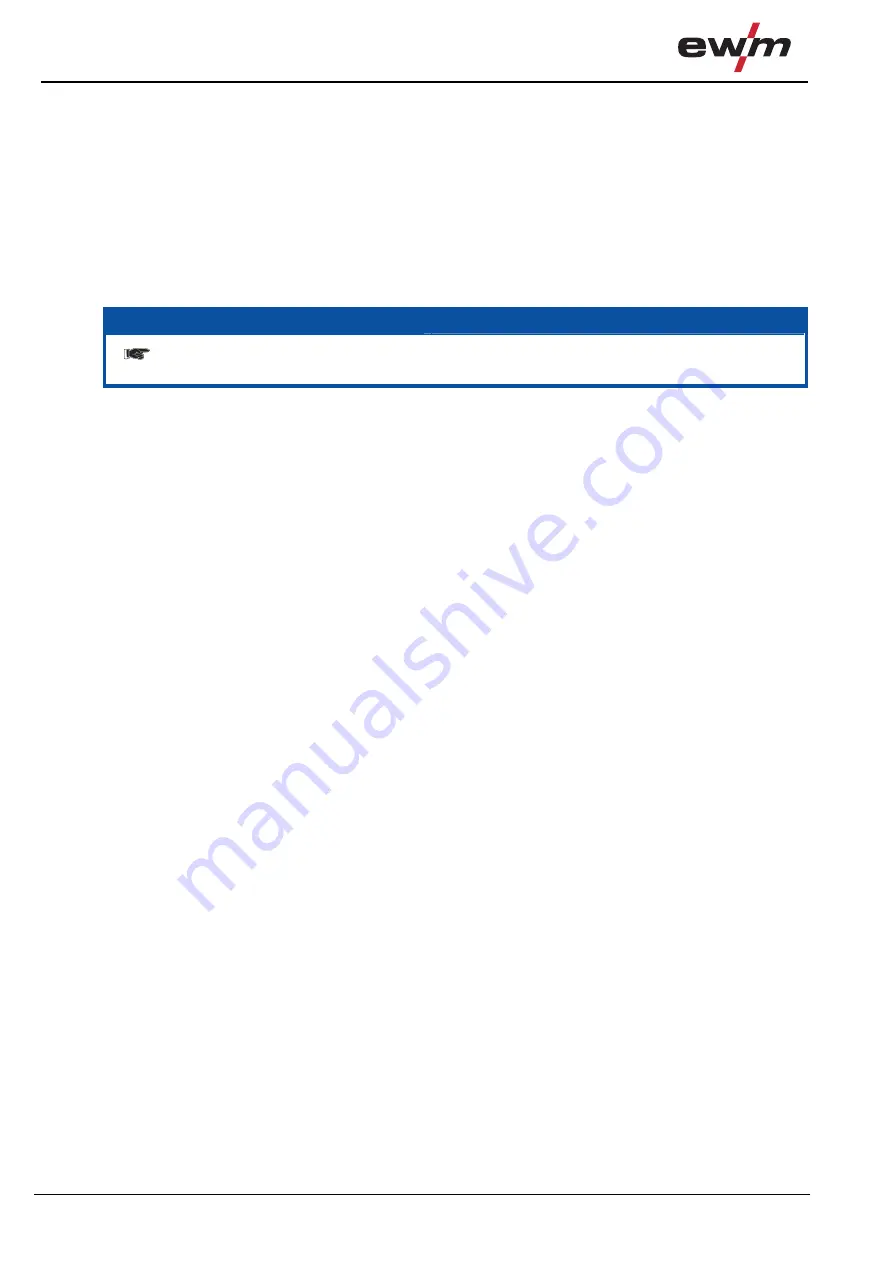
Rectifying faults
Customer checklist
44
099-005084-EW501
22.09.2011
7
Rectifying faults
All products are subject to rigorous production checks and final checks. If, despite this, something fails to
work at any time, please check the product using the following flowchart. If none of the fault rectification
procedures described leads to the correct functioning of the product, please inform your authorised
dealer.
7.1
Customer checklist
Legend
a
: Fault/Cause
#
: Remedy
NOTE
The correct machine equipment for the material and process gas in use is a
fundamental requirement for perfect operation!
Wire feed problems
a
Contact tip blocked
#
Clean, spray with anti-spatter spray and replace if necessary
a
Setting the spool brake (see "Setting the spool brake" chapter)
#
Check settings and correct if necessary
a
Setting pressure units (see "Inching wire electrodes" chapter)
#
Check settings and correct if necessary
a
Worn wire rolls
#
Check and replace if necessary
a
Wire feed motor without supply voltage (automatic cutout triggered by overloading)
#
Reset triggered fuse (rear of the power source) by pressing the key button
a
Kinked hose packages
#
Extend and lay out the torch hose package
a
Wire guide core or spiral is dirty or worn
#
Clean core or spiral; replace kinked or worn cores
Functional errors
a
Machine control without displaying the signal lights after switching on
#
Phase failure > check mains connection (fuses)
a
No welding performance
#
Phase failure > check mains connection (fuses)
a
Various parameters cannot be set
#
Entry level is blocked, disable access lock (see chapter entitled "Lock welding parameters
against unauthorised access")
a
Connection problems
#
Make control lead connections and check that they are fitted correctly.
a
Loose welding current connections
#
Tighten power connections on the torch and/or on the workpiece
#
Tighten contact tip/collet correctly