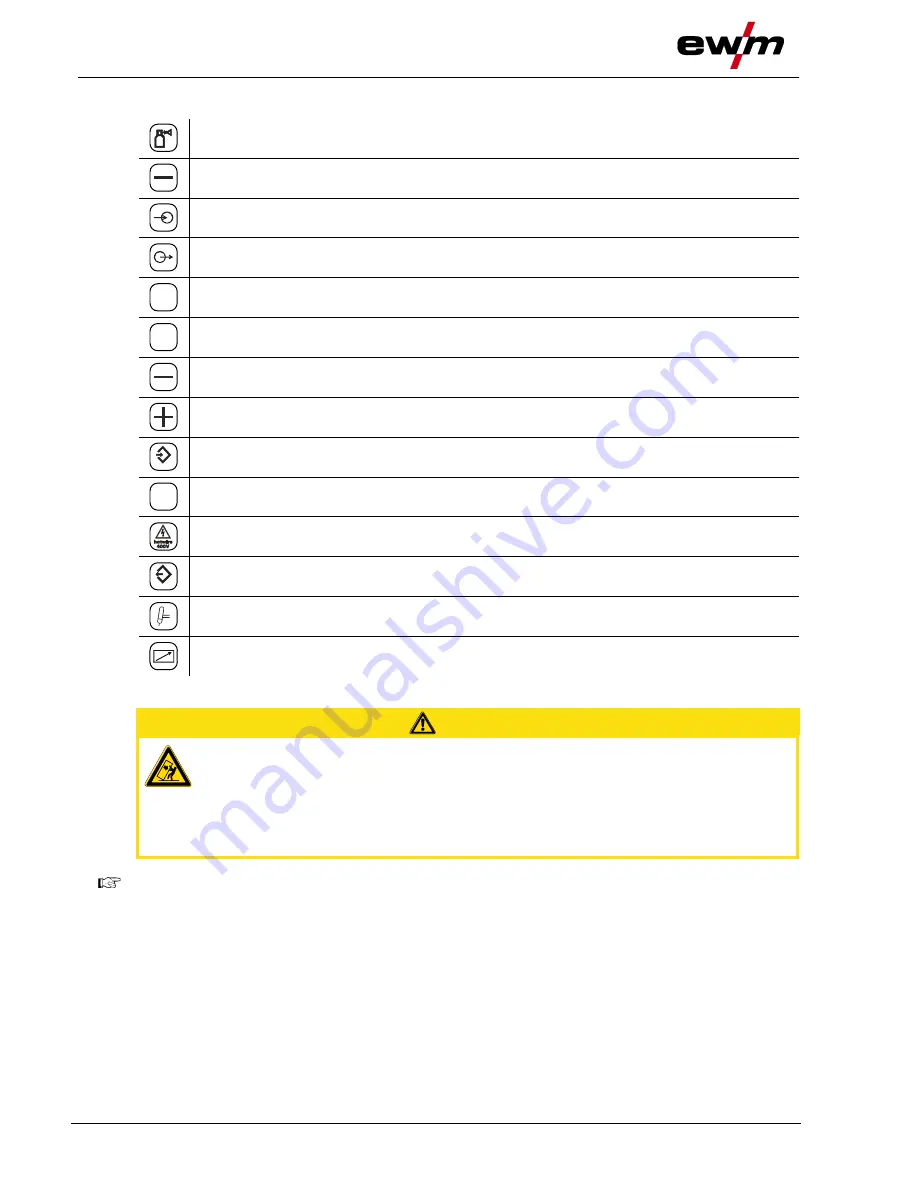
Design and function
TIG cold wire welding
42
099-000115-EW501
17.06.2015
5.9.2
Legend
Shielding gas
Welding current(minus potential)
Coolant input (marked in colour)
Coolant output (marked in colour)
X2
Control lead (28-pole)
TP
Hose package (TP = tube package)
HW
Welding current (minus potential, TIG hot wire)
Welding current (plus potential, workpiece)
hotwire
Control lead, hot wire (signal input, 4-pole)
3~
AC
Connection, supply voltage (3-phase)
Supply voltage, hot wire power source
hotwire
Control lead, hot wire (signal output, 4-pole)
Control lead, welding torch (12-pole)
Remote control connection
5.9.3
Installation
CAUTION
Installation site!
The machine must not be operated in the open air and must only be set up and
operated on a suitable, stable and level base!
• The operator must ensure that the ground is non-slip and level, and provide sufficient
lighting for the place of work.
• Safe operation of the machine must be guaranteed at all times.
In a TIG cold wire welding system the wire feed unit is placed onto the casing cover of the TIG
power source.
Содержание Tetrix 351
Страница 7: ...Contents Notes on the use of these operating instructions 099 000115 EW501 17 06 2015 7...
Страница 22: ...Machine description quick overview Rear view 22 099 000115 EW501 17 06 2015 4 4 Rear view Figure 4 3...
Страница 26: ...Machine description quick overview Rear view 26 099 000115 EW501 17 06 2015 4 7 Rear view Figure 4 5...
Страница 111: ...Design and function Machine configuration menu 099 000115 EW501 17 06 2015 111 EXIT NAVIGATION ENTER l 0 Figure 5 55...
Страница 138: ...Appendix B Overview of EWM branches 138 099 000115 EW501 17 06 2015 11 Appendix B 11 1 Overview of EWM branches...