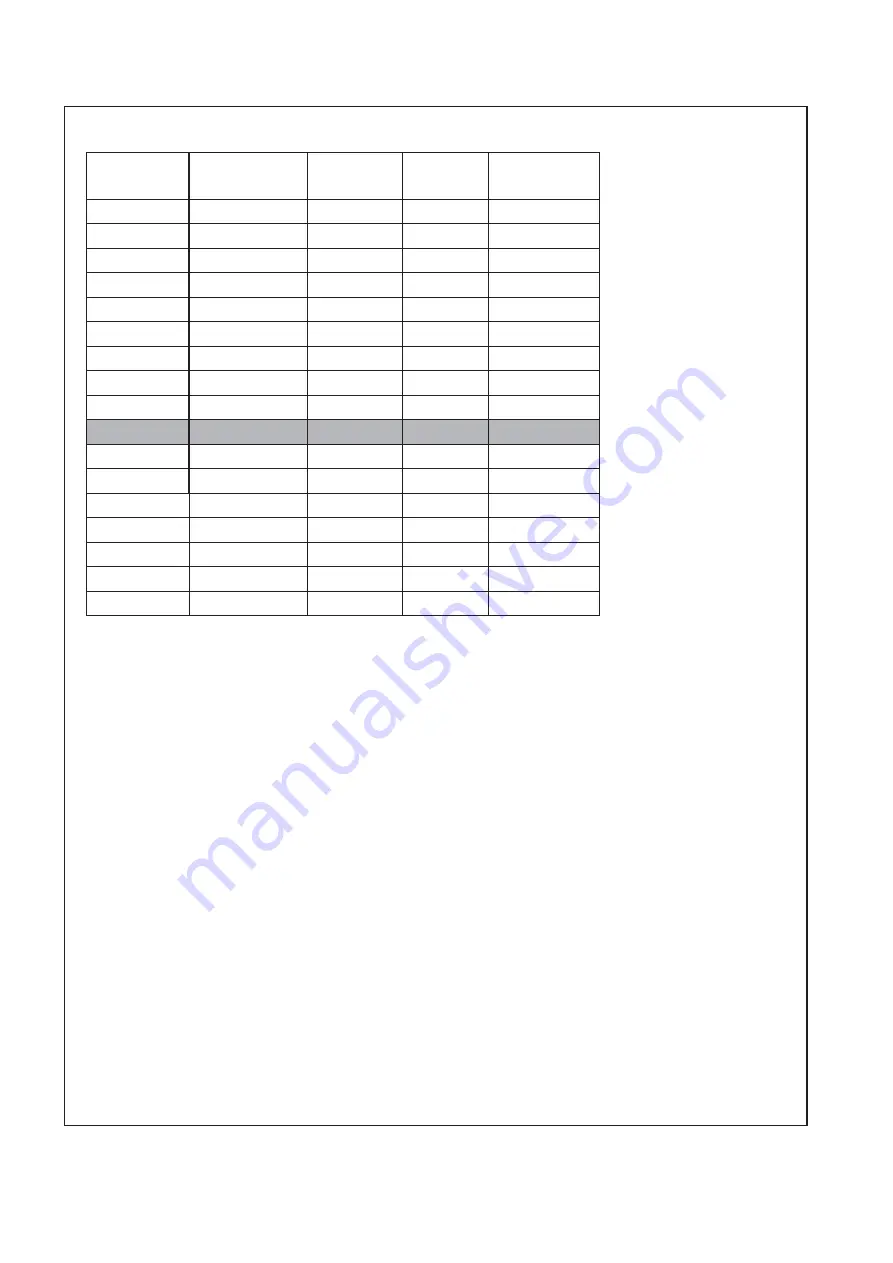
26
‘Renovator Mk4’
Calibration Sowing Chart
Settings for Seed Type
Seed Type
Default Calibration
Factor (kg/rev)
Shutter Slide1 Bottom Flap2
Metering Wheel3
Wheat
0.70
3/4
3
N
Oats
0.69
Full
3
N
Barley
0.69
Full
3
N
Ryecorn
-
Full
3
N
Peas
1.00
3/4
3
N
Grass
0.28
Full
3
N
Grass Mix
0.30
Full
3
N
DAP Granules
0.94
Full
3
N
Super Phosphate
1.20
Full
3
N
Lucerne/Alfalfa
0.10
3/4
1
F
Turnip
0.093
3/4
1
F
Kale
0.092
3/4
1
F
Swede
0.093
3/4
1
F
Canola/Rape
0.09
3/4
1
F
White Clover
0.094
3/4
1
F
Red Clover
0.094
3/4
1
F
NOTES
1. SHUTTER SLIDE
For grain, opening the shutter slide to Full gives 10-15% more flow.
2. BOTTOM FLAP
The values shown were the optimum test settings.
Decreasing the gap may cause seed damage.
Too large a gap will give intermittent flow rates.
Flaps are spring loaded to cope with small variations in seed/granule size.
3. METERING WHEEL
N = Normal metering wheel
F = Fine metering wheel only
TSW:
TSW(gm) x Desired Plants/m
2
= Sowing Rate (Kg/Ha)
Germination %
Содержание MK4 Renovator
Страница 2: ...ii ...
Страница 17: ...15 Pt No 67437 Issue 0716 Renovator Mk4 ...
Страница 29: ...27 Pt No 67437 Issue 0716 Renovator Mk4 Calibration Notes ...
Страница 30: ...28 ...
Страница 34: ......
Страница 36: ...1 ...
Страница 63: ...28 Figure 33 Motor control module offline ...