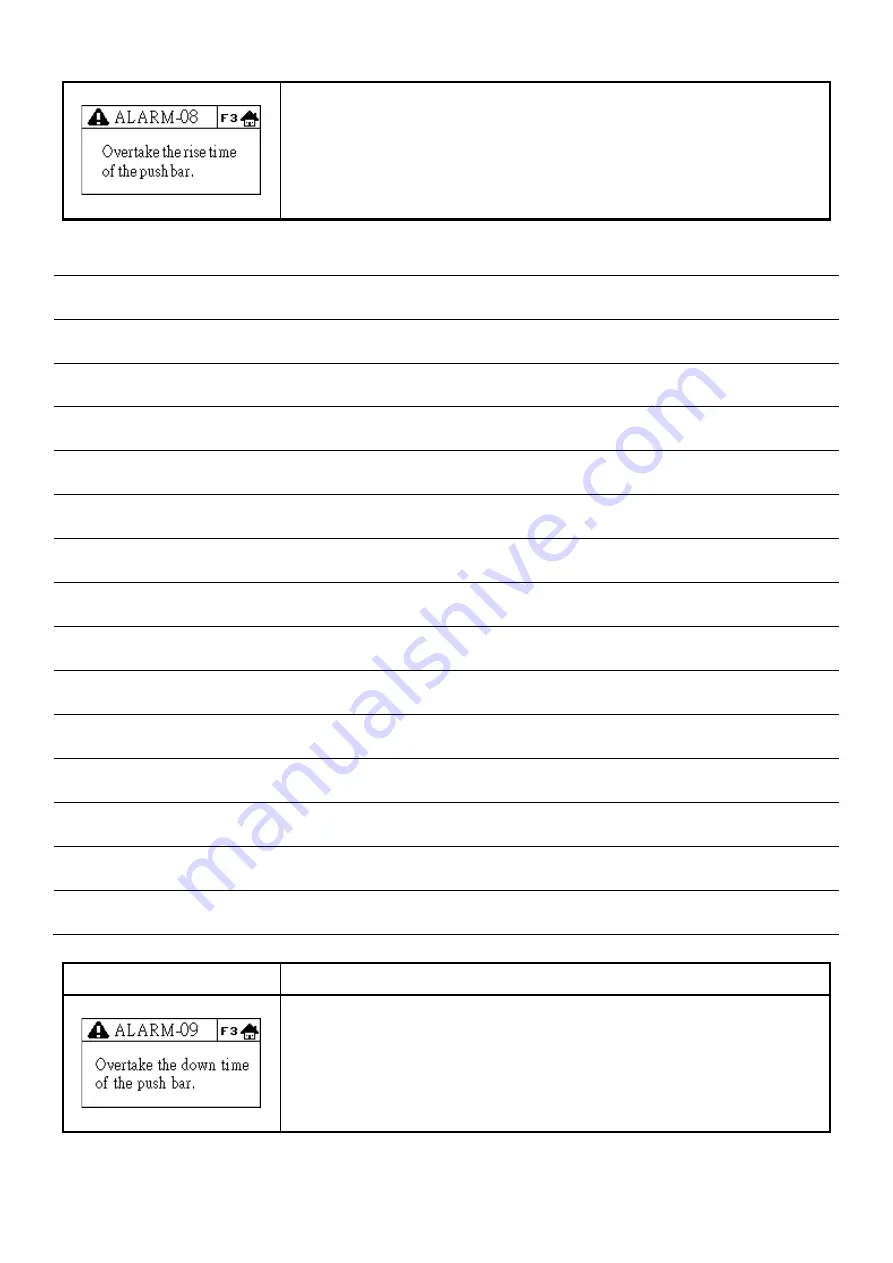
91
Scout 320 REV 3:2018
※
Check for low air pressure supply.
※
Check for correct sensor placement.
※
Check for obstruction limiting movement.
※
Check
LS08 Channel Open Switch
for loose or damaged
wiring.
Alarm Number
CURE
※
Check for low air pressure.
※
Check for correct sensor placement.
※
Check for obstruction limiting movement.
※
Check
LS07 channel close switch
for loose or damaged
wiring.