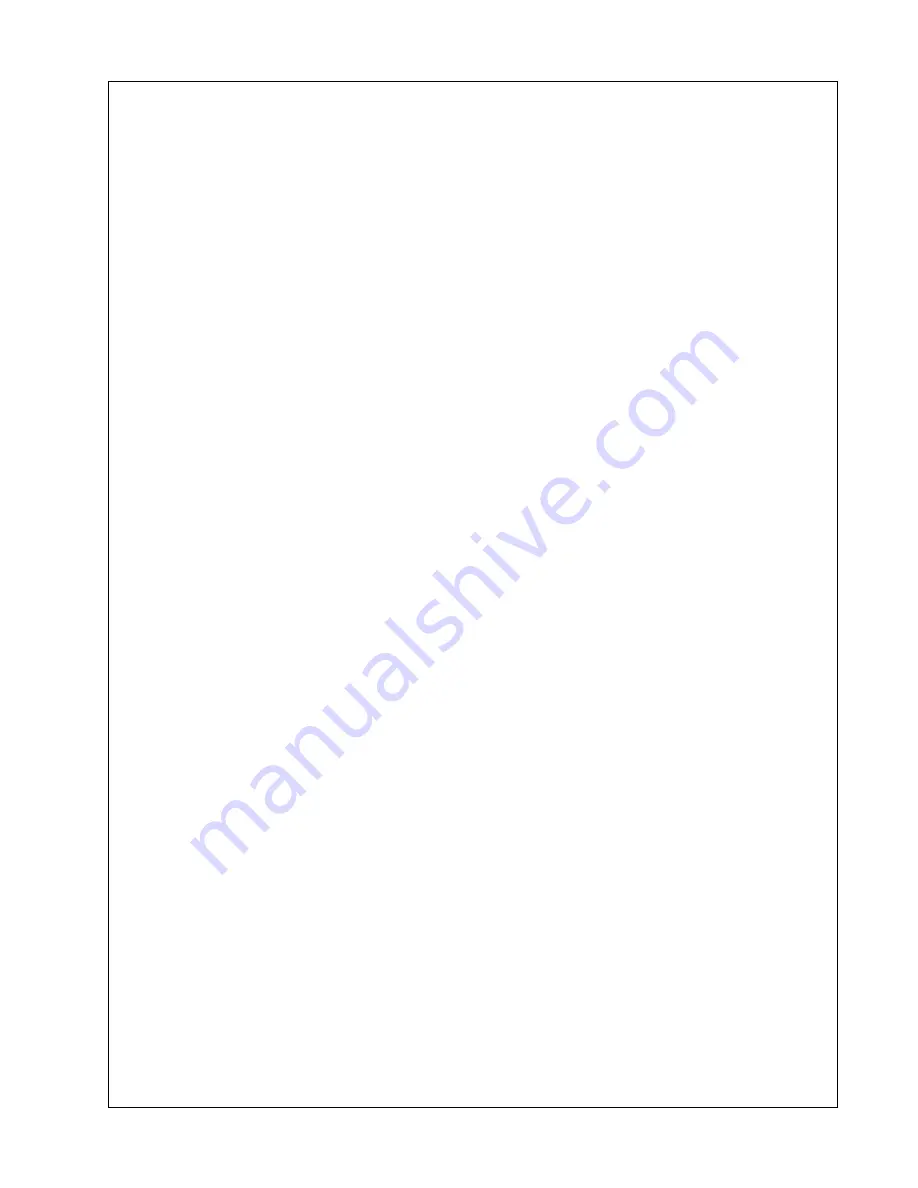
Electrical
Operating & Maintenance Manual
67
Controller Outputs
The INTELLISYS Controller has three different types of outputs: frequency, pulse width
modulated (PWM) and 24 VDC digital (ON / OFF). The frequency output is used as a throttle
signal for the engine (software revisions less than 2.0). The INTELLISYS Controller varies the
frequency from 150 Hz to 375 Hz, corresponding to 1200 to 1800 RPM. The frequency signal
is a 50% duty cycle, 24 VDC, square wave.
The PWM signal is used to control the speed of the aftercooler fan. It is a 125 Hz frequency
signal, 24 VDC with a duty cycle of 5% to 90%.
The INTELLISYS controller provides 24 VDC digital outputs to control solenoids, alarm horn,
strobe lights, DC heaters and fuel pump. These are 24 VDC ON and 0 VDC OFF. They are
current limited and short circuit protected. They may have a voltage level of .5 VDC to 1.4 VDC
in the OFF state due to transistor leakage of the darlington drivers in the controller.
Pressure Control Loop
The INTELLISYS controls discharge pressure by modulating engine speed. The discharge
pressure setpoint is entered at the controller front panel. The control loop will modulate the
engine speed between 1200 and 1800 RPM to maintain the selected discharge pressure.
Electronic Engine
The NHP1500 machine contains an emissions certified diesel engine. In order to meet the
emissions requirements, the engine has an electronic control system.
The control system handles all the monitor, alarm and control functions for the engine. The
INTELLISYS controller communicates with the engine controller over the J1939 CAN network.
The INTELLISYS controller sends speed setpoints to the engine (software versions 2.0 and
greater) and receives diagnostic and run time data from the engine over the J1939 CAN
network. A frequency throttle interface with the engine is used for software versions earlier
then 2.0. Figure 2 shows the connections between the engine and INTELLISYS controller.
Ref: J1939 Data Link - The CAN network is a single pair shielded cable located with or
attached to the W1 main harness. Figure 3 shows a layout of the CAN harness or backbone
as it is referred to. The termination resistors (Terminator) are important to prevent reflections
on the transmission line and must be in place for the network to function properly. The shield
from the cable is connected to the machine frame at the INTELLISYS controller end.
The engine diagnostics connector is located inside the control panel. This is used to connect
the engine manufacturer’s service tools to the CAN network. This connector also provides 24
VDC to power these service tools.
Содержание NHP10-425WCU-EU-FX-T3
Страница 2: ...2...
Страница 4: ...2...
Страница 7: ...3 TABLE OF CONTENTS Operation Maintenance Manual TITLE PAGE SYSTEM DIAGRAMS 73...
Страница 8: ...4...
Страница 9: ...5 Foreword...
Страница 13: ...9 Safety...
Страница 21: ...17 General Information...
Страница 24: ...20...
Страница 25: ...21 Operating Instructions...
Страница 43: ...39 Maintenance...
Страница 56: ...52...
Страница 57: ...53 Lubrication...
Страница 60: ...56...
Страница 61: ...57 Fault Finding...
Страница 68: ...64...
Страница 69: ...65 Electrical...
Страница 73: ...Electrical Operating Maintenance Manual 69 Electronic Control Systems...
Страница 74: ...Always use Ingersoll Rand Replacement parts 70...
Страница 75: ...Electrical Operating Maintenance Manual 71...
Страница 77: ...73 System Diagrams...