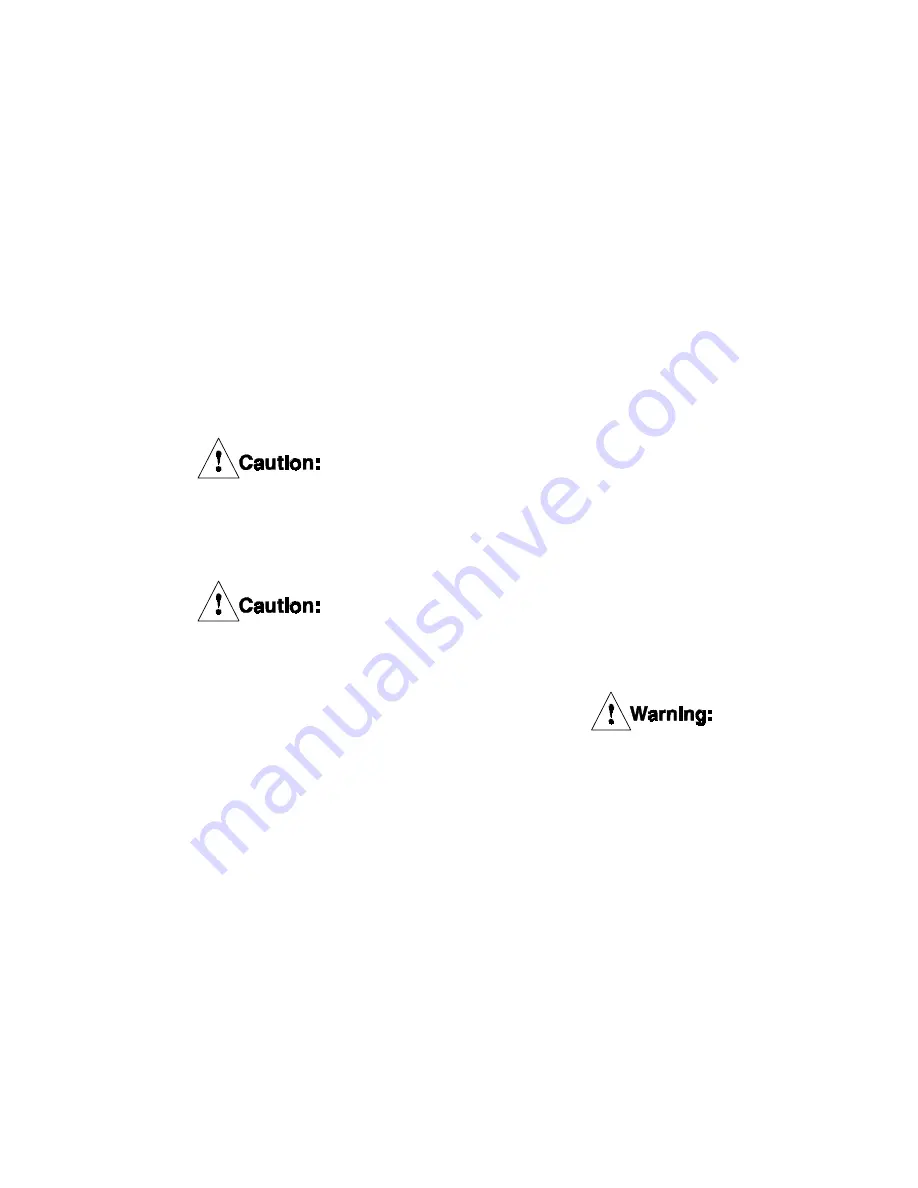
4.2.3
Disconnect the air supply lines from the
brake.
4.2.4
Rig the cylinder assembly. Slide the
cylinder (19), spring housing (16) and
pressure plate (13) (powerpak) off of the
studs as an assembly. Set aside in a clean
area making sure not to damage the
friction material wear surface on the
pressure plate.
Note: If a stud (6) should happen to come
loose, remove it completely, clean the
threads on the stud and the threads in the
mounting flange. Apply Loctite
®
Primer
Grade "T" to the stud threads. After the
threads have dried, assemble to the mount-
ing flange using Loctite
®
#262. The end of
the stud must not extend past the mounting
surface on the mounting flange.
Loctite® #262 must be shaken prior
to application.
Loctite® #262 may irritate sensitive
skin. Refer to the product label for
proper safety precautions.
4.2.5
Remove the friction disc assemblies, the
reaction plates (30) and the release springs
(34) and set aside.
4.2.6
Slide the clamp tubes (12) and wear
spacers (29) off of the studs.
4.2.7
Inspect the friction disc for wear. Refer to
Table 4 for wear limits. Repair per section
4.3.
4.2.8
Inspect the friction wear surfaces on the
mounting flange and reaction plate surfaces.
if the limits in Table 4 are reached or
exceeded replacement is required.
4.2.9
Inspect the pressure plate wear surface. If
the wear reaches or exceeds then limit in
Table 4 replacement is required. Refer to
section 4.5 for further dis-assembly
procedures.
4.2.10
See section 4.4 for cylinder seal
replacement.
4.2.11
Inspect the clamp tubes, springs (22) and
release springs (34) and compare to the
limits in Table 4. If any limit is reached,
replacement is required.
4.2.12
Refer to section 4.5 if spring (22) (34)
replacement is required.
4.2.13
Re-assemble the brake per section 4.7.
4.3
Friction Material Replacement
4.3.1
Disconnect the air supply lines and remove
the cylinder/spring housing/pressure plate
assembly (power pac) per 4.2.2 -4.2.4..
4.3.2
Remove the friction disc assembly,
reaction plate, seperator springs and
remaining friction disc assembly and
transport to a clean work area.
4.3.3
Remove the screws and washers attaching
the friction disc subassembly to the ring gear
and remove the friction disc subassembly.
4.3.4
Thoroughly clean the threaded holes in the
ring gear and the threads on the screws.
4.3.5
Attach a new friction disc subassembly to
the ring gear using Loctite
®
#262 on the
screw threads. Torque the screws to the
value shown on Table 3.
Use only the proper size and grade
screws to attach the friction disc
sub-assembly to the ring gear. Use
of commercial (Grade 2) screws
where Grade 8 screws are specified
may result in failure of the screws
and a sudden loss of brake torque.
4.3.6
Friction disc cores may be relined with
new friction material per the following
instructions. Refer to Table 5 for the
appropriate friction disc replacement kit
part number.
DBB 8104 PDF format
8
© Copyright Eaton Corp., 1998. All rights reserved.
(Revised: January, 1998)