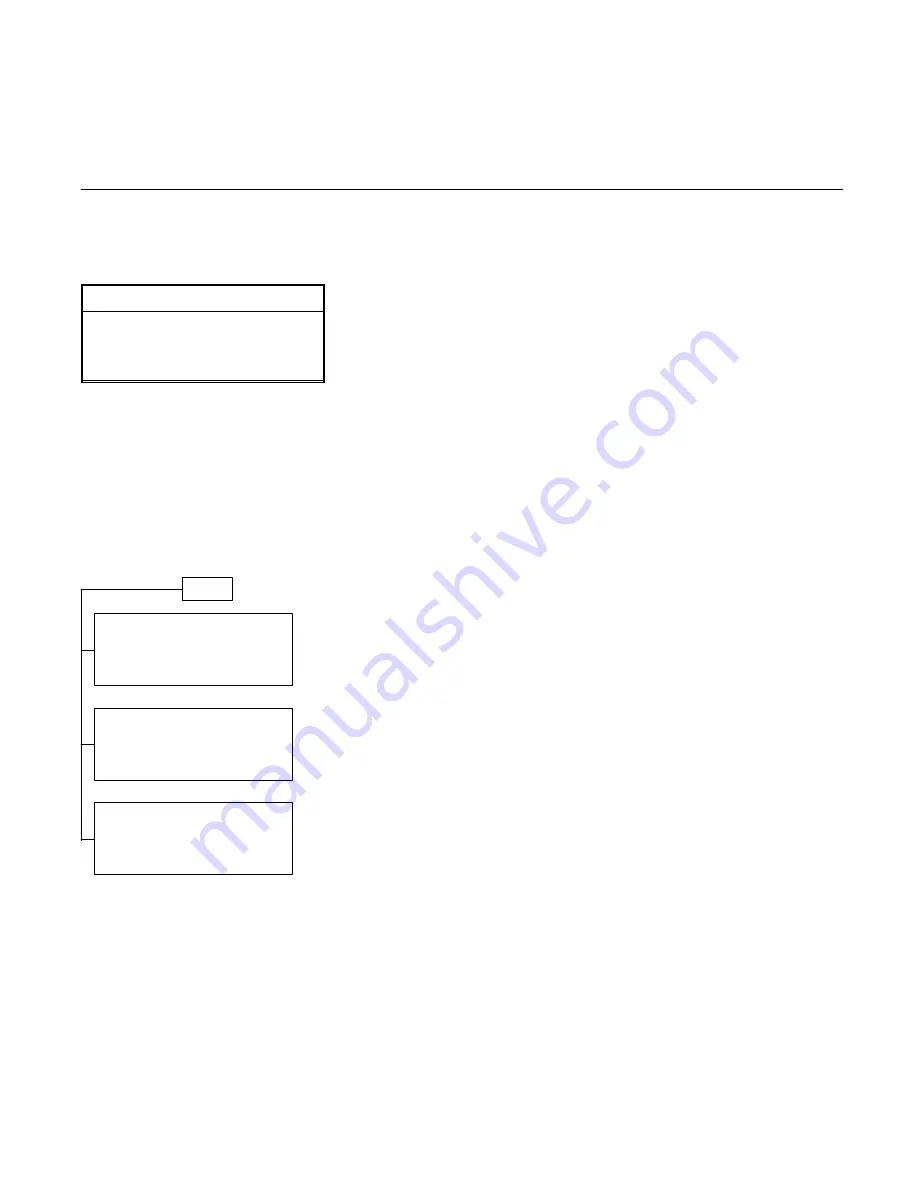
16
Set–Up Axis Configurations
Perform the installation and check-list in
the Installation section (page ##).
CAUTION
At this point, power should still be
removed from electric or hydraulic
axis actuators to prevent unintended
motion or damage.
Apply power to the controller. Get into
Monitor (MON) mode as indicated on
page ##. You can change to different
modes by pressing the corresponding
key. MON, CFG, VAR, PRG, RUN.
Monitor Mode
The Monitor mode (MON) is used to
monitor motion parameters and input
and output status. Three screens are
available:
Figure 3-3. MON Mode Screens
MON
MONITOR MOTION
↑
AXIS
F1
POS 1 0 0000 <SEL
F2
PER 1 0 0000 <SEL
F3
VEL 1 0 0000
↓
<SEL
F4
MONITOR I/O
↑
F1
PREV
F2
ADDRESS: [ 0 ]
<EDT
F3
(NO ALARMS)
↓
NEXT
F4
AXIS[ 1] ALARMS
↑
AXIS
F1
FLAGS(00000000)
F2
←
F3
(NO ALARMS)
↓ →
F4
The first screen allows you to monitor
Axis Position, Position Error, and
Velocity Command for each axis. The
available parameters for viewing are:
Axis 1
POS1 –
actual position
PER1 –
position error
VEL1 –
velocity command
Axis 2
POS2 –
actual position
PER2 –
position error
VEL2 –
velocity command
Note: See pages ##–## for information
about other parameters displayed in
monitor mode.
Any of the above parameters can be
displayed in any of the three fields – F2,
F3, F4 by pushing the corresponding
<SEL (F2, F3, F4). For example, if the
Axis 1 screen is currently displayed
(POS1, PER1, VEL1), push <SEL–F3
once and the following screen will be
displayed. Pushing AXIS-F1 will reset
the screen to all Axis 1, or all Axis 2
parameters.
MONITOR MOTION
↑
AXIS
F1
POS 1 X XXXX <SEL
F2
POS 2 X XXXX <SEL
F3
VEL 1 X XXXX
↓
<SEL
F4
Pushing F1 again will show the following
screen:
MONITOR MOTION
↑
AXIS
F1
POS 2 X XXXX <SEL
F2
PER 2 X XXXX <SEL
F3
VEL 2 X XXXX
↓
<SEL
F4
The second screen (reached by
Up/Down arrow keys) is used to monitor
Alarms (Error Flags). See General
Faults section (page ##).
AXIS[ 1] ALARMS
↑
AXIS
F1
FLAGS(00000000)
F2
F3
(NO ALARMS)
↓
NEXT
F4
The Monitor I/O screen (reached by
Up/Down arrow keys) is used to monitor
I/O status.
MONITOR I/O
↑
F1
PREV
F2
ADDRESS: [ 0 ]
<EDT
F3
STATE: (0)
↓
NEXT
F4
CFG-System Parameters section (page
##) describes input and output address
assignment. You can monitor the state
(ON = 1, OFF = 0) of any address by
scCFG-rolling through the addresses
with the PREV–F2 or NEXT–F4 keys. A
specific address can be accessed
directly by pressing <EDT–F3 and then
entering in the address number, then
press ENTER.
A description of parameters is available
for viewing on the Monitor screen. In
addition to Position, Velocity and Error
Parameters, the following are available
by scrolling (left–right) each line:
Axis 1 or Axis 2
A/D
– Output in analog-to-
digital counts. Used for
diagnostic purposes.
D/A
– Analog input in counts.
BRC
– Number times following
error exceeded
maximum value.
RAW
– Feedback counts – for
absolute encoders such
as resolvers.
P (X) Seg ( ) – Displays program
number and segment
number currently being
executed.
Configuration Mode
Press CFG to bring up the Axis
Configuration mode. [Note: If the unit
has previously been programmed with a
security code other than 0, you will have
to know the security code to proceed
further than Monitor mode.] Press
Up/Down arrow keys to change from
one screen to the next.
Configuration mode is required to set
each axis parameters:
–
Axis Gains
–
Position Sensor Scale Factor
(counts per engineering unit)
–
Software Travel Limits
–
Home Parameters
–
Maximum Acceleration,
Deceleration, Move Velocity and
other motion parameters
–
Input/Output Requirement