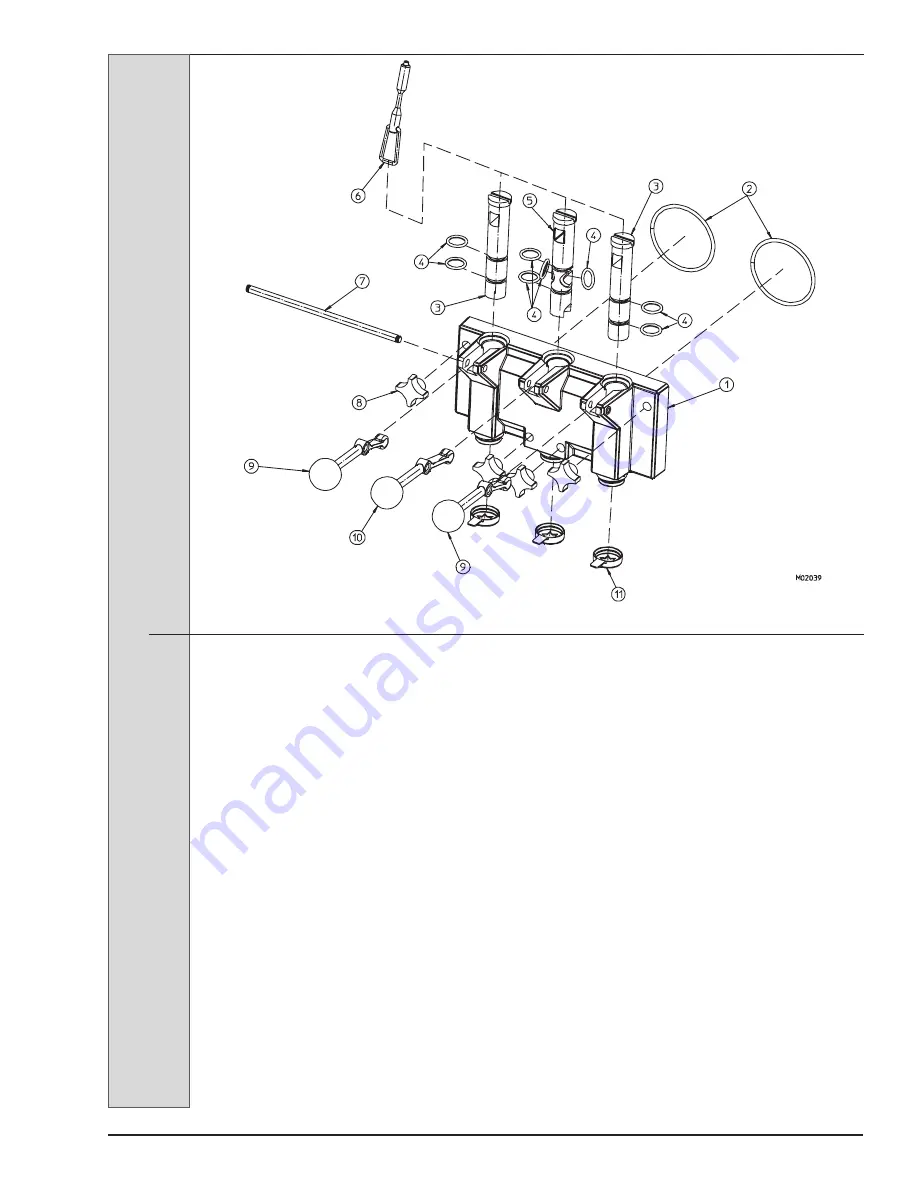
ELECTRO FREEZE Soft Serve Models SLX400C
184582-01
1
Figure 1 Head Assembly
Item
Part No.
Description
* ...............HC121186 ......... Head - Assy. Dispense ADA
1 ...............HC121260 ......... Head - Assy. with Actuators
2 ...............HC160583 ......... O-ring (Head)
3 ...............HC137174 ......... Plunger - Side Self Dispense
4 ...............HC160501 ......... O-ring (Plunger)
5 ...............HC138009 ......... Plunger - Dispense Center
6 ...............HC113426 ......... Push Rod - Assy. Plunger Switch
7 ...............HC141311 ......... Pin - Handle
7A.............HC160581 ......... O-ring (not shown)
8 ...............HC162625 ......... Knob - Hand
9 ...............HC120864 ......... Handle - Assy Dispense ADA (Side)
HC162629 ....... Knob - Ball 3/8-16 THD Black
10 .............HC120865 ......... Handle - Assy Dispense Center ADA
HC162629 ....... Knob - Ball 3/8-16 THD Black
11 .............HC196192 ......... Nozzle - Serrated Six Point
* Includes all items above except #6 and #8.
Not Shown:
HC114341-05 .... Stud - Assy. Cylinder 3-5/16” (Bottom)
HC114341-08 .... Stud - Assy. Cylinder 2-5/16” (Top)
HC116410 ......... Switch - Dispense Head Kit
Содержание SLX400C
Страница 2: ......
Страница 10: ......
Страница 58: ......
Страница 60: ......
Страница 62: ......
Страница 70: ...8 184582 01 ELECTRO FREEZE Soft Serve Models SLX400C Figure 8 Assembly View ...
Страница 73: ...ELECTRO FREEZE Soft Serve Models SLX400C 184582 01 11 O Ring Chart ...
Страница 74: ...12 184582 01 ELECTRO FREEZE Soft Serve Models SLX400C ...