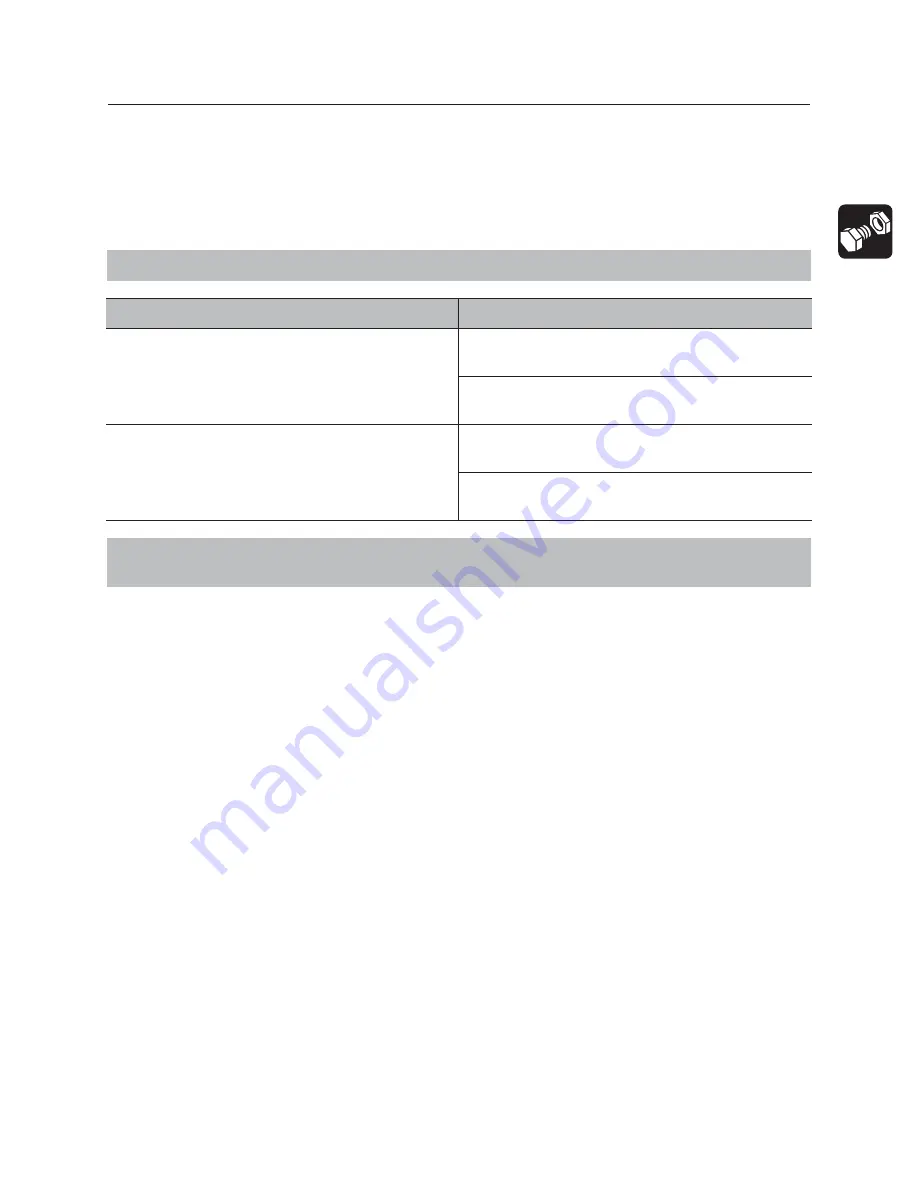
JT40/JT40 All Terrain Operator’s Manual
Systems and Equipment - 167
Downhole Tools
Backream Fluid Requirements
Backreaming is only successful when enough fluid reaches the bore. The amount of fluid needed depends
on size of bore and soil condition.
Follow these steps to find the
minimum
amount of fluid needed in perfect conditions.
IMPORTANT:
Use more fluid than recommended or the backream might be dry and unsuccessful.
Instructions
Example
1.
Find amount of fluid needed for your size of
backreamer. See the table on the next page.
U.S.
A 6” backreamer requires at least 1.47
gal/ft.
Metric
A 152-mm backreamer requires at least
18.24 L/m.
2.
Multiply this number by distance per minute
you plan to backream. The answer is an
estimate of amount of fluid you will need for
each minute of backreaming.
U.S.
1.5 gal x 2 ft/min = 3 gal for each minute of
backreaming.
Metric
18 L x .5 m/min = 9 L for each minute of
backreaming
IMPORTANT:
After you have determined how much fluid you will need, see your Ditch Witch
®
dealer for
nozzle recommendations.
Содержание JT40
Страница 1: ...JT40 JT40 All Terrain HRC and LRC Issue 1 0 Original Instruction Operator s Manual 053 2966 ...
Страница 79: ...Controls 78 JT40 JT40 All Terrain Operator s Manual Battery Disconnect ...
Страница 113: ...Drive 112 JT40 JT40 All Terrain Operator s Manual Shut Down Unit ...
Страница 119: ...Transport 118 JT40 JT40 All Terrain Operator s Manual Retrieve ...
Страница 147: ...Conduct a Bore 146 JT40 JT40 All Terrain Operator s Manual Remove Pullback Device ...
Страница 199: ...Complete the Job 198 JT40 JT40 All Terrain Operator s Manual Stow Tools ...
Страница 241: ...Service 240 JT40 JT40 All Terrain Operator s Manual As Needed ...
Страница 247: ...Specifications 246 JT40 JT40 All Terrain Operator s Manual Declaration of Conformity Information ...
Страница 250: ......
Страница 251: ......
Страница 252: ...JT40 JT40 All Terrain Operator s Manual Service Record 251 Service Record Service Performed Date Hours ...
Страница 253: ...Service Record 252 JT40 JT40 All Terrain Operator s Manual Service Performed Date Hours ...