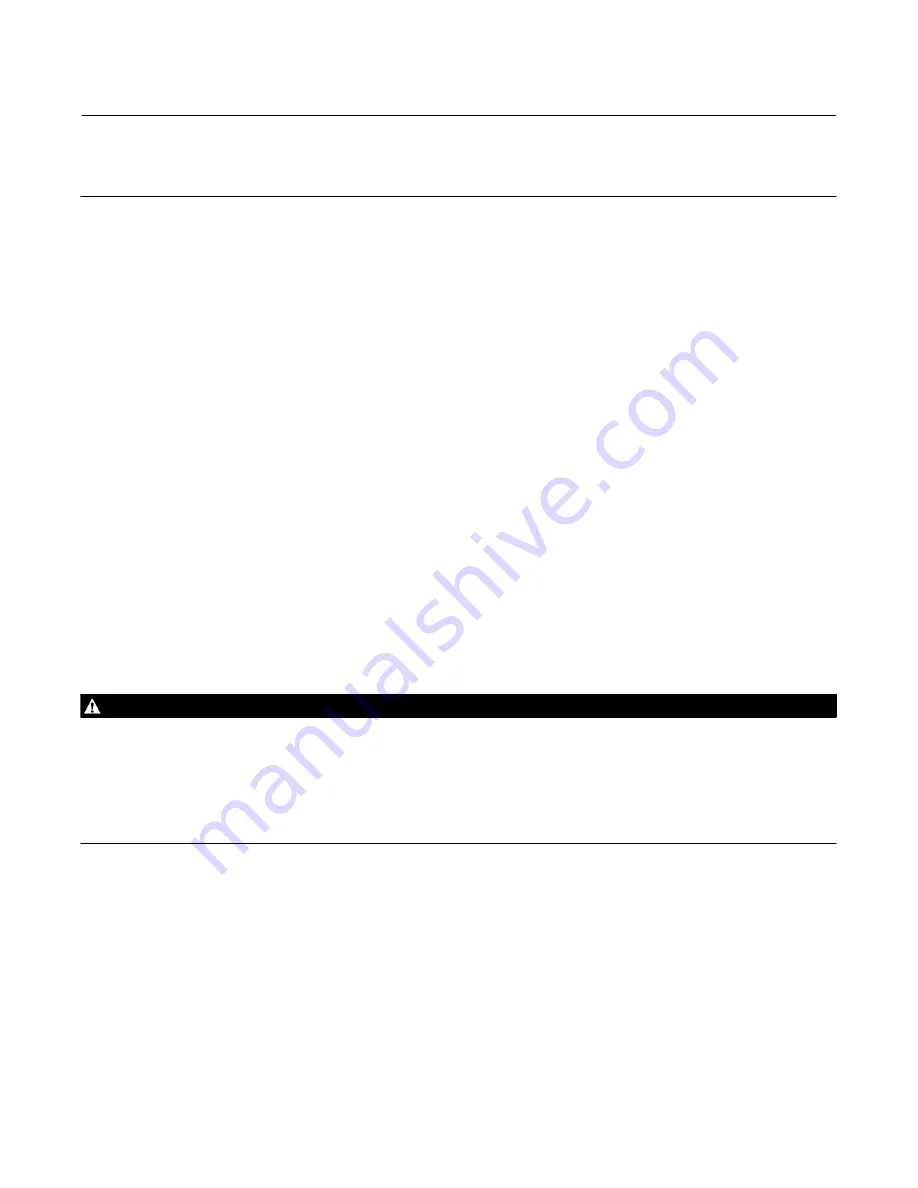
Instruction Manual
D200163X012
4660 Pressure Pilot
June 2017
10
micrometers in diameter will suffice in most applications, check with an Emerson Automation Solutions field office and
industry instrument air quality standards for use with corrosive gas or if you are unsure about the proper amount or
method of air filtration or filter maintenance.
Supply pressure medium must be clean, dry, and noncorrosive, and meet the requirements of ISA Standard 7.0.01 or
ISO 8573-1. A maximum 40 micrometer particle size in the air system is acceptable. Further filtration down to 5
micrometer particle size is recommended. Lubricant content is not to exceed 1 ppm weight (w/w) or volume (v/v)
basis. Condensation in the supply medium should be minimized.
Use a suitable filter regulator, such as the 67CFR regulator with standard 5 micrometer filter, to remove solid particles
and to maintain the supply pressure source within the normal operating range of 1.4 to 4.4 bar (20 to 65 psig). Refer to
table 1 for the pilot supply flow requirement (relay construction only). As shown in figure 4, connect supply pressure to
the connection marked SUPPLY on the bottom of the pilot case.
Process Pressure
Connect process pressure to the connection marked PROCESS on the bottom of the pilot case as shown in figure 4.
When installing process pressure piping, follow accepted practices to ensure accurate transmission of the process
pressure to the pilot. Install shutoff valves, vents, drains, or seal systems as needed in the process pressure line. Install
a needle valve in the process pressure line to dampen pulsations.
Output Pressure
Connect output pressure piping to the connection marked OUTPUT on the bottom of the pilot case as shown in figure
4. Refer to the appropriate control valve or actuator instruction manual to complete the connection of output pressure
piping from the pilot to the loading connection of the control valve actuator.
Vent
WARNING
Personal injury or property damage could result from fire or explosion of accumulated gas, or from contact with hazardous
gas, if a flammable or hazardous gas is used as the supply pressure medium. Because the instrument case and cover
assembly do not form a gas‐tight seal when the assembly is enclosed, a remote vent line, adequate ventilation, and
necessary safety measures should be used to prevent the accumulation or flammable or hazardous gas. A remote vent pipe
alone cannot be relied upon to remove all flammable and hazardous gas.
Vent line piping should comply with local and regional codes, should have adequate inside diameter, and should be be as
short as possible to reduce case pressure buildup.
If a remote vent is required, use 19 mm (3/4‐inch) (minimum inside diameter) pipe for runs up to 6.09 meters (20
feet). For vent piping runs from 6.09 to 30.5 meters (20 to 100 feet), use 25.4 mm (1‐inch) (minimum inside diameter)
pipe. Remove the vent screen (key 20, figure 8) and install a remote vent pipe to exhaust the vented gas to a safe,
well‐ventilated area. The vent, as shown in figure 8, or the end of a remote vent pipe must be protected against the
entrance of all foreign matter that could block the vent. Check the vent periodically to be certain it is not plugged.
Operating Information
For high‐only and low‐only constructions, perform the procedures that are outlined in the adjustments portion of this
section. For high‐only constructions, perform only those procedures that pertain to setting and checking the high set