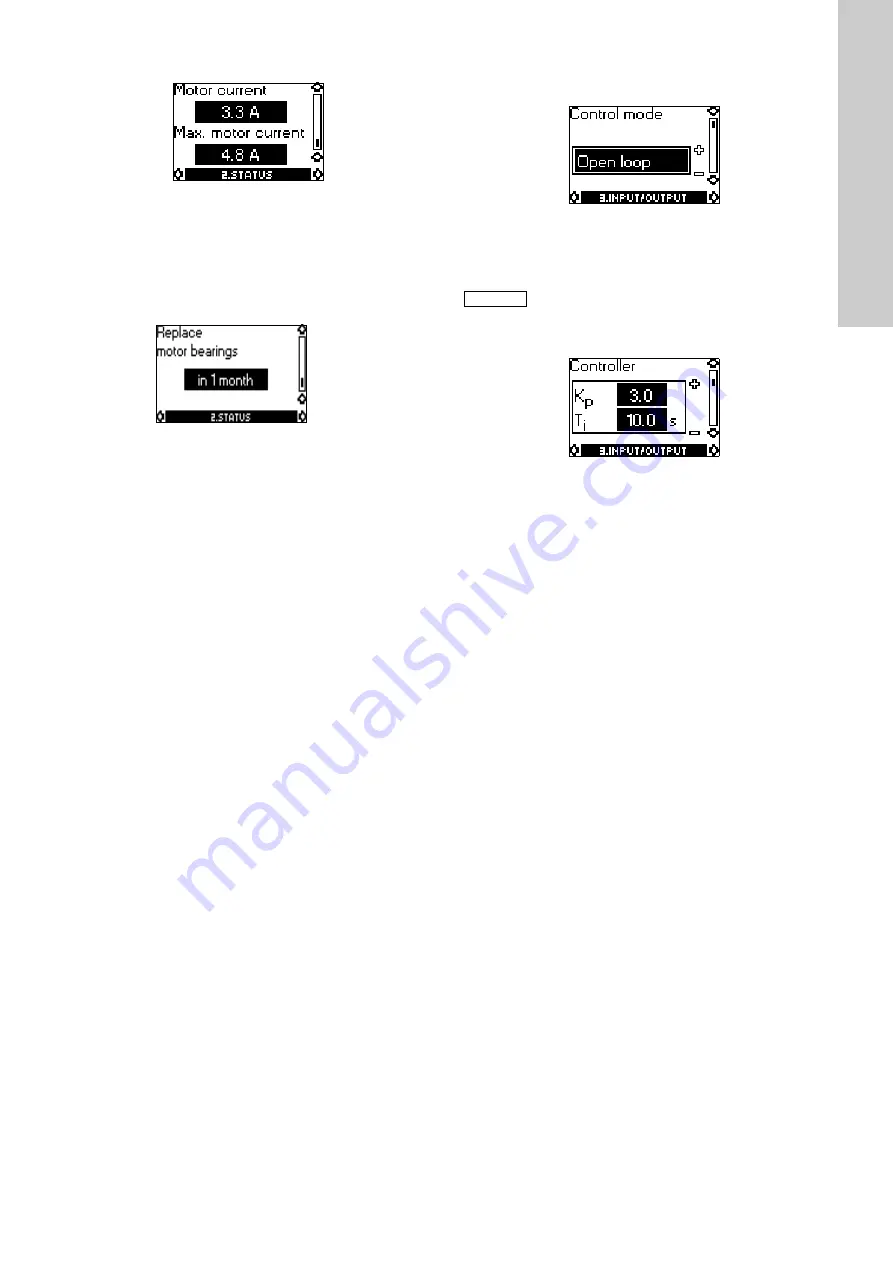
English (GB)
13
10.2.7 Display of motor current
Tolerance: ± 5 %
•
Motor current
indicates the actual motor input current from
the frequency converter.
•
Max. motor current
indicates the maximum motor current
limit.
10.2.8 Time till replacement of motor bearings
(only three-phase motors)
This display shows when to replace the motor bearings.
The controller monitors the operating pattern of the pump and
calculates the period between bearing replacements.
The displayable values are these:
• in 2 years
• in 1 year
• in 6 months
• in 3 months
• in 1 month
• in 1 week
• Now!
10.3 Menu INPUT/OUTPUT
10.3.1 Selection of control mode
Select one of the following control modes:
•
Closed loop
,
•
Open loop
.
10.3.2 Setting of controller
In this display, the gain (K
p
) and the integral-action time (T
i
) of the
built-in PI controller can be set if the factory setting is not the
optimum setting:
• The gain (K
p
) is set within the range from
0.1
to
20
.
• The integral-action time (T
i
) is set within the range from
0.1
to
3600 s
.
If
3600 s
is selected, the controller will function as a P
controller.
Setting the PI controller:
1. Start the motor and adjust the system so that the motor is
operating in the typical operating situation.
2. Set the integral-action time (T
i
) to 3600 s.
3. Increase the gain (K
p
) until the motor operation gets unstable,
i.e. until the actual value starts fluctuating, see section
10.2.3 Display of actual value
. Instability can also be heard
because the motor starts adjusting the speed up and down.
Some systems react slowly, e.g. during temperature control.
Therefore, several minutes may pass before the motor
operation gets unstable.
4. Set the gain (K
p
) to half the value at which the motor got
unstable. Then the gain has been set.
5. Reduce the integral-action time (T
i
) until the motor gets
unstable.
6. Set the integral-action time (T
i
) to the double value of the
value at which the motor got unstable. The PI controller has
now been set.
Inverse control:
It is possible to set the controller to inverse control (if the setpoint
is increased, the speed will be reduced). In the case of inverse
control, the gain (K
p
) must be set within the range from
-0.1
to
-20
.
Note
If the motor is connected to a bus (see section
), it is not possible to select the
control mode via the R100.
Содержание VT Booster Set
Страница 1: ...VT Booster Set O M Manual...
Страница 3: ...1 Important Health Safety Information Page 3 VT Booster Set...
Страница 10: ...2 System Information Installation and Commissioning Page 10 VT Booster Set...
Страница 11: ...2 1 Booster Set Components VT Booster Set Components Page 11 VT Booster Set...
Страница 12: ...2 2 Control Panel Wiring Diagrams Twin Pump Wiring Diagram Single Phase Page 12 VT Booster Set...
Страница 13: ...Twin Pump Wiring Diagram 3 Phase Page 13 VT Booster Set...
Страница 14: ...VT3 Single Phase Control Panel Wiring Diagram VR VASCO Cold Water Booster Sets Page 14 VT Booster Set...
Страница 15: ...VR VASCO Cold Water Booster Sets Page 15 VT Booster Set...
Страница 16: ...VT3 Three Phase Control Panel Wiring Diagram Page 16 VT Booster Set...
Страница 17: ...Page 16a VT Booster Set...
Страница 23: ...3 User Maintenance and Troubleshooting Page 22 VT Booster Set...
Страница 43: ...Appendix 14...
Страница 50: ...Appendix 21...
Страница 51: ...Appendix 22...
Страница 55: ...Appendix 26...
Страница 56: ...Appendix 27...