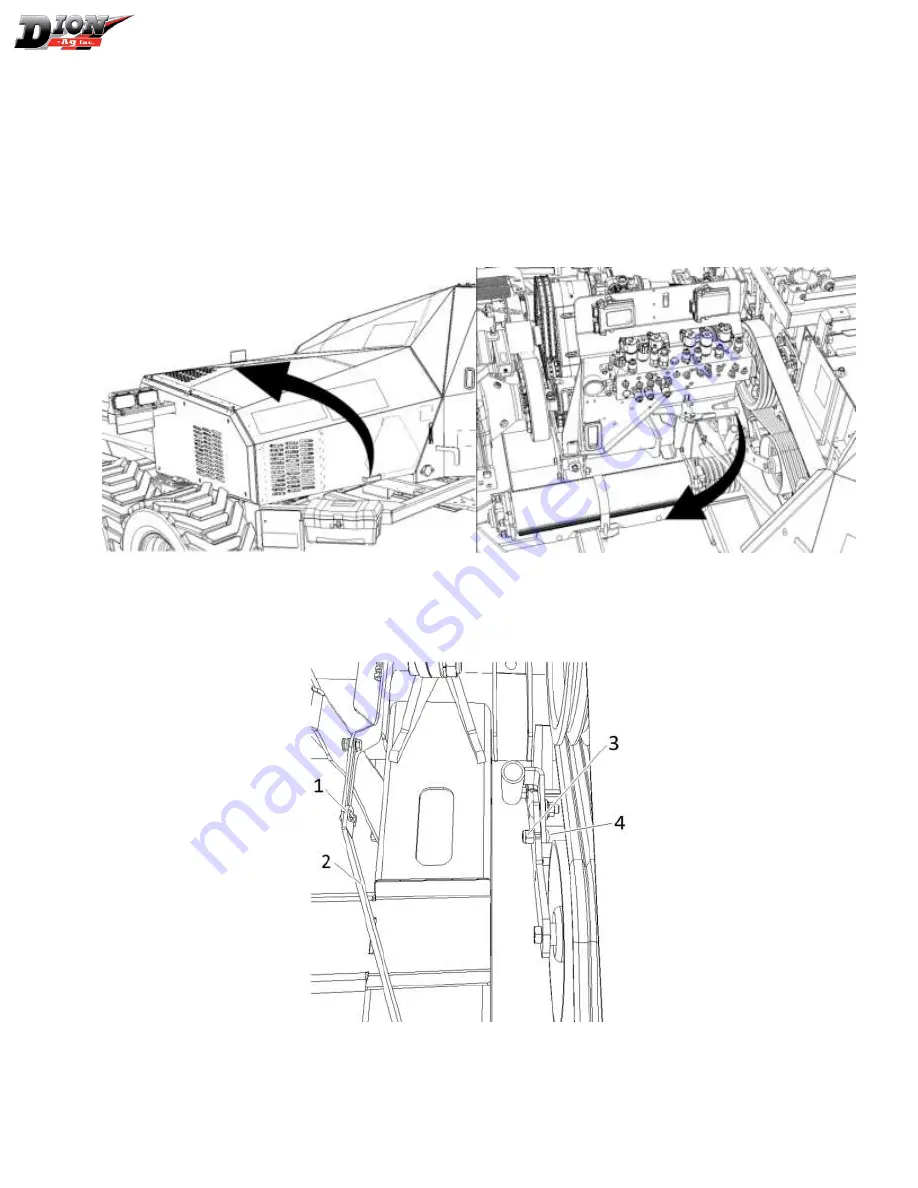
SETUP
30
CONFIGURING FOR CORN HARVEST SETUP
To harvest corn, the PROCESSOR must be partially re-assembled by installing the top roll in position. Follow
the instructions:
STEP 1 - FIGURE 21
Open the main guard then pivot the hydraulic manifold to free space around the accelerator belt binder.
Figure 21 Main guard and manifold
STEP 2 - FIGURE 22
Remove the lock pin (item 1) and the header lift cylinder locking arm (item 2). Remove the bolt that locks the
accelerator binder (item 3 and 4).
Figure 22 Cylinder lever arm and lock bolt
Manual
N
o. F6918E003E v1.2
Содержание Scorpion 300
Страница 1: ...Operator s Manual FORAGE HARVESTER Manual No F6918E003E v1 2...
Страница 2: ...Manual No F6918E003E v1 2 2...
Страница 5: ...Manual No F6918E003E v1 2 5...
Страница 11: ...Manual No F6918E003E v1 2 11...
Страница 18: ...SAFETY RULES 18 Figure 5 Safety Decals Figure 6 Safety Decals Manual No F6918E003E v1 2...
Страница 19: ...SAFETY RULES 19 Figure 7 Safety Decals Figure 8 Safety Decals Manual No F6918E003E v1 2...
Страница 20: ...SAFETY RULES 20 Figure 9 Safety Decals Manual No F6918E003E v1 2...
Страница 21: ...SAFETY RULES 21 Figure 10 Safety Decals Manual No F6918E003E v1 2...
Страница 84: ...MAINTENANCE AND ADJUSTMENTS 84 Figure 93 Universal joints transmission chain Manual No F6918E003E v1 2...
Страница 85: ...MAINTENANCE AND ADJUSTMENTS 85 Figure 94 Feedrolls linkage bearings and chains Manual No F6918E003E v1 2...
Страница 88: ...MAINTENANCE AND ADJUSTMENTS 88 Figure 98 Processor rolls lubrification Manual No F6918E003E v1 2...
Страница 109: ...Manual No F6918E003E v1 2 109...