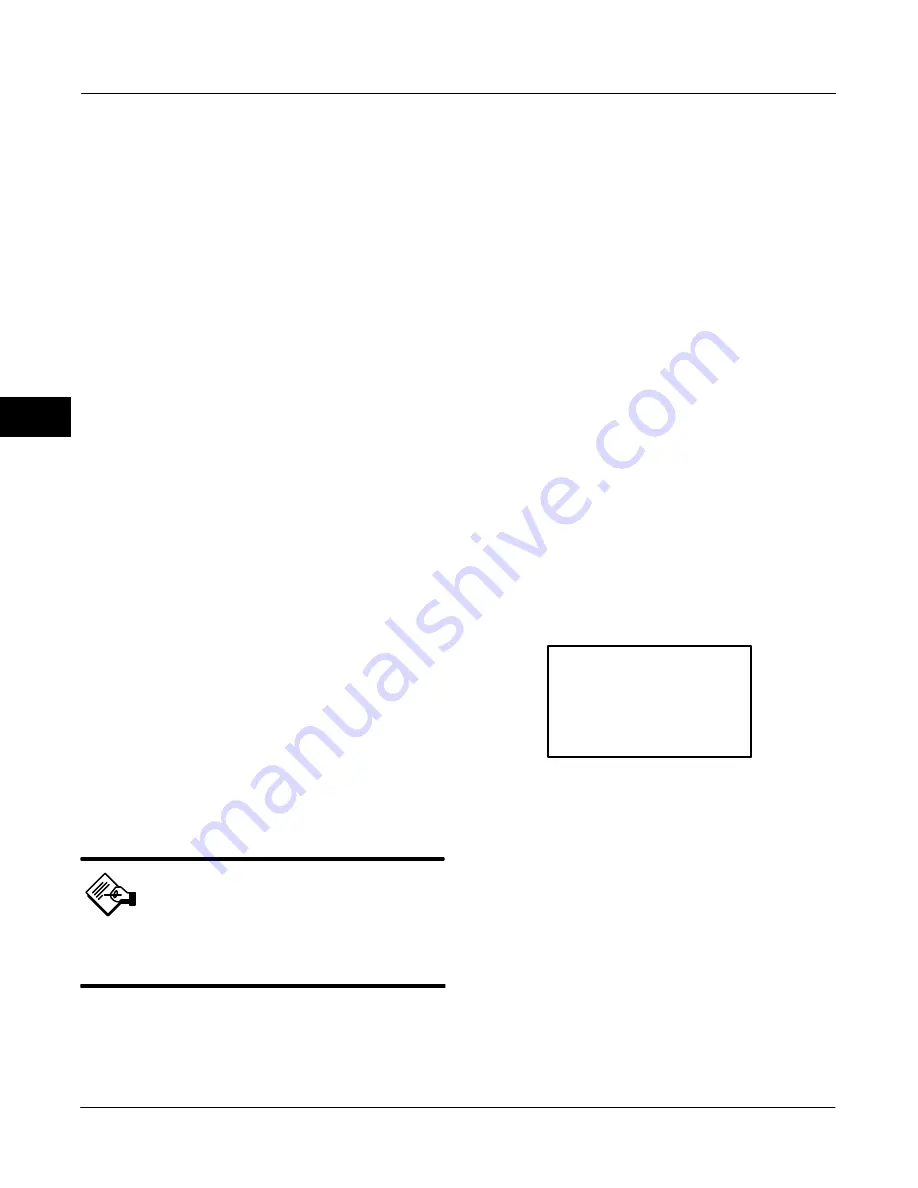
DVC6000 Digital Valve Controllers
September 2013
5-6
12. Place the instrument In Service and verify that the
travel properly tracks the current source.
Touch-Up Travel Calibration
Once the travel is calibrated by performing either the
Auto or Manual Calibration procedure, the travel
calibration can be “touched-up” by shorting the
Auxiliary Terminal Connections for 3 to 5 seconds to
activate Touch-Up Calibration. Touch-Up Travel
Calibration uses Last Value for the crossover
adjustment. You can abort the procedure by shorting
the auxiliary terminals for 1 second.
To enable Touch-Up Travel Calibration the Aux
Terminal Mode must be set to Auto Calibration. The
instrument Operational Status during calibration is
Calibration in Progress.
Use Touch-Up Calibration to calibrate the digital valve
controller travel whenever the I/P converter or relay is
replaced. Do not use Touch-Up calibration for initial
calibration when mounting the instrument on an
actuator, or if the travel sensor assembly or printed
wiring board assembly was replaced.
You can use Touch-Up Travel Calibration to calibrate
the digital valve controller if you suspect calibration
has changed due to drift. However, prior to initiating
Touch-Up Travel Calibration, perform a Valve
Signature diagnostic test, using ValveLink software.
This will capture the as-found data for future root
cause analysis.
Sensor Calibration
Pressure Sensors (1-3-2-1)
There are three pressure sensors: output A, output B
and supply. Select the appropriate menu depending
upon which pressure sensor you are calibrating.
Note
The pressure sensors are calibrated at
the factory and should not require
calibration.
Output Pressure Sensor Calibration
To calibrate the output pressure sensors, connect an
external reference gauge to the output being
calibrated. The gauge should be capable of measuring
maximum instrument supply pressure. From the
Calibrate menu, select Sensor Calibration and Press
Sensors. Depending upon the sensor you wish to
calibrate, select either Output A Sensor or Output B
Sensor. Follow the prompts on the Field
Communicator display to calibrate the instrument’s
output pressure sensor.
1. Adjust the supply pressure regulator to the desired
supply pressure. Press OK.
2. Select a) Zero only, or b) Zero and Span (gauge
required) sensor calibration.
a. If Zero only calibration is selected, wait until
output x pressure has completely exhausted, then
continue. Once calibration is completed, go to step
6. The output x pressure corresponds to A or B,
depending on which output you are calibrating.
b. If Zero and Span calibration is selected, wait
until output x pressure has completely exhausted,
then continue. You will then be asked to wait until
output x pressure has reached full supply, then
continue. The output x pressure corresponds to A
or B, depending on which output you are
calibrating. Proceed with step 3.
3. The instrument sets the output pressure to full
supply. The following message appears:
Use the Increase and
Decrease selections
until the displayed
pressure matches the
output x pressure.
The output x pressure corresponds to A or B,
depending on which output you are calibrating. Press
OK when you have read the message.
4. The value of the output pressure appears on the
display.
5. From the adjustment menu, select the direction and
size of adjustment to the displayed value. Selecting
large, medium, and small adjustments causes
changes of approximately 3.0 psi/0.207 bar/20.7 kPa,
0.30 psi/0.0207 bar/2.07 kPa, and 0.03 psi/0.00207
bar/0.207 kPa, respectively. Adjust the displayed value
until it matches the output pressure, select Done and
go to step 6.
6. Place the instrument In Service and verify that the
displayed pressure matches the measured output
pressure.
5
Содержание Fisher FIELDVUE DVC6000
Страница 2: ......
Страница 22: ...DVC6000 Digital Valve Controllers September 2013 1 12 1 ...
Страница 82: ...DVC6000 Digital Valve Controllers September 2013 4 22 4 ...
Страница 94: ...DVC6000 Digital Valve Controllers September 2013 5 12 5 ...
Страница 139: ...Loop Schematics Nameplates September 2013 B 1 B B Appendix B Loop Schematics Nameplates B ...
Страница 161: ......