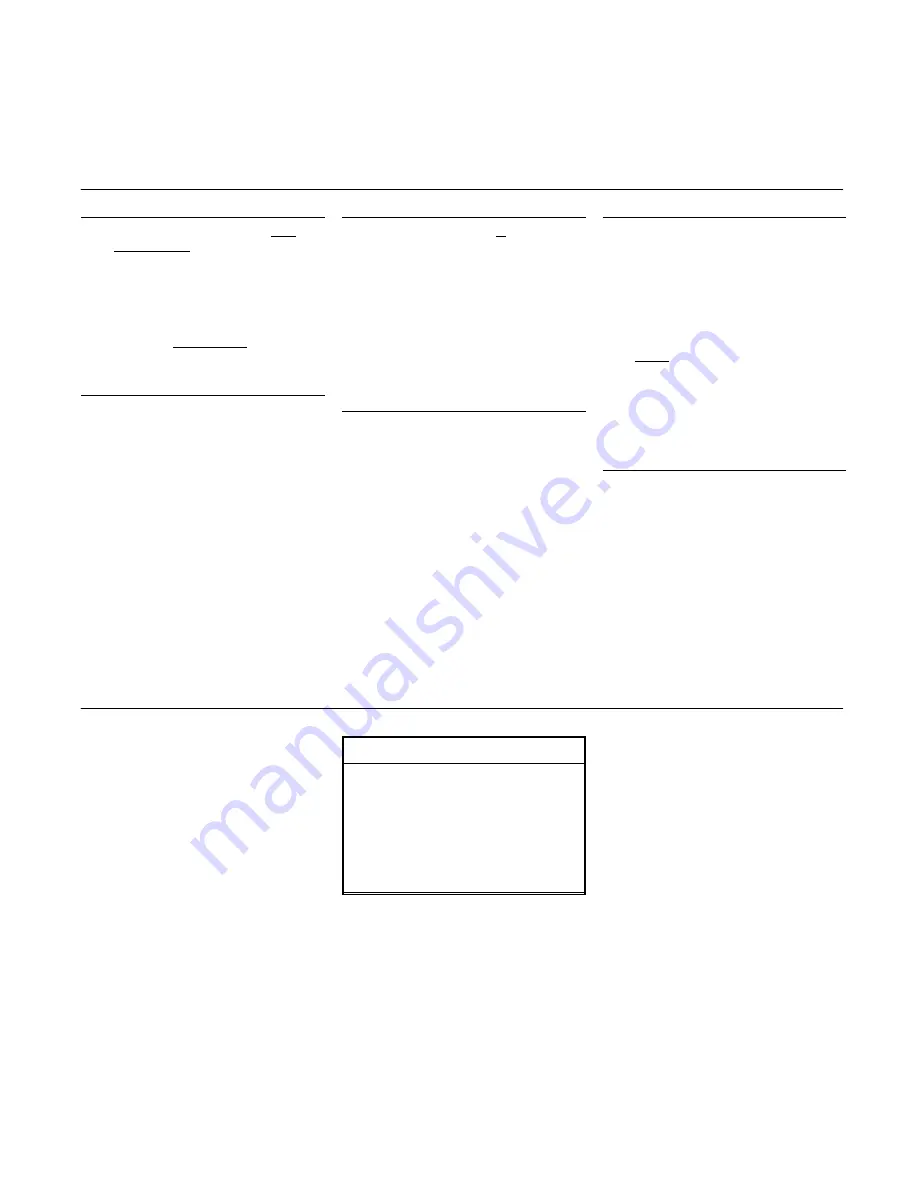
28
3.
Press Move–F3 key. The axis
should move to the position
entered above.
If the axis motion is unstable or
exact position is not reached or
motion is sluggish, it may be
because the proportional or other
gains are not optimum. Refer to
Troubleshooting section (page
##) for tuning and troubleshooting
help.
4.
If homing sequence is
implemented, perform the
following check:
Go to Run mode main screen and
select ‘Home’. Press Home–F4
key. Axis should move to the
home limit switch, stop, move to
offset position and just off the
switch and stop. The axis
position should now be the
programmed Home Position
(usually 0.000)
5.
If Limit+ and/or Limit– functions
are used, perform the following
check:
Go to Jog screen and move axis
towards one of the limits. When a
limit switch is reached, the axis
should decelerate to zero velocity
(stop). Continued pressing of the
same Jog key should not cause
any motion. Press the other Jog
key. The axis should move
towards the opposite limit
switches. Keep jogging in this
direction until the limit switch is
reached. Again, the axis should
stop.
Table 3-4. Operational Test
Programming
Introduction
Efficient programming requires that
several steps be performed in
sequence. These are:
1. Determine overall motion limits on
each axis –– the axis configuration
limits. These will be entered for each
axis from the Configuration (CFG)
mode. The controller will use these
limits as defaults at other
programming levels.
These configuration parameters
should be carefully verified. Jog
each axis between the extreme axis
position limits, or the maximum
positions that will ever be
programmed. Test Maximum
Velocity, Acceleration, and
Deceleration rates, using Position
screen. (Ref: Operation Test
section, page ##.)
WARNING
Motion profile programming should
proceed only after these tests are
completed and test results or values
lower than test results are entered in
the CFG mode for each axis. See
Initial Set-Up section (page ##) for an
explanation of the Terminal screens
used for entry.
2. Determine what axis profile(s) are
to be programmed. Choose a
program number for each. Program
numbers can range from 1 to 999
and don’t have to be sequential.
3. Determine what the limit values for
the motion parameters should be
for each profile. If these are the
same as the configuration axis limits,
they do not have to be entered.
However, it is likely that if several
profiles are programmed, some
should have reduced limit values.
These individual program limit values
default to the axis configuration
values. In turn, the motion
parameters in each segment have
the program values as defaults.
4. Enter the program limits for the
first profile to be programmed.
These are entered from the Program
mode (PRG) – described in this
chapter.