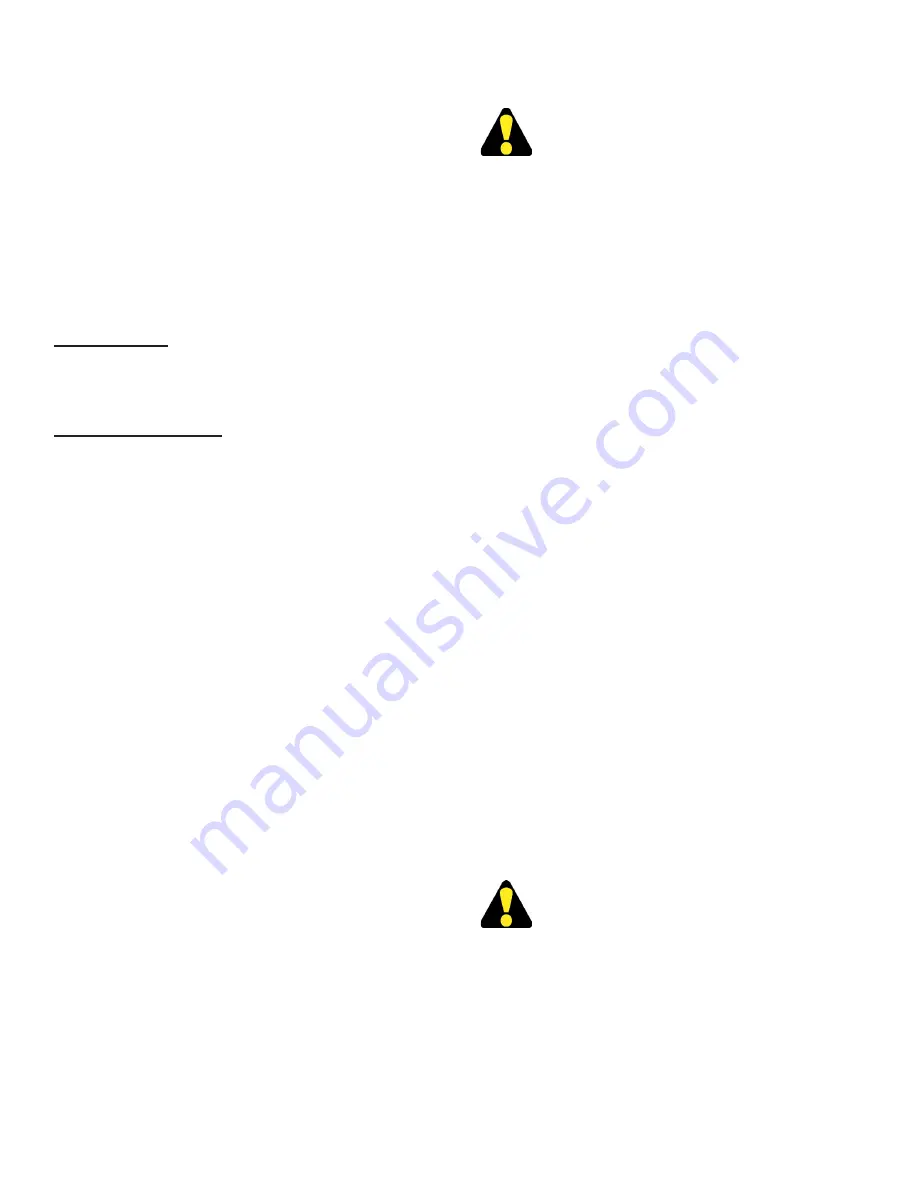
16
REPLACING CROWNED BANDWHEEL TIRES
1.
Loosen the worn tire with a screwdriver or other flat
tool.
2.
Stretch the tire if necessary to remove it.
3.
Clean the bandwheel and install a new tire by
stretching it over the bandwheel.
INSERT-TYPE SAW GUIDES
Back-Up Inserts
1.
Reverse back-up inserts for additional wear life,
then replace when all surfaces are worn.
Roller Back-Up Bearng
1.
These bearings are sealed and packed for life with
a special lubricant. They can be replaced by:
(a)
Removing the snap ring;
(b)
Pulling out the bearing
and shaft;
(c)
New bearings are easily installed with
a light press fit.
ELECTRIC MOTORS
1.
Follow the manufacturer's maintenance instructions
for each electric motor.
HEAD COMPONENTS
1.
Wipe oil onto the post occasionally. Then move the
post up and down through the slide block several
times.
2.
Oil the upper and idler bandwheel slides and band
tension screw each month.
3.
Wheel bearings are sealed and lubricated for life.
SPINDLE DRIVE BEARINGS
1.
THe spindle drive shaft has two (2) bearings with
grease fittings. Lubricate the bearings as necessary
according to the Lubrication Chart.
WHEEL BRUSH
1.
Check the lower bandwheel brush occasionally for
correct position. Adjust the brush so it just touches
the bandwheel tire.
MAINTENANCE
Too much pressure of the brush wll score the
bandwheel tre.
2.
Replace the brush when necessary.
BAND DRIVE BELT
1.
The belt driving the input sheave will stretch during
use. This stretch should be taken up by moving the
drive motor on its mounting plate.
2.
To replace the belt:
(a)
Loosen the screws that
mount the drive motor and slide the motor to the
left;
(b)
Slip the old belt from the pulleys and install
the new one;
(c)
Slide the drive motor to the right
to tighten the belt so there is very little deflection of
the belt;
(d)
When correct belt tension is acheived,
tighten the screws.
4.
Tension the belt by loosening the motor mounting
bolts, slide the motor to the right until correct tension
is obtained and then tighten the bolts.
MIST COOLANT (If Suppled)
1.
Intermittent coolant stream indicates an air leak.
Check all joints.
2.
Clogging may occur if waxed-based or other
coolants are used. Your DoALL sales representative
can provide complete information about various
coolants.
3.
Keep the mist applicator nozzle and filter clean.
If the center nylon coolant tube needs replacing,
remove the entire applicator tube. Insert new nylon
tube and trim off excess flush with nozzle. Make
sure all joints are sealed and tight after applicator
tube is reinstalled.
MACHINE CLEANING
Stop the machne when cleanng the machne
or openng bandwheel doors or covers.
1.
Keep the machine and its parts as clean as possible
to prevent excessive wear and damage.
2.
Remove the chip drawer and dispose of the chips
when necessary.
Содержание 3613-V5
Страница 1: ...3613 V5 Serial No 569 04101 to Band Sawing Machine Instruction Manual...
Страница 5: ...MACHINE DIMENSIONS INCHES 03 MILLIMETERS 1 mm FLOOR PLAN...
Страница 7: ...MACHINE FEATURES FRONT VIEW...
Страница 8: ...MACHINE FEATURES Continued REAR VIEW...
Страница 17: ...13 LUBRICATION NEXT 2 PAGES...
Страница 19: ...15 LUBRICATION DIAGRAM FRONT VIEW REAR VIEW...