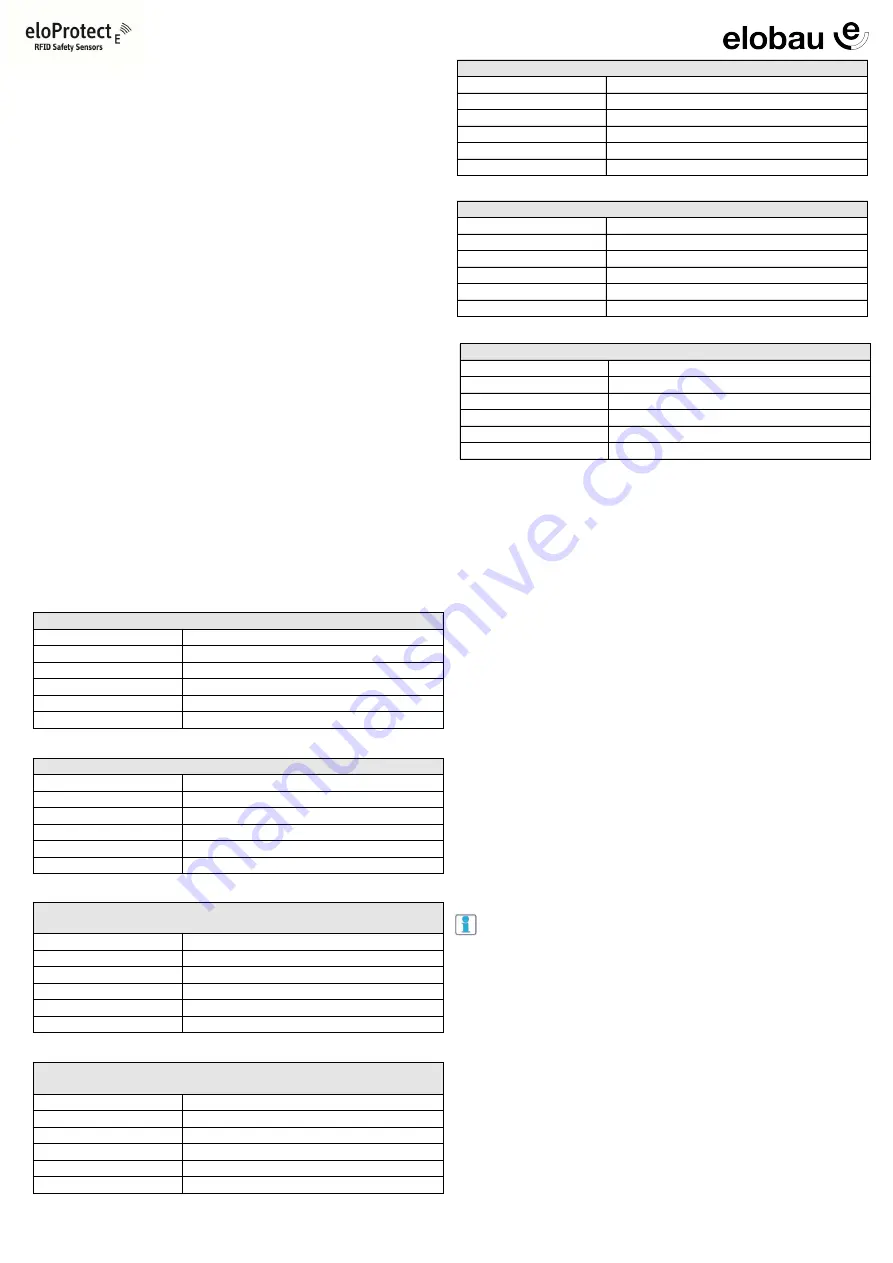
Art.-Nr./Art. No./Réf./N° art/N° art.: 9010017B01M
Version:
1.0
Date:
25.05.2016
3/15
165ESK...
Wiring examples can be found on page
12.
7.4
EDM input
The EDM input can be configured as "automatic" or "monitored" (see number
key).
If the EDM input is not required, the "automatic" variant must be selected and
connected to +24 V DC.
EDM input: automatic
For contactor monitoring, the open contactors must be connected to the EDM
input.
For series connection of multiple sensors all EDM inputs must be connected
to +24 V DC. The monitor for the contactors must be connected to the last sen-
sor of the chain.
Wiring examples can be found on page
12.
EDM input: monitors (start button)
Connect the EDM input to an external start button on your machine control.
The EDM input is only then recognized as set properly if after pressing the
sensor and after setting the safety inputs at least one valid start pulse is
detected.
The valid start pulse is detected when after a rising edge, a falling edge within
the allowable start pulse duration between 30 ms and 5 s is detected.
Wiring examples can be found on page
12.
7.5
Diagnostic output
The diagnostic output is positive switching, short-circuit protected and trans-
mits the various sensor states with different signals, for example, to a PLC.
The pulsed signals correspond to the timing of the yellow LED.
The various symbols are described in more detail under point 7.6.
7.6
LED displays, flash codes and clocking diagnostic output
Sensor non-actuated
LED green
off
LED red
off
LED yellow
on
Diagnostic output
0 V
Safety outputs
0 V
Note
Voltage is applied
Actuator in the detection area (sensor activated), all inputs correctly set
LED green
on
LED red
off
LED yellow
off
Diagnostic output
24 V DC
Safety outputs
24 V
Note
Actuator in the detection area
Actuator in the detection area (sensor actuated),
safety inputs not set (low level)
LED green
flashes
1)
LED red
off
LED yellow
off
Diagnostic output
24 V DC
Safety outputs
0 V
Note
Set safety inputs
Actuator in the detection area (sensor actuated),
safety inputs set (high level), waits for start pulse
LED green
rapid flashes
2)
LED red
off
LED yellow
off
Diagnostic output
24 V DC
Safety outputs
0 V
Note
Press Start button
Actuator at the reception limit
LED green
off
LED red
off
LED yellow
flashes
1)
Diagnostic output
24 V DC clocked
Safety outputs
Previous state
Note
Readjust sensor
Teach-in process
LED green
off
LED red
off
LED yellow
rapid flashes
2)
Diagnostic output
24 V DC clocked
Safety outputs
0 V
Note
Disconnect voltage to complete teach-in
1)
Flashing: The pulse intervals of the LED ratio is 1:1.
2)
Rapid flashing: The pulse intervals of the LED ratio is 1: 4.
Fault condition
LED green
off
LED red
flashes
1)
LED yellow
off
Diagnostic output
0 V
Safety outputs
0 V
Note
See "Troubleshooting" on page 9.
7.7 Boundary area monitoring
If the actuator is in the boundary area of the switching distances with corre-
sponding offset values of the sensor, it is transmitted to a PLC or indicated by
the LED (see point 7.6).
8
Technical specifications
See Technical specifications from page 24.
9
Assembly
- Safety sensor and actuator
do not use as a stopper
external fields can affect switching distances
- Installation of the safety sensor and the associated actuator is allowed only
when de-energized.
-
-
Make sure that the markings on the sensor and actuator face each other
congruently.
The mounting position is arbitrary. However, security sensor and actuator
must be mounted parallel and opposite each other.
- Note the specified installation tolerances and the approved control options.
The specified operating distance around the free zone must be maintained
(free of electrically and magnetically conductive materials).
Matching spacer plates for mounting on metal parts are available
under the order no. 350005 (8 mm) and 350008 (10 mm) from elobau.