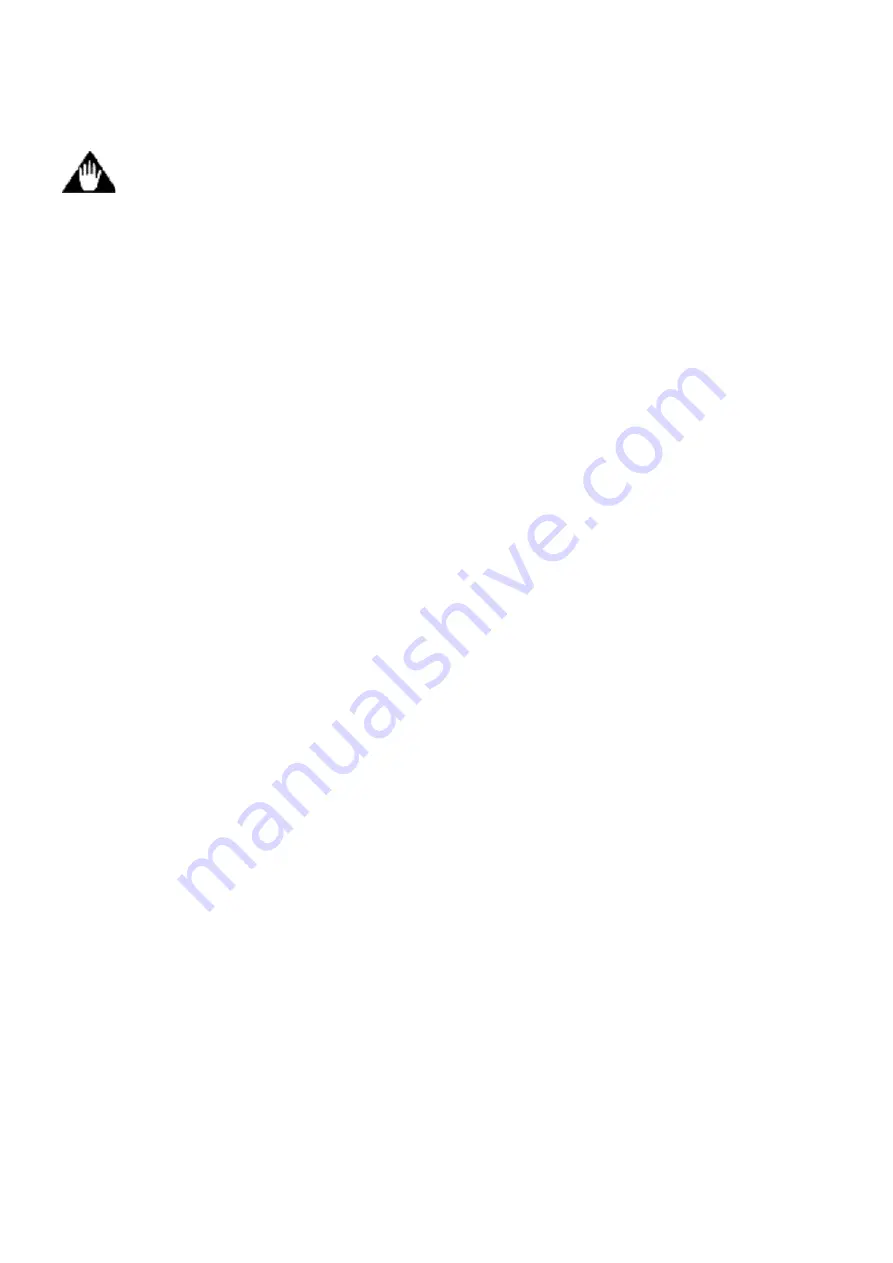
42
Scout 320 REV 3:2018
5.8 Material Standards and Requirements
Caution The ends of the bar should be relatively straight to the
diameter of the bar to help ensure proper positioning of the bar as it reaches
the facing position and to keep the bar pusher from sliding off the bar while
feeding the material. In most cases chamfering the lathe side of the bar is
required and with spindle rotation at approximately 50rpms.
Material should be relatively straight and clean. A chamfer on the leading bar edge is highly
recommended. While bent stock will not necessarily cause problems within the lathe spindle
while turning, it may prevent loading if bar condition is such that the bar collides with the back of
the lathe spindle or it binds while feeding into the spindle. Bars of small diameter may not pick
up properly from the magazine if they are not straight. Excessive chips, burrs or dirt may cause
binding within the spindle.
Straightness Requirements
Optimum performance of the bar feeder can only be achieved if the material to be run meets
specifications for straightness. The maximum allowable bend in a bar is 0.5mm T.I.R. in a 1
meter section (.02” T.I.R per 3 foot section). This tolerance assumes a curvature over the
length of the section and not a short kink in the bar. This tolerance is not accumulative. The
tolerance for the entire length of the bar is 1.7mm TIR.