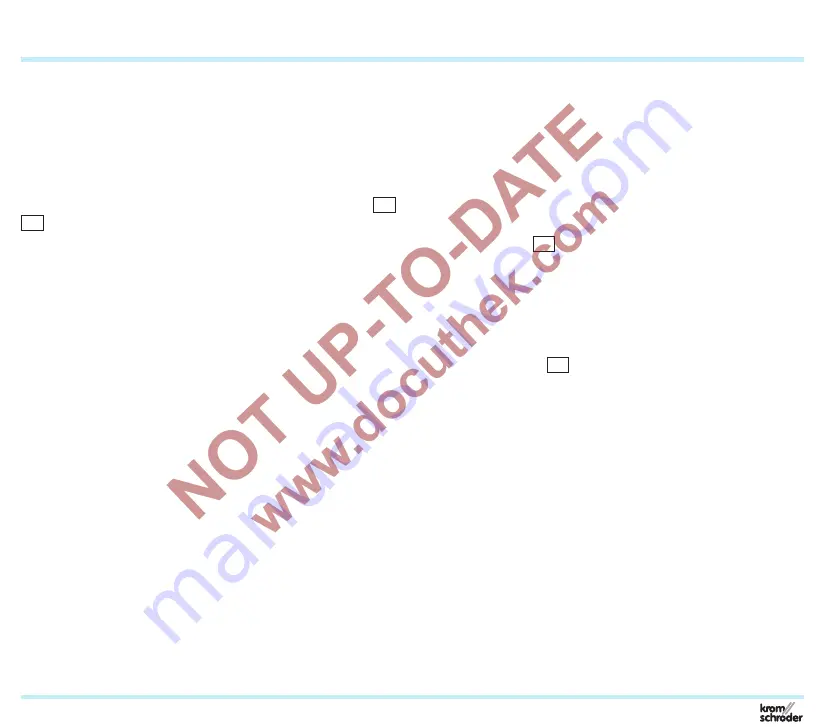
BCU 480 · Edition 06.07
39
Air valve control on BCU . .L
5 .7
Parameter 30, Behaviour of the air valve during operation.
Parameter 31, Behaviour of the air valve during start-up.
Parameter 32, Behaviour of the air valve in the event of a
fault lock-out.
The BCU..L features an adjustable air valve control. The display
shows that purging is currently being carried out with
P 0
.
A
indicates that the air valve is being activated for cooling
or heating.
The BCU..L supports the following functions:
– Purge
– Cooling in start-up position/standby
– Switching of the burner between low and high burner out-
put during operation via the air valve.
– To start up the burner as intended, external activation of
the air valve can be blocked during start-up (prevents
synchronisation problems between the BCU and the cen-
tral control system).
– Setting the air valve parameters, so that it
– opens with valve V1
– opens with valve V2
– opens once the main burner has reached its operating
position
– Low fire over run time t
KN
after a normal shut-down
Purge
5 .7 .1
In the case of multiple burner applications, burners with me-
chanical combustion air supply are used. The air for combus-
tion and pre-purge is supplied by a central fan controlled by
a separate logic. This logic determines the purging time.
The BCU..L supports centrally-controlled pre-purge or post-
purge. The BCU..L is informed that purging is currently being
performed by input 22. It then opens the air valve, regardless
of the status of the other inputs (purging has priority). The
display indicates
P 0
.
For purging, the safety interlock (limits) must activate input 5
and input 22 of the BCU.
Cooling in start-up position/standby
5 .7 .2
The air valve can be activated externally via input 23 for cool-
ing in the start-up position. During activation of the air valve
the display shows
A 0
, indicating that cooling is currently
being carried out.
Burner start
5 .7 .3
Parameters 30 and 31 determine the behaviour of the air valve
during burner start.
Parameters