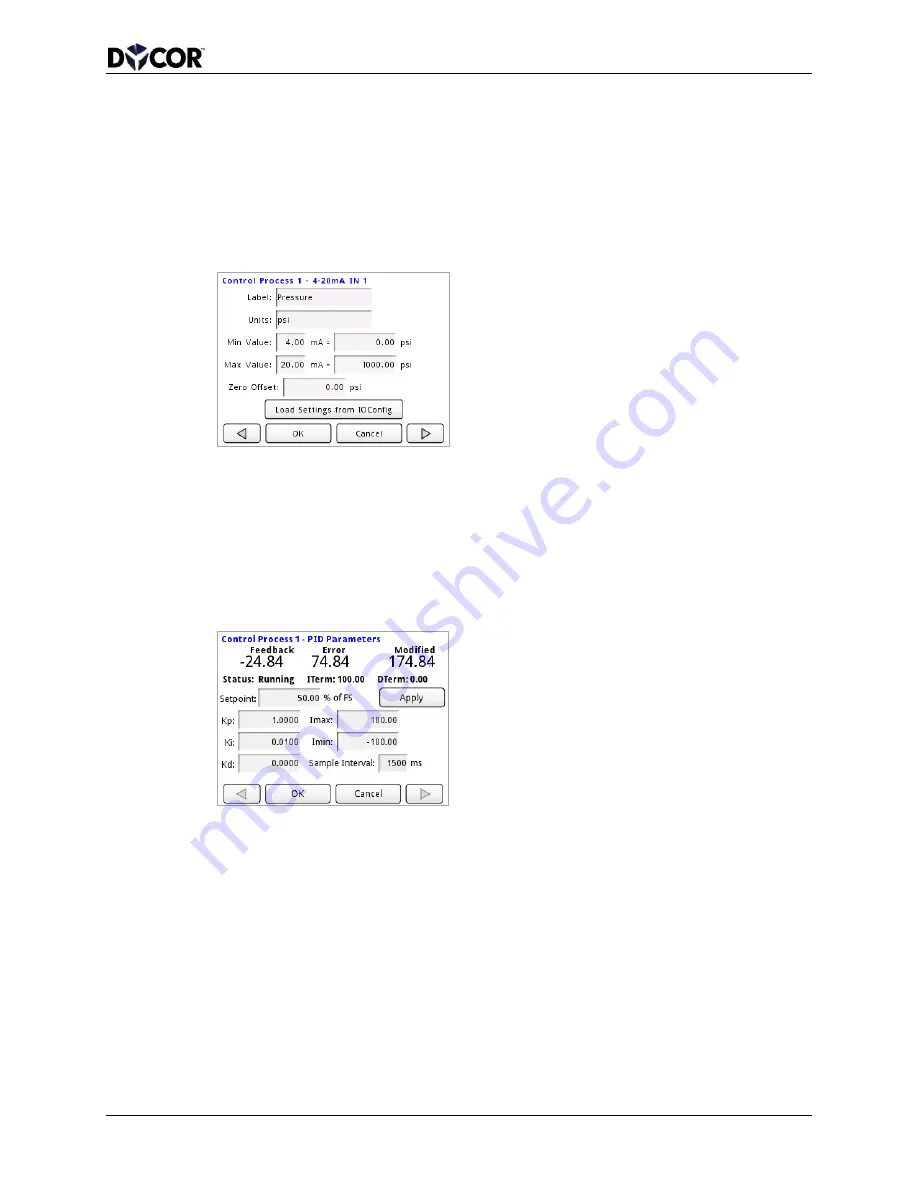
SmartVue Operator’s Manual
10-0004-R13
25
3.
Press the right arrow button to proceed to the feedback input scale configuration.
4.
Feedback label, units, scale – If you have pre-configured IO units and scales
values that you want to use for the selected input type, press the
Load Settings
from IOConfig button to load them. Enter a label and engineering units that will
appear on the Meter Screen then enter scaling values for the input signal so that
the displayed values accurately reflect the value being measured for the
engineering units you have chosen.
Note that input scaling values will not be applied to the control process
computation algorithm until either
Apply (see below) or OK are pressed.
5.
If the control mode is
PID Ext SP, the next screen will be the setpoint scale
configuration which is configured as described in the previous step. Proceed to
the next screen.
6.
PID Parameters: Enter values for the Setpoint (PID mode only), the PID
coefficients,
Kp, Ki, and Kd, as well as Imax, Imin, and the Sample Interval.
Kp, Ki, and Kd are the PID algorithm coefficients or gains. Imax and Imin set
limits for the I term, preventing it from becoming too large and are specified in
engineering units for the process output. The values you choose depend on the
capability of the system being controlled.
The valid range for the
Sample Interval is 20 to 10000 milliseconds. A slower
system that is less sensitive to random disturbances or parameter variations does
not need to be sampled as often. If using a Modbus register as the Feedback then
it is suggested to have the sample interval higher than the register update rate.
You can observe the effects of adjusting the PID parameters on the Feedback,
Error, and Modified values on this screen and thus
tune the control process by
using the
Apply button.
Adjust the PID parameters and click Apply
or OK to update the control process. You
can tune your control process by using the
Apply button and observing the effects on
the Feedback, Error, and Modified values.