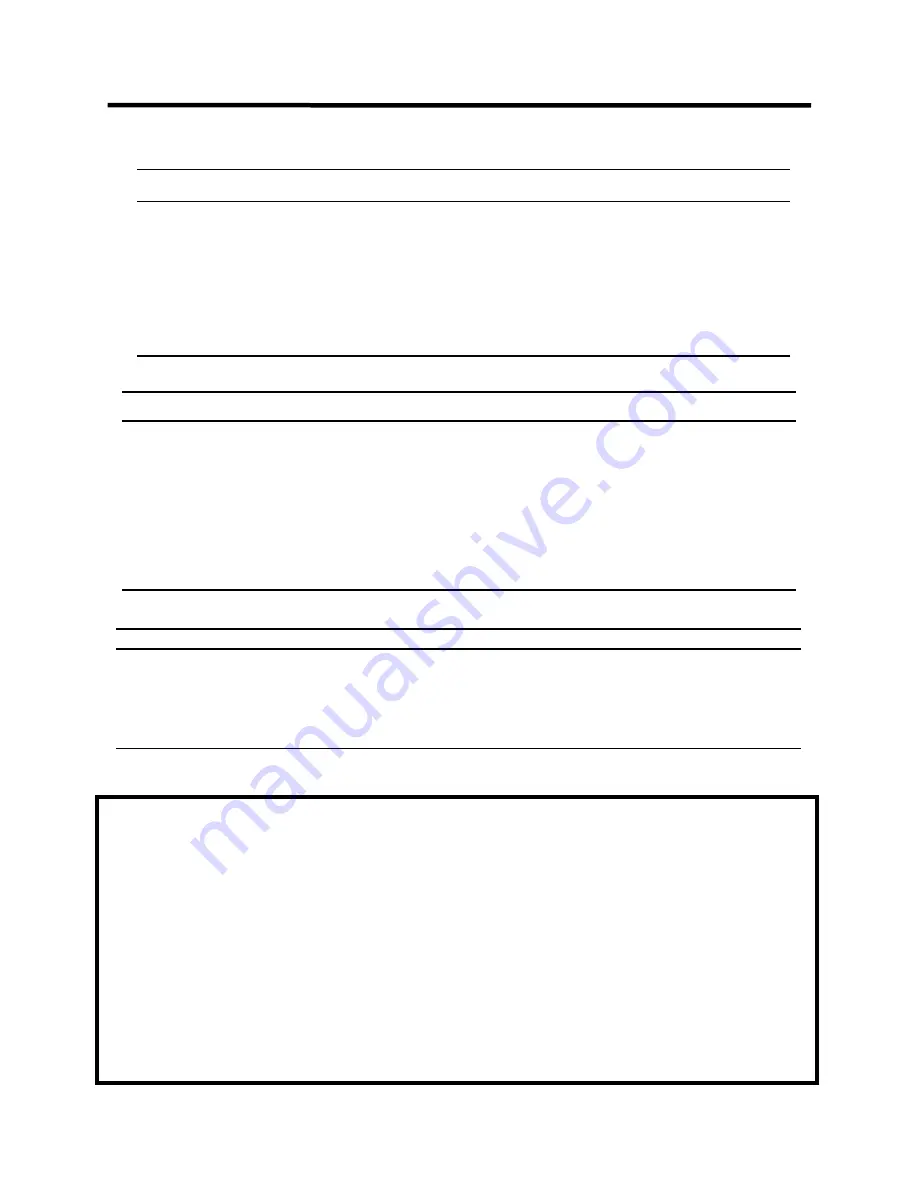
24
PROCESS
TORCH POLARITY
WORK POLARITY
MIG (GMAW)
+
-
FLUX CORE (FCAW)
-
+
STICK (SMAW)
+
-
TIG (GTAW)
-
+ /AC
Table 1
GENERAL POLARITY RECOMMENDATIONS*
*Consult the manufacturer of the filler material recommendations concerning polarity .
PROCESS
GAS
MIG (GMAW) STEEL
80/20 Ar/CO2 or 75/25 Ar/CO2 or 100% CO2 for short Circuit MIG
80% or higher Argon content (recommend: 90/10 CO2 ) or similar content for
true Axial Spray Transfer. See below for basic flow rates.
MIG (GMAW) STAINLESS
98/2 Ar/O2 , 98/2 Ar/CO2, or TriMix/ StainMIX with Helium (20
-
35 CFH)
MIG DUAL SHIELDED
Follow wire manufacturer
’
s recommendations in product literature.
MIG (GMAW) ALUMINUM
100% Argon (35 to 40CFH is usually needed for cleaner welds)
TIG (GTAW) STEEL/STAINLESS
100% Argon (10
-
30 CFH depending upon cup size and welding environment)
TYPICAL GAS SELECTION AND SETTING GUIDE
Table 2
WIRE DIAMETER
WELDING AMPS (A)
PLATE THICKNESS
GAS FLOW RATE
.023” (0.6
mm)
25
-
110
.040”
-
.063” (1.0
-
1.6)
15
-
20 CFH /7
-
10 lpm
.030” (0.8
mm))
35
-
200
.040”
-
.128” (1.0
-
3.2)
20
-
25 CFH/ 10
-
14 lpm
.035” (0.9
mm)
45
-
200 +
.040”
-
.128”.(1.0
-
3.2)
20
-
25CFH/ 10
-
14 lpm
.040” (1.0
mm)
45
-
200+
.050”
-
.25”+(1.2
-
6.0+)
25+ CFH/ 14+ lpm
.045” (1.2
mm)
60
-
200+
.25”+ (6.0+)
25+ CFH/ 14+ lpm
MIG (GMAW) CURRENT/WIRE/SINGLE PASS THICKNESS GENERAL SUGGESTIONS
Table 3
IMPORTANT:
Use the synergic function of the welder if you are unsure of the best volt and wire feed/amp settings to use.
This feature
automatically sets a generally useable volt/amp ratio for you.
After this is selected and wire type and diameter of the wire is selected it is
a simple matter of turning the amps up or down until the arc is stable and the sound of the arc is a crisp frying sound. If no workable setting is
obtained, the volt setting may be selected and adjusted up or down while in synergic mode. Adjusting the volts will reset the volt/amp ratio and
create a whole new range of adjustment capability. Deviating from the standard the shielding gas mix for the metal/wire in MIG mode will
affect how accurate the volt/amp ratio is. The synergic mode provides much better results in general than a chart can provide.
Please note
that in synergic mode, the unit display defaults to read in Amps, not the actual wire feed speed (IPM) while adjusting. This is not
denoted by a separate LED light. Also, note that the unit will default to a relatively low amp setting. This is intentional as the welder
does not compute the thickness of the metal being welded. You will need to adjust the Amps to match the metal thickness yourself.
Displaying in Amps in synergic mode is a more accurate method since the wire diameter and type is entered and actual amps can be pre
-
computed before the gun trigger is activated. While actively welding in manual or synergic modes, both the volt meter and the wire feed/amp
meter will display actual, real time output. There will be some variation in the reading as arc length, angle and even metal cleanliness con-
stantly fluctuate.
Keep in mind that wire feed speed controls amps, but the same wire feed speed feed setting on different diameter
wires will change the amount of amps delivered at the same set feed rate.
Many wire manufacturers provide a range of amps and or
wire speed feed, and volts for their wire type in the printed material in their brochures, packaging information, or in their online information.
Actual suggested wire feed speed/amp and volt ranges may differ somewhat from brand to brand. MIG inductance settings will also affect final
preferred settings. You'll find that settings will vary according to the welding position and joint type. Any recommendation will not be 100%
accurate and can vary widely. For additional help with manual or synergic setup, consider downloading one of the numerous welding apps
available online.
Before adjustment of volts and amps begins, set the inductance to approximately 65
-
75%, then fine tune the induct-
ance only after all fine tuning of volts and amps has been completed. Stainless will usually require around 90 to 100% setting for
inductance for proper wet
-
in of the puddle but that also will vary a little based upon wire class and gas mix. Generally, in spray
mode inductance is not much of a factor, but leave the setting at the recommended settings for short circuit transfer.
Setup Guide and Component Identification
Section 2
Содержание POWER MTS 221STi
Страница 38: ...38 REAR VIEW BACK PANEL POWERMTS 221STi Setup Guide and Component Identification Section 2 1 2 4 3 1x220V 6 5...
Страница 44: ...44 MIG OPERATION where porosity and inclusions can be introduced Basic Theory and Function Section 3...
Страница 66: ...66 24 SERIES MIG TORCH OPT Expanded View Basic Theory and Function Section 3...
Страница 72: ...72...