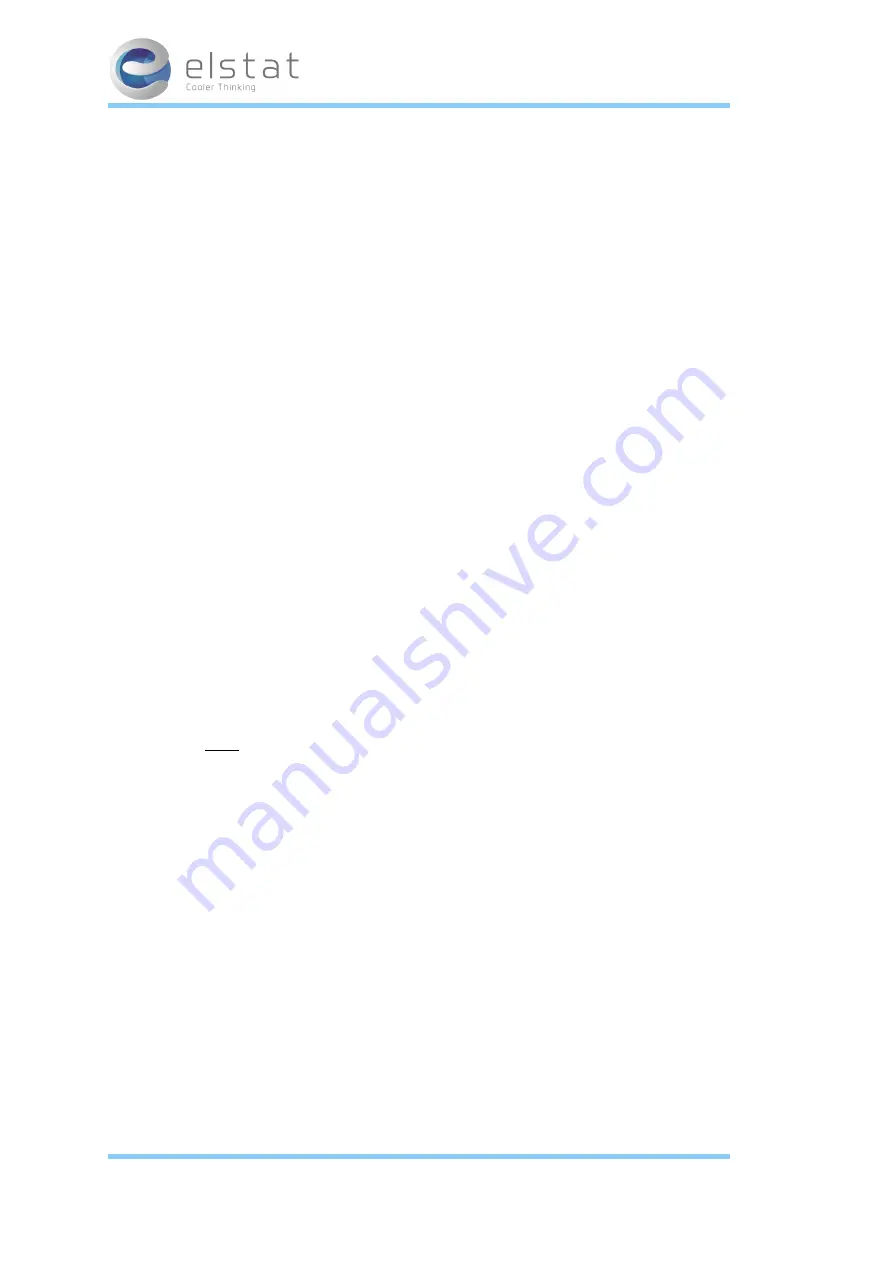
l
Passing peak current through the windings of the compressor motor
l
Switching off the refrigeration system on the thermal overload protection
l
Short-cycling the refrigeration system.
However, if
ready mode
and
saving mode
differential temperatures are too small or if the compressor
rest time (
rt
) is too short, the EMS controller cycles the compressor on the compressor rest time
(
rt
) as the compressor rest time (
rt
) overrides the differential temperatures.
If the compressor runs continuously for too long without reaching the set point (
S P
) temperature, a
refrigeration system failure (
rS F
) alarm activates alerting to possible problems with the refrigeration
system.
EMS controllers can monitor the refrigeration system temperature using a condenser sensor. Mon-
itoring the refrigeration system temperature can help detect problems, such as a blocked con-
denser.
If the temperature measured on the condenser sensor reaches the condenser high temperature
(
C t
), the EMS controller disables the compressor and activates the (
Ht
) alarm. The condenser high
temperature (
C t
) is set by measuring the refrigeration system temperature when the condenser is
75% blocked.
EMS controllers manage the failure of a temperature sensor as follows:
l
Appliance sensor failures indicated by
PF1
alarms, EMS controllers stop running the compressor and then
waits 60 seconds before rebooting (switch off and then switch on).
If the fault continues, the EMS controller repeats and continues the cycle.
l
Condenser sensor failures indicated by
PF2
alarms, EMS controllers continue running the compressor. EMS
controllers alternate the display between
PF2
and the appliance sensor temperature.
l
For evaporator failures indicated by
PF3
alarms, EMS controllers continue running the compressor. EMS con-
trollers alternate the display between
PF3
and the appliance sensor temperature.
Note:
l
Ht alarms do not apply to CO2 coolers
For more information about the parameters used in
compressor management
:
l
See "Refrigeration system failure (Ct)" on page 72
l
See "Differential (dIF)" on page 67
l
See "Compressor rest time (rt)" on page 71
l
See "Set point (SPC or SPF)" on page 67
l
See "Saving set point (SSP)" on page 68
For trouble shooting information:
l
See "How to troubleshoot refrigeration system failure (rSF) alarms" on page 62
l
See "How to troubleshoot temperature sensor alarms" on page 63
5.6
Product temperature
EMS controllers manage the product temperature. EMS controllers use an appliance sensor to meas-
ure the air temperature of the refrigeration compartment.
The location of the appliance sensor within the refrigeration compartment depends on the cooler
type.
35 of 86
27 February 2014