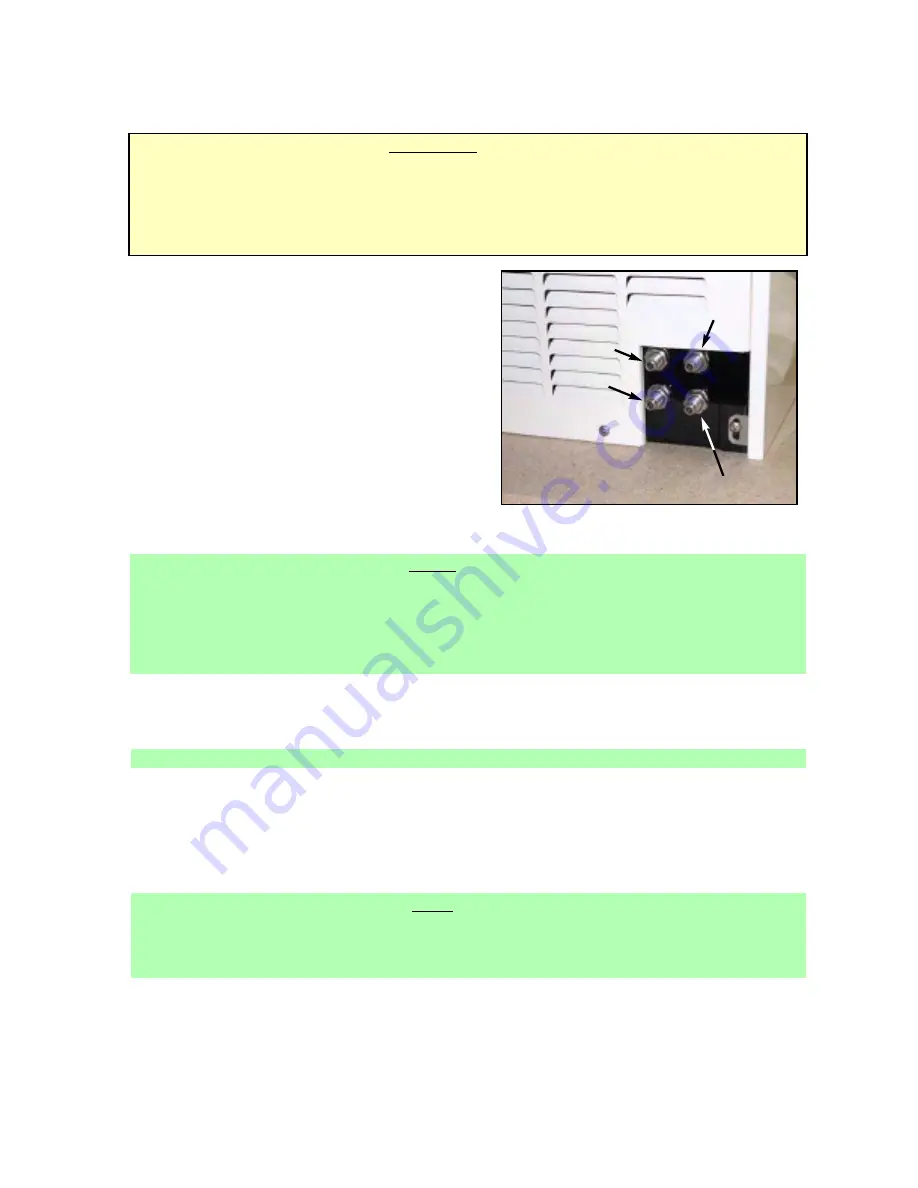
5.
CONNECTING WATER, CO
2
, AND SYRUP SUPPLIES
5.1
WATER SUPPLY
IMPORTANT
A WATER PUMP AND WATER REGULATOR ARE INSTALLED IN THE BASE OF THE MACHINE.
A WATER FILTER SHOULD BE INSTALLED IN THE WATER LINE BEFORE BEING
CONNECTED TO THE MACHINE. FLUSH THE FILTER WITH SEVERAL GALLONS
(12-15 LITERS) OF WATER PRIOR TO USE TO INSURE BLACK CARBON "FINES" ARE NOT
FED INTO THE FREEZING CHAMBER.
3
Figure 5
CO
2
Water
Syrup 2
Right
Syrup 1
Left
5.2
CO
2
SUPPLY
NOTE:
The CO
2
supply may come from either an independent tank/regulator or a bulk CO
2
system. If
connected to a bulk CO
2
system, install a shutoff valve and a secondary supply regulator [to be set
at 70-72 PSIG (482.6-496.4 KPa)] in the line.
Ensure that the CO
2
line comes directly from the
main branch on the bulk supply and is not branched off down line. Failure to do so may
starve the unit of CO
2
flow and cause performance problems.
A. Fabricate a 3/8 inch supply line for connecting the unit to a CO
2
supply.
B. Connect the supply line to the CO
2
bulkhead fitting labeled "CO
2
IN" located at the rear of the
unit (see Figure 5.2). A 3/8” barb by 1/4” flare nut fitting will be required to make connection.
C. Splice a barb "cross" into the CO
2
supply line and run two (2) lines to the syrup pump CO
2
inlets.
Or
If Figal tank will be utilized, splice a barb "cross" into the CO
2
supply line and run two (2) lines
to tank location and install CO
2
tank couplers to end of lines.
D.
Do not turn on the CO
2
at this time.
5.3
SYRUP SUPPLY
The unit may be connected to either a BIB (Bag-in-Box) or a five-gallon syrup supply (figal). Use
the appropriate connection method below.
NOTE
Installations requiring long runs of tubing [25 feet or more (7.62 meters or more)] may encounter
pressure fluctuation problems. The machine's sensors may indicate that the machine is out of
syrup, water, or CO
2
. To avoid pressure fluctuations, consider the following solutions.
A. Increase the tubing size to 3/8 inch diameter.
B. Install booster pumps in the supply lines. Use a vacuum regulating valve with syrup booster
pumps.
C. Increase primary CO
2
regulator pressure from bulk or tank CO
2
to 105 - 120 PSIG (723.9 to
827.4 KPa). A secondary regulator
will
be necessary for syrup pumps to avoid exceeding
manufacturer’s recommended operating pressures. Set the secondary regulator to 70-72 PSIG
(482.6-496.4 KPa).
A. Fabricate a 3/8 inch supply line for connecting
the unit to a potable water supply (a 3/8” barb by
1/4” flare nut fitting will be required).
B. Install a shutoff valve in the water line as close to
the unit as practical and convenient.
C. Clear the line by running a minimum of two (2)
gallons (7.57 liters) of water through the line
before attaching the line to the unit.
D. Connect the line to the bulkhead fitting labeled
"WATER IN" located at the rear of the unit (see
Figure 5).
E.
Do not turn water on at this time.