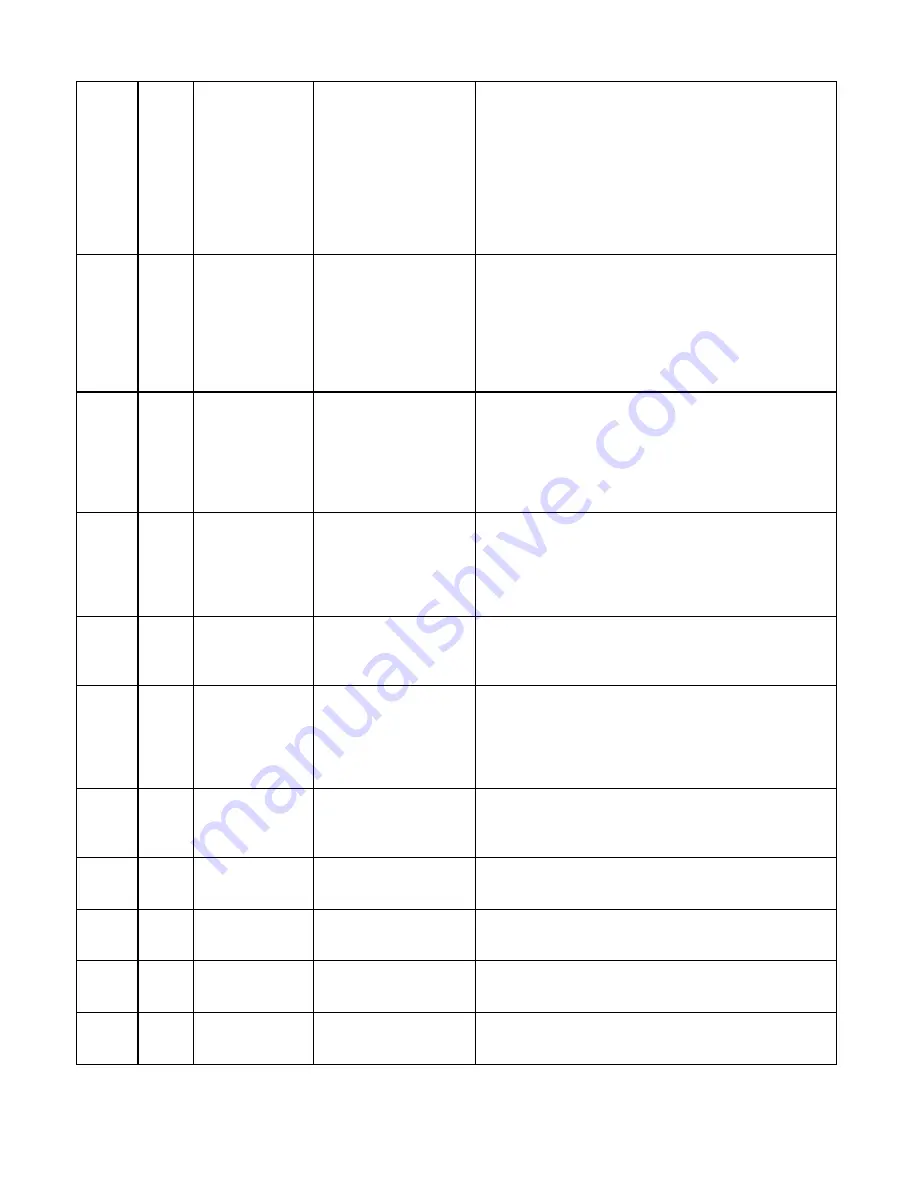
7382
29570
Resolver output level
too low
Reaction 5: Switch-off of the
current immediately (without
ramp), application of the
brake
Malfunction (motion caused by external source) of the motor
during automatic commutation, starting current too great, incorrect
parameter for commutation direction (use MotorManager to
determine the values). Check feedback resolution (per pitch) and/or
number of feedback or motor poles. A motor phase has been
(temporarily) interrupted.
Post-pulse oscillation of the drive due to a too high excitation in a
feebly attenuated system ->= increase O2190.1
AutoCommuntationControl_Ramptime and/or vary O2190.4
AutoCommutationControl MotionReduction.
7383
29571
Synchronization of
resolver excitation
Reaction 5: Switch-off of the
current immediately (without
ramp), application of the
brake
Eliminate external influence on the motor or device current is too
small resp. friction is too high.
Post-pulse oscillation of the drive due to a too high excitation in a
feebly attenuated system ->= increase O2190.1
AutoCommuntationControl_Ramptime and/or vary O2190.4
AutoCommutationControl_MotionReduction.
The commutation direction may be badly parameterized (use
MotorManager to determine the values).
7385
29573
Position difference
between load
mounted and motor
feedback too high
Reaction 2: Downramp /
apply brake / de-energize..
Avoid external influences on the motor, check feedback (sufficient
EMC immunity/shielding, resolution not configured). In very easy
running systems, it may be necessary to increase O2190.1
AutoCommutationControl_Ramptime. If needs be, increase O2190.7
AutoCommutationControl_Standstillthreshold as well.
7390
29584
SinCos internal
feedback error (group
bit)
Reaction 2: Downramp /
apply brake / de-energize..
Increase starting current O2190.2 and eliminate very high direction
dependence or friction if any. Check feedback resolution and/or
number of feedback or motor poles. With a high inertia (or
mass)/torque constant KT ratio, it might in addition be necessary to
reduce the motion threshold O2190.3.
7391
29585
Feedback level
exceeds limit
Reaction 5: Switch-off of the
current immediately (without
ramp), application of the
brake
Increase the starting current or eliminate external influence on the
motor. Check feedback resolution and/or number of feedback or
motor poles, update firmware to a release higher than 04_2005-3
(Firmware V02.07.16).
7392
29586
Feedback level too
low
Reaction 5: Switch-off of the
current immediately (without
ramp), application of the
brake
Increase automatic commutation starting current, eliminate motor
block, check parameters for motor current (too small, device
extremely under-dimensioned), current controller unstable. With a
high inertia (or mass)/torque constant KT ratio, it might in addition
be necessary to reduce the motion threshold O2190.3.
7393
29587
SinCos RS-485
communication error
(multiple bit)
Reaction 2: Downramp /
apply brake / de-energize..
Connect motor resp. check wiring. In the case of high winding
resistance reduce peak current so that Rkk*Imax is inferior to
Umains*0.8.
The power stage may be defective.
7394
29588
Feedback EEPROM
data invalid
Reaction 2: Downramp /
apply brake / de-energize..
Check and correct feedback sensor adjustment as well as feedback
wiring.
7395
29589
Error while storing
data in feedback
EEPROM
Reaction 2: Downramp /
apply brake / de-energize..
Increase baud rate
7396
29590
Checksum error
SinCos® EEPROM
Reaction 2: Downramp /
apply brake / de-energize..
Check feedback and feedback cable.
7397
29591
SinCos® FF feedback
type is not supported
Reaction 2: Downramp /
apply brake / de-energize..
Check feedback and feedback cable or reduce lower limit value
(Obj287.10) if needs be