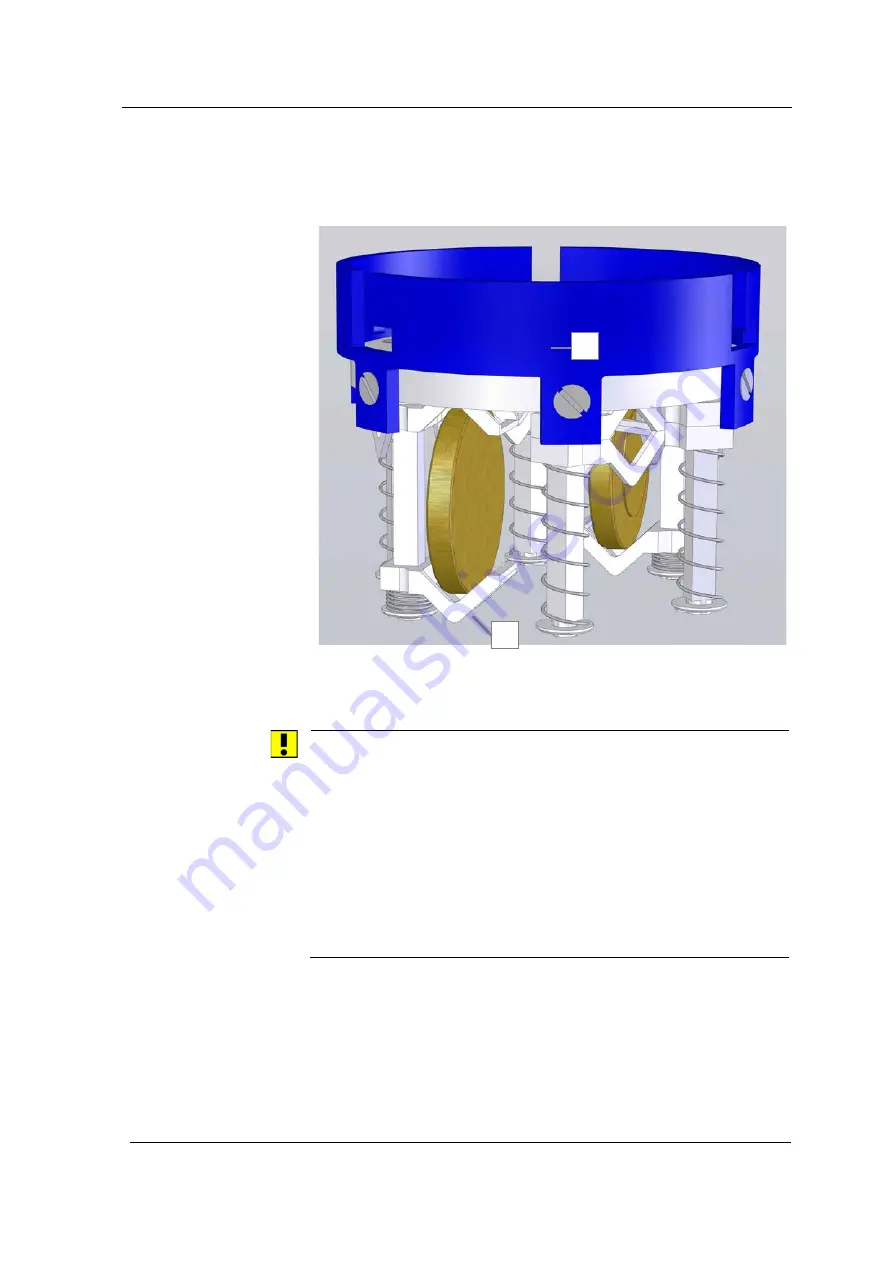
Daily cleaning operation
26
BA_Elmasolvex_SE_EN_Vers. 03.2018
© Elma Schmidbauer GmbH
Movement holder
Grub screw
for fastening the mounting to the drive shaft.
Correct fastening must be checked regularly (see
Chapter
Maintenance 8.2.1)
.
Fig. 6.3.2. Movement holder with clamped parts (simplified display).
Pull the retaining clips (
Fig. 6.3.2.E.
) apart and clamp the
movement or PCB.
Note the following instructions (and in
Chapter 3.6. Technical
Data
) before loading the movement holder in order to prevent
damage to the product to be cleaned and cleaning machine:
The maximum load weight of the movement holder with
cleaning parts is 60 grams.
Also note the maximum capacity of the retaining clips.
Pay attention to even loading to avoid unbalance and
vibrations.
Also secure difficult to clamp parts with, for example, a suitable
solvent-resistant rubber band.
Now fasten the movement holder in the mounting of the
cleaning machine again (
Fig. 6.3.1.A
)
.
Ensure that the movement holder is correctly locked in the
locking mechanism (
Fig. 6.3.1.B
).
Ensure that the holder is correctly screwed to the drive shafts
(
Fig. 6.2.1.D
).
C
D
Loading retaining
clips
ATTENTION
Fastening movement
holder in the
mounting
C
E