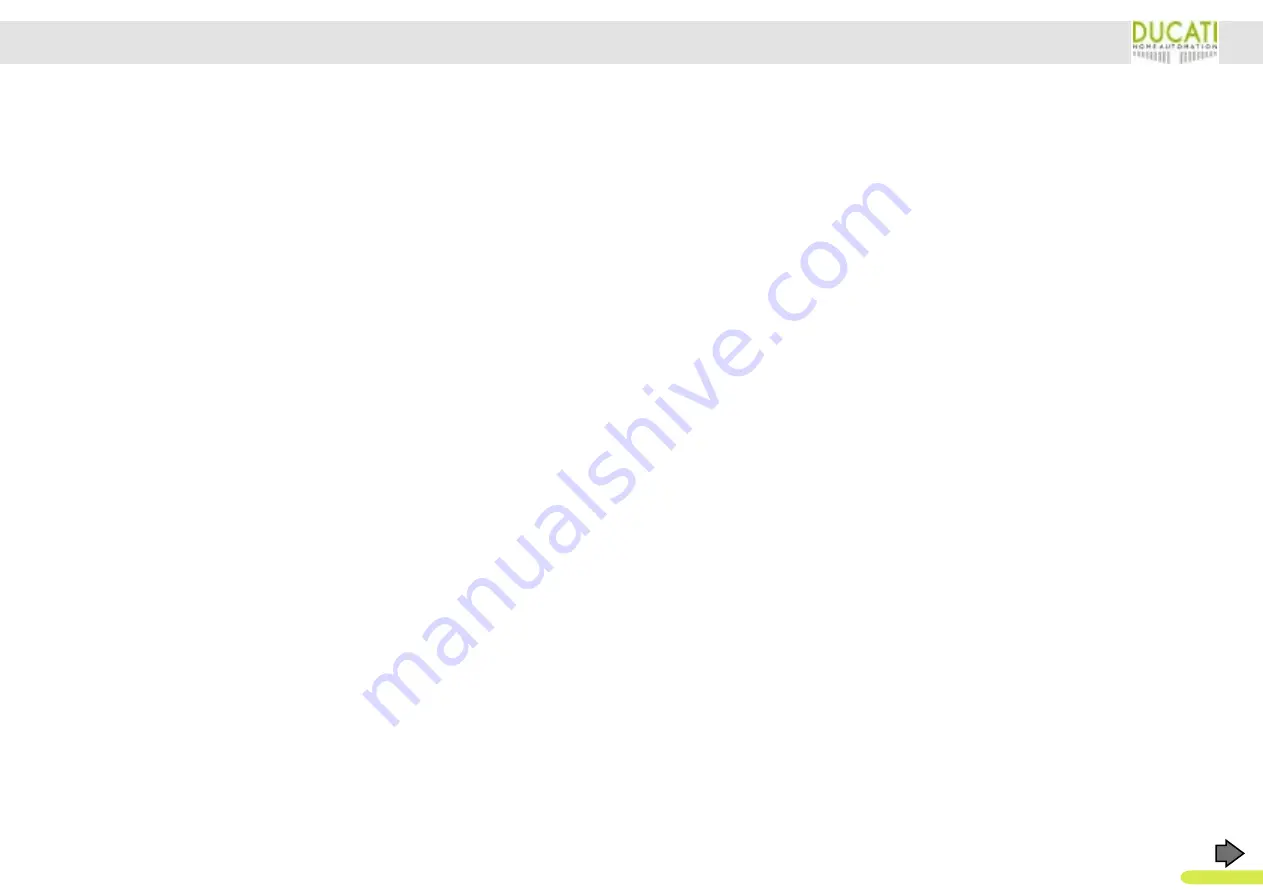
19
6) FIXING FROM THE RACK TO THE GATE
(See the drawings in section 6).
The rack (module 4) can be supplied as standard Ref. RACK 8612 in Hostaform®
(special material in acetal copolymers showing a remarkable combination of wear
resistance, long-term fatigue resistance and hardness) in measuring sections of 0 , 5
m each or, on request, in the traditional iron version (Art. FE8612) in 1 m bars.
Perfect alignment of the frame is of the utmost importance and determines the correct
movement and operation of the drive.
WARNING
: a rack not perfectly aligned with the gate would produce a friction point,
detected by the motorization as an obstacle detected by the safety system which will
cause the motor to stop.
Fastening of the rack model RACK 8612:
Once the motor has been fixed (make sure to respect the correct distance between
the motor and the gate, see drawing 6.4), the frame must be installed one section at a
time (drawing 6.5).
Each segment must be fixed individually to the rack by sliding the gate and checking
that the height of the rack with respect to the motor output pinion is always at the
same distance (drawing 6.2 - 6.3) pag. 7.
WARNING
: respect the tolerance of the dimensions indicated in the drawings in step
6 on page 7.
Proceed as follows:
1) Unlock the motor and manually open the gate up to the mechanical stop.
2) Place the first piece of rack (0.5 m) on the motor output pinion, at the correct di-
stance and height.
3) Mark the top line of the grid and the position of the holes on the gate with a special
pencil.
4) Fasten the first section of the frame to the gate with self-drilling screws.
5) Proceed in the same way with the other sections of the grid until it is fixed along the
entire length of the gate. Take care to position each piece of rack at the same height
so that the distance between the motor output pinion is constant over the entire length
of the gate.
The rack must be fixed to the gate with self-drilling stainless steel screws (not inclu-
ded).
Assemble the rack parts using the male-female recessed bracket using a rubber
mallet.
WARNING:
Once finished, manually move the gate and check that it slides smoothly
along its length without showing any friction points. If not, correct the attachment of
the rack.
6) restart the engine (see section 5).
7-8) PRE-POSITIONING OF LIMIT SWITCH MAGNETS ON THE HINGE.
(section 7 and 8 drawings on page 8).
The position of the magnets along the frame determines the stop point of the gate in
both directions of travel. The limit switch magnets must be fixed on the frame (drawin-
gs section 7) and must be detected by the operator, before the gate reaches the
mechanical stop on the structure.
NOTE:
To avoid an error in the positioning of the magnets, it is recommended, at this
stage of the installation, to pre-position the magnets well before the final mechanical
stop of the gate and subsequently postpone the precise positioning of the magnets.
How to pre-position the limit switch magnet for the gate closed position.
1) Unlock the motor.
2) Manually position the gate 10 cm before the completely closed position.
3) Manually move the limit switch magnet (M) and align it with the "Reed" magnet
detector (R), the position of which is indicated on the motor cover by a label (R).
4) Check that the yellow led on the edge of the electronic board is on to confirm that
the magnet has been detected correctly.
Repeat the operation to position the limit switch magnet for the closed gate position:
5) Unlock the motor.
6) Manually position the gate 10 cm before the gate is completely open.
7) Manually move the limit switch magnet (M) and align it with the "Reed" magnet
detector (R), the position of which is indicated on the motor cover by a label (R).
8) Check that the yellow LED on the edge of the electronic board is on to confirm that
the magnet has been detected correctly.
DUCATI
INSTALLATION