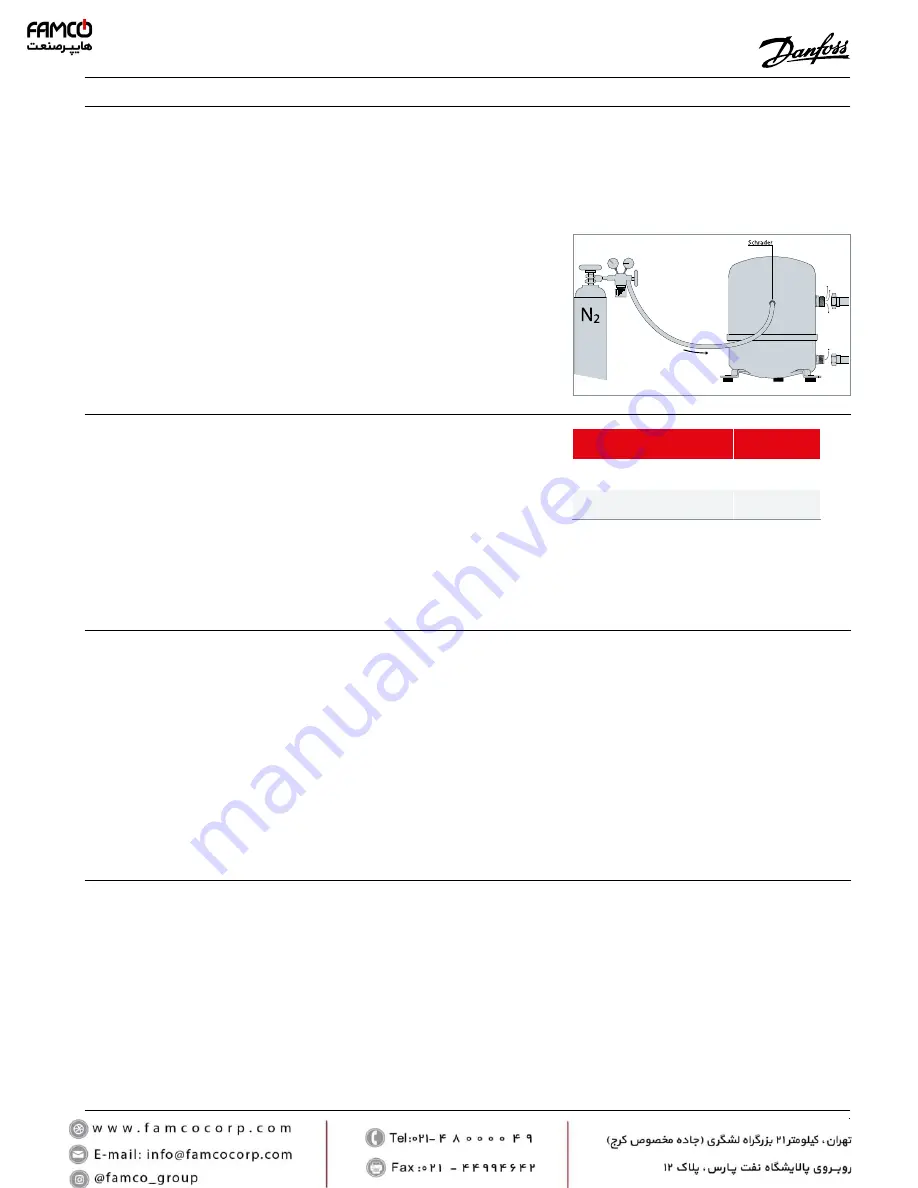
Application guidelines
31
FRCC.PC.004.A9.22
Installation and service
System pressure test
Leak detection
It is recommended that an inert gas such as
nitrogen be used for pressure testing. Dry air
may also be used but care should be taken
since it can form an inflammable mixture with
the compressor oil. When performing a system
pressure test, the maximum allowed pressure
for the different components should not be
exceeded.
For MT/MTZ compressors the maximum test
pressures are shown in the table beside.
1-2-4 cylinder
compressors
Maximum compressor test
pressure, low side
362 psi(g)
Maximum compressor test
pressure, high side
435 psi(g)
Do not exceed 435 psig pressure difference
between high pressure side and low pressure
side of the compressor because this will open the
internal compressor relief valve.
Whenever possible (if valves are present) the
compressor must be kept isolated from the
system. Perform a leak detection using the final
refrigerant. Pressurize with nitrogen or another
neutral gas and use a leak detector for the
applied refrigerant. Any spectrometric detection
system using helium can also be applied.
Eventual leaks shall be repaired respecting
the instructions written above. It is not
recommended to use other gasses such as
oxygen, dry air or acetylene as these gasses can
form an inflammable mixture. Never use CFC
or HCFC refrigerants for leak detection of HFC
systems.
Note 1: Leak detection with refrigerant may
not be allowed in some countries. Check local
regulations.
Note 2: Leak detecting additives shall not be used
as they may affect the lubricant properties.
Warranty may be voided if leak detecting
additives have been used.
In this situation nitrogen or CO
2
must be purged
through the compressor via the schrader valve to
prevent air and moisture ingress. Purging must
start when the caps are removed and proceeded
during the brazing process.
When rotolock valves are used on the
compressor, they shall be closed immediately
after mounting, thus keeping the compressor
isolated from atmosphere or from a not yet
dehydrated system.
Note: When the compressor is built into a ”pack”
or “rack” configuration which is not installed
immediately on its final location, a vacuum pull-
down and moisture removal must be performed
to this pack (rack) as if it were a complete system
(see below). The pack must be charged with
nitrogen or CO
2
and open tubes must be blocked
with caps or plugs.
Vacuum pull-down moisture
removal
Moisture obstructs the proper functioning of the
compressor and the refrigeration system.
Air and moisture reduce service life and increase
condensing pressure, and cause excessively high
discharge temperatures, which can destroy the
lubricating properties of the oil. Air and moisture
also increase the risk of acid formation, giving
rise to copper platting. All these phenomena
can cause mechanical and electrical compressor
failure.
Содержание Danfoss Maneurop MT
Страница 2: ......
Страница 3: ......
Страница 39: ......
Страница 42: ......
Страница 43: ......
Страница 65: ......
Страница 66: ......
Страница 67: ......
Страница 103: ......
Страница 105: ...Maneurop reciprocating compressors NTZ R404A R507 60 Hz Application guidelines http danfoss us com...
Страница 106: ......
Страница 138: ......
Страница 139: ......
Страница 192: ......
Страница 193: ......
Страница 196: ......
Страница 239: ...Danfoss scroll compressors SM SY SZ R22 R407C R134a R404A R507A 50 60 Hz Application guidelines http cc danfoss com...
Страница 240: ......