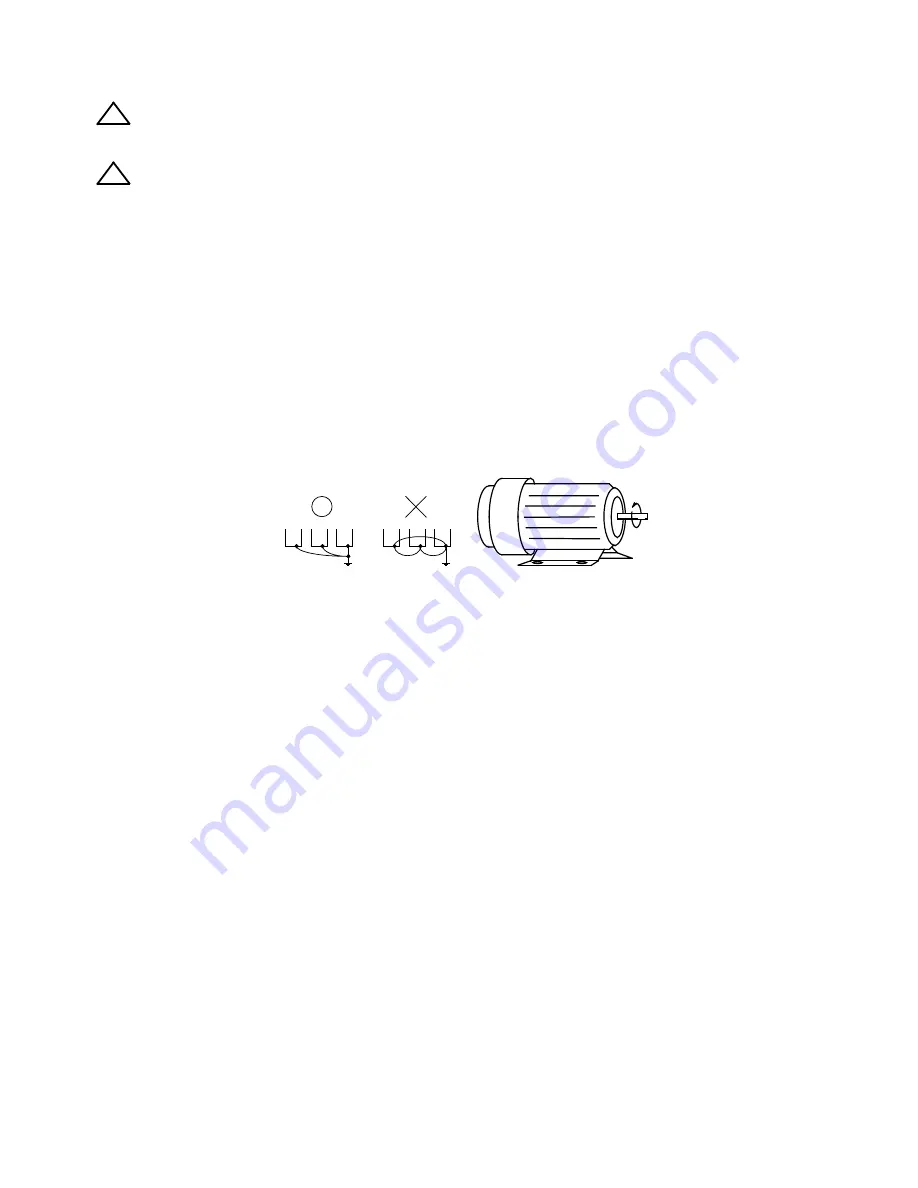
6
Wiring Notes: PLEASE READ PRIOR TO INSTALLATION.
1.
!
CAUTION:
Do not connect the AC input to any of the U/T1, V/T2, W/T3 terminals, as it will
damage the AC drive.
2.
!
WARNING:
Ensure all screws are tightened to the proper torque rating.
3. During installation, follow all national and local electrical, construction, and safety codes for the
country the drive is to be installed in.
4. Ensure the appropriate protective devices (circuit breaker or fuses) are connected between the
power supply and AC drive.
5. Make sure that the leads are connected correctly and the AC drive is properly grounded. (Ground
resistance should not exceed 0.1
Ω
.)
6. Use ground leads that comply with AWG/MCM standards and keep them as short as possible.
7. Multiple VFD-L units can be installed in one location. All the units should be grounded directly to
a common ground terminal. The VFD-L ground terminals may also be connected in parallel, as
shown in the figure below.
Ensure there are no ground loops.
Forward
running
8.
When the AC drive output terminals U/T1, V/T2, and W/T3 are connected to the motor terminals
U, V, and W, respectively, the motor will rotate counterclockwise (as viewed from the shaft ends
of the motor) when a forward operation command is received. To reverse the direction of motor
rotation, switch over any of the two motor leads.
9. Make sure that the power is capable of supplying the correct voltage and required current to the
AC drive.
10. Do not attach or remove wiring when power is applied to the AC drive.
11. Do not monitor the signals on the circuit board while the AC drive is in operation.
12. Route the power and control wires separately, or orthogonal to each other.
13. If a filter is required for reducing EMI (Electro-Magnetic Interference), install it as close as
possible to AC drive. EMI can also be reduced by lowering the Carrier Frequency.
14. If the AC drive is installed in the place where a load reactor is needed, install the filter close to
U/T1, V/T2, W/T3 side of AC drive. Do not use a Capacitor or L-C Filter (Inductance-Capacitance)
or R-C Filter (Resistance-Capacitance).
15. When using a GFCI (Ground Fault Circuit Interrupt), select current sensor with minimum current
200mA, and minimum detection time 0.1-second to avoid nuisance tripping.