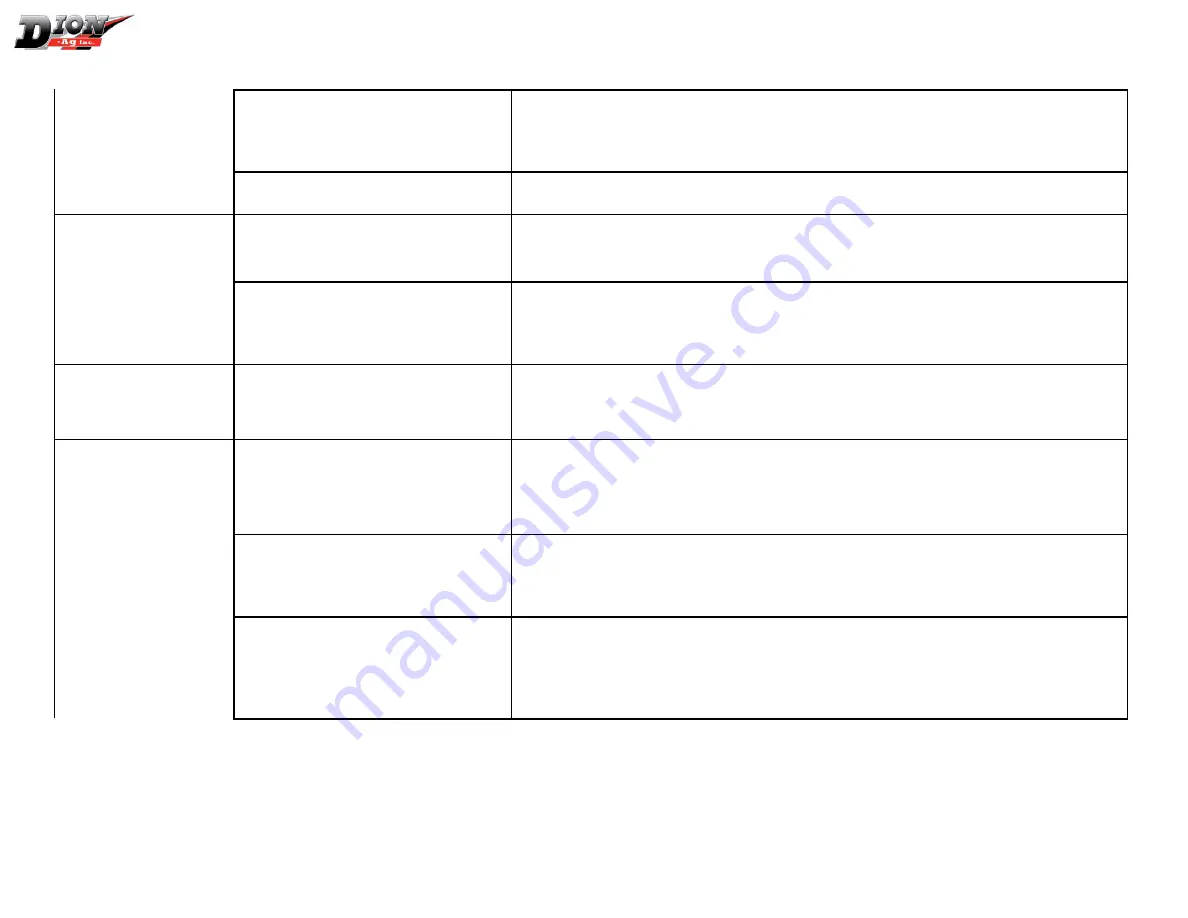
DIAGNOSTIC & TROUBLESHOOTING
99
Antenna internal damage
Electrical resistance between the colored wires is less than 800Ω or higher than 1kΩ
signaling that antenna coil wire are damaged or short. Or, there is a short circuit
between the signal wires and the ground.
Replace the antenna inside the detector roll.
Amplifier or controller damaged
Make sure the controller and amplifier (black electronic casings) are not damaged or
cracked. Refer to the service manual.
Drive failure
(shearbolt or clutch
slippage)
(Alarm)
Shearbolt on cutterhead shaft has
failed or friction clutch slipped.
Turn off the tractor, inspect the shearbolt and collect the broken halves if it is the
case. Replace the shearbolt with provided bolts in toolbox.
Refer to the friction clutch slippage section of this manual if equipped.
The cutterhead speed sensor is
damaged or out of adjustment
If the shearbolt or clutch is intact, the speed sensor might clearance might be too
large, or the sensor itself is defective.
Set the clearance to about 1 mm or 1/32" between the sensor tip and encoding
wheel or replace the sensor.
Emergency stop
error
(Alarm)
The emergency stop stays active
Make sure the emergency stop button on the control box is not damaged, stuck in
depressed position or that the cable is not cut or disconnected.
Replace or repair depending on the case.
Feedroll speed error
(Alarm)
Feedrolls are clogged with crop
If an overload has occurred and clogged the feedrolls, the overload protection clutch
on the transmission input pulley will slip and emit a growling sound. Reduce the PTO
rpm, then reverse the feedrolls to clear the harvester throat before restarting in
forward at low speed and rapidly increasing the rpm.
The detector stop pawl is stuck in
the ratchet wheel
If the stop pawl is jammed in the ratchet wheel, the solenoid will cycle between
pause and pulling cycles due to a current overload protection in the circuit. Engage
the PTO at idle, reverse the feedrolls to free the stop pawl. Forward motion should
now be possible.
Solenoid stroke is limited
If the solenoid can’t pull to its full stroke, it will cycle between pulling and pause
phases of a few seconds. Make sure the stop pawl pivot is greased and free of
movement. When the solenoid is activated, make sure there is still some play in the
pawl (the solenoid must pull only against the weight of the pawl and the spring
force).
Manual
N
o. F6918E003E v1.2
Содержание Scorpion 300
Страница 1: ...Operator s Manual FORAGE HARVESTER Manual No F6918E003E v1 2...
Страница 2: ...Manual No F6918E003E v1 2 2...
Страница 5: ...Manual No F6918E003E v1 2 5...
Страница 11: ...Manual No F6918E003E v1 2 11...
Страница 18: ...SAFETY RULES 18 Figure 5 Safety Decals Figure 6 Safety Decals Manual No F6918E003E v1 2...
Страница 19: ...SAFETY RULES 19 Figure 7 Safety Decals Figure 8 Safety Decals Manual No F6918E003E v1 2...
Страница 20: ...SAFETY RULES 20 Figure 9 Safety Decals Manual No F6918E003E v1 2...
Страница 21: ...SAFETY RULES 21 Figure 10 Safety Decals Manual No F6918E003E v1 2...
Страница 84: ...MAINTENANCE AND ADJUSTMENTS 84 Figure 93 Universal joints transmission chain Manual No F6918E003E v1 2...
Страница 85: ...MAINTENANCE AND ADJUSTMENTS 85 Figure 94 Feedrolls linkage bearings and chains Manual No F6918E003E v1 2...
Страница 88: ...MAINTENANCE AND ADJUSTMENTS 88 Figure 98 Processor rolls lubrification Manual No F6918E003E v1 2...
Страница 109: ...Manual No F6918E003E v1 2 109...