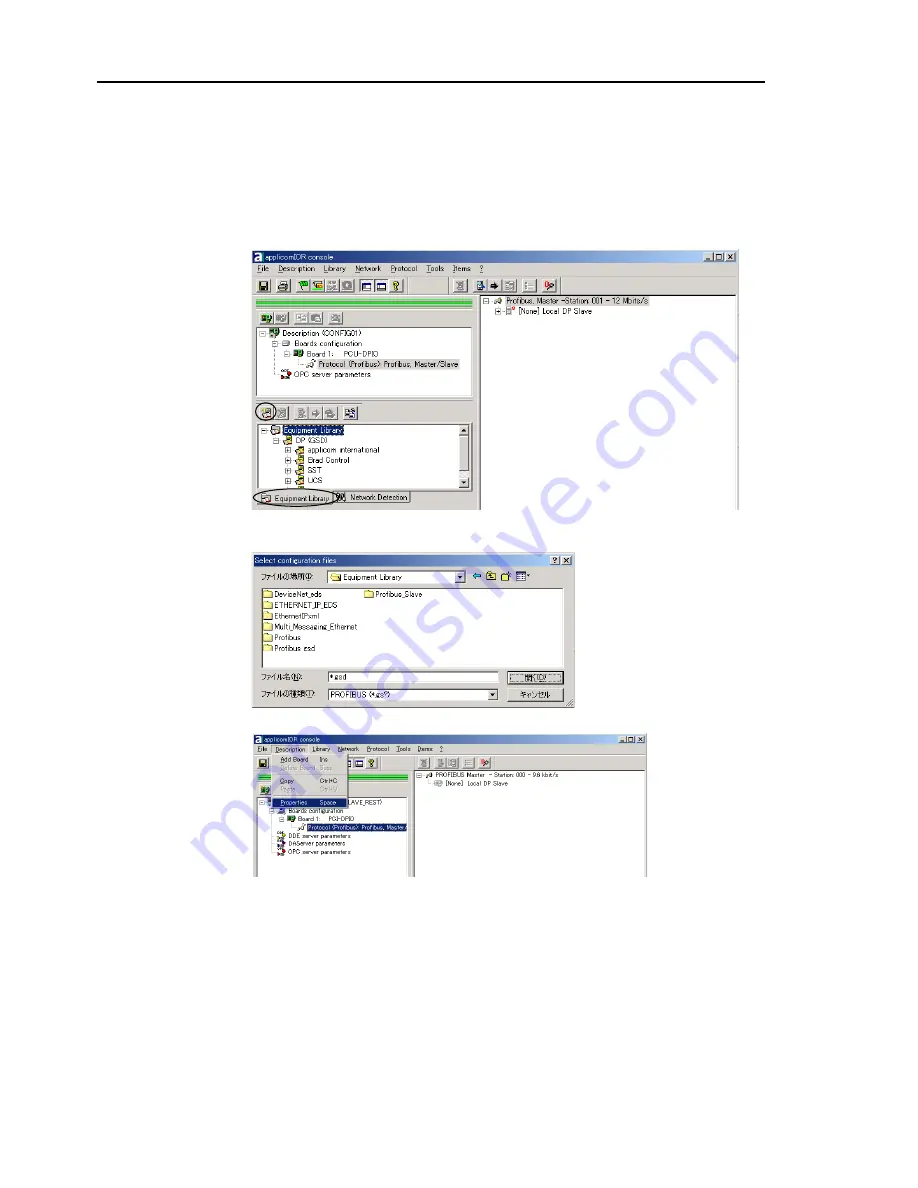
2. Installation
2.8.5 Master Mode
(1) Ensure that the board is connected to the fieldbus. Then, start the applicomIO
console application.
(2) Register the device information (GSD file) that is necessary for the network setup.
Select the [Equipment Library] tab at the center of the dialog’s right side and click
the
Add
icon.
(3) Following dialog appears. Specify the GSD file that is supplied from the device
manufacturer.
(4) Select
Description
|
Properties
.
46
Fieldbus I/O Rev.6
Содержание EM07ZS1647F
Страница 1: ...Rev 6 EM07ZS1647F EPSON RC Option Fieldbus I O ...
Страница 2: ...E PSON RC Option Fieldbus I O Rev 6 ...
Страница 8: ...vi Fieldbus I O Rev 6 ...
Страница 11: ...Table of Contents 5 Maintenance Parts List 151 Appendix A applicomIO Upgrade 153 Fieldbus I O Rev 6 ix ...
Страница 12: ...Table of Contents x Fieldbus I O Rev 6 ...
Страница 80: ...2 Installation 68 Fieldbus I O Rev 6 ...
Страница 88: ...3 Operation 76 Fieldbus I O Rev 6 ...
Страница 164: ...5 Maintenance Parts List 152 Fieldbus I O Rev 6 ...
Страница 168: ...Appendix A applicomIO Upgrade 156 Fieldbus I O Rev 6 ...