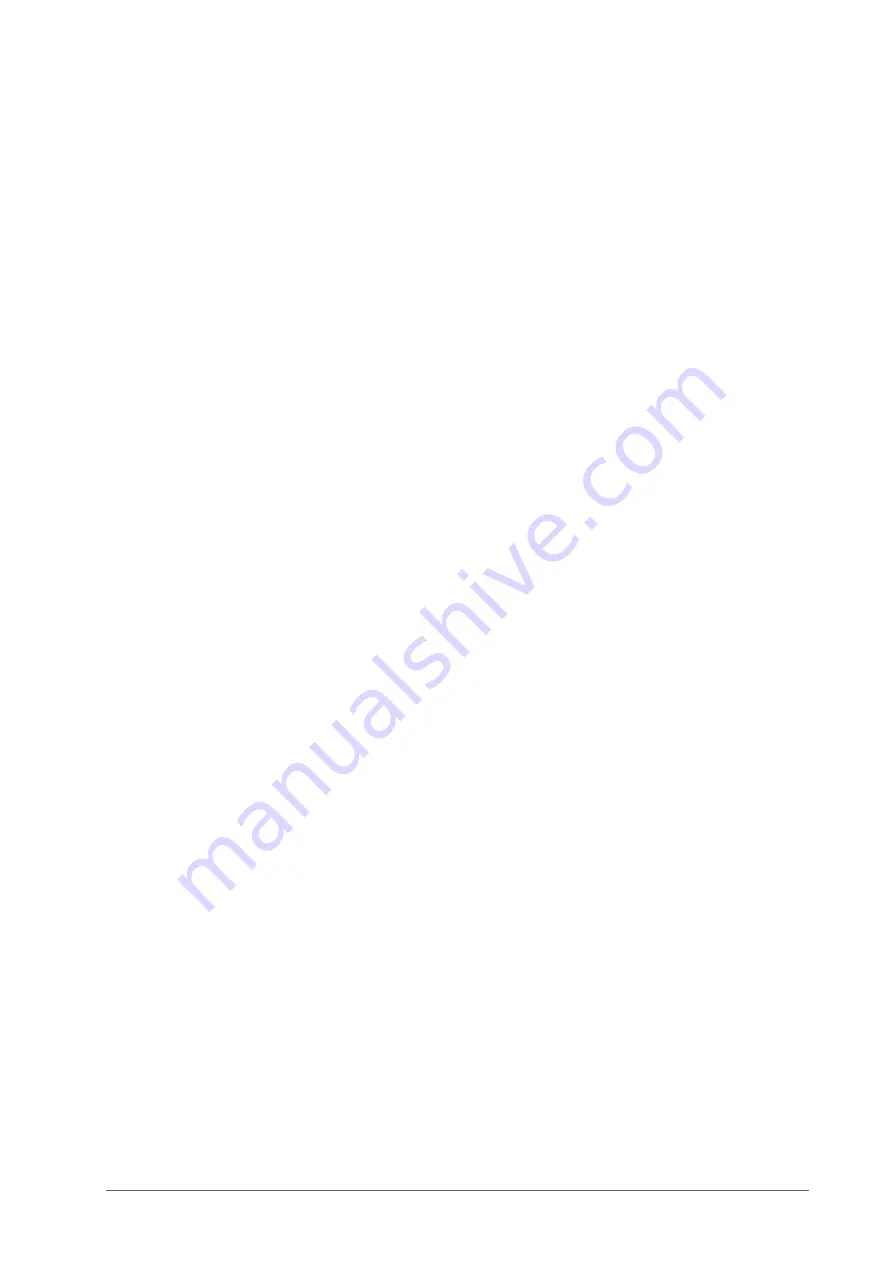
Users’ Manual
EDI-53 Series Digital Indicator
Page
|
9
what is known as suppressed zero or elevated zero. The measuring range of the transducer is known as
Span. Discussion of these technical issues is not within the scope of this manual. However, gauge factor
calculation for simpler transducers which provide 4 mA output at zero input is discussed below.
If a 4 – 20 mA current loop output transducer is calibrated to read 4 mA with zero input and M units
(engineering units) at 20 mA, the gauge factor of the transducer should be calculated as follows.
G = M / 0.8
[Eqn. 3.3.3]
and R
0
, in Eqn. 3.3.1 should be taken as 0.200 V if the zero-input reading cannot be determined at
installation time.
Users may consult Encardio-rite for determination of gauge factors of transducers with zero suppression
or elevation and/or cases where a constant offset need to be added to the measured parameter.
Although the internal ADC of the indicator has a full-scale resolution of 20,000 counts, it is recommended
that the display resolution of the engineering units display be limited to 2000 counts full scale only. This
will avoid fluctuation in the measured value due to induced noise on the transducer signal cables. Also,
because most of the transducers for Geotechnical application will not have an accuracy and resolution
better than 0.1% of full scale, a higher display resolution will not provide any additional benefit.
The EDI-53 provides an easy way of controlling the precision (or resolution) of the calculated engineering
units value. The setup process allows the user to specify the number of decimal places up to which the
result should be displayed.
3.4
Non-linearity correction using polynomial calculation
Transducers are generally so designed that their output is directly proportional to the measured
parameter. However, this assumption is not true if a very high level of accuracy is desired. At higher
resolutions the relationship does become sufficiently non-linear and other methods have to be found to
get better accuracies. The deviation (or error) of the measured value from its ideal straight-line value is
known as the non-linearity error of the transducer.
The traditional method of correcting errors due to non-linearity was to calibrate each transducer in the lab
and use the calibration curve to correct the obtained readings. Due to limitation of the graphical methods
a look up table in numerical format is generally tabulated. This method involves an amount of calculation
by the user and is not suitable for automated data collection.
If errors due to repeatability and hysteresis of any non-linear transducer is smaller than the desired
accuracy limits then polynomial calculation method can often be used to calculate the parameter value to
a better accuracy than possible using a linear approximation.
For example, if a load cell has a non-linearity error of say 0.3% using a linear approximation it may be
possible to get an accuracy better than 0.1% using polynomial calculation provided errors due to its
repeatability and hysteresis is less than 0.05%.
A second order polynomial takes the form
Y = AX
2
+ BX + C
[Eqn. 3.4.1]
where, in our case, X is the voltage measured by EDI-53 (i.e. the voltage shown on indicator display) and
Y is the value of the measured parameter in engineering units. A, B and C are three polynomial
constants.
The polynomial constants A, B and C are determined by Encardio-rite during calibration of individual
transducers and is mentioned in the corresponding test reports. However, the polynomial constants are
only available for higher accuracy transducers.