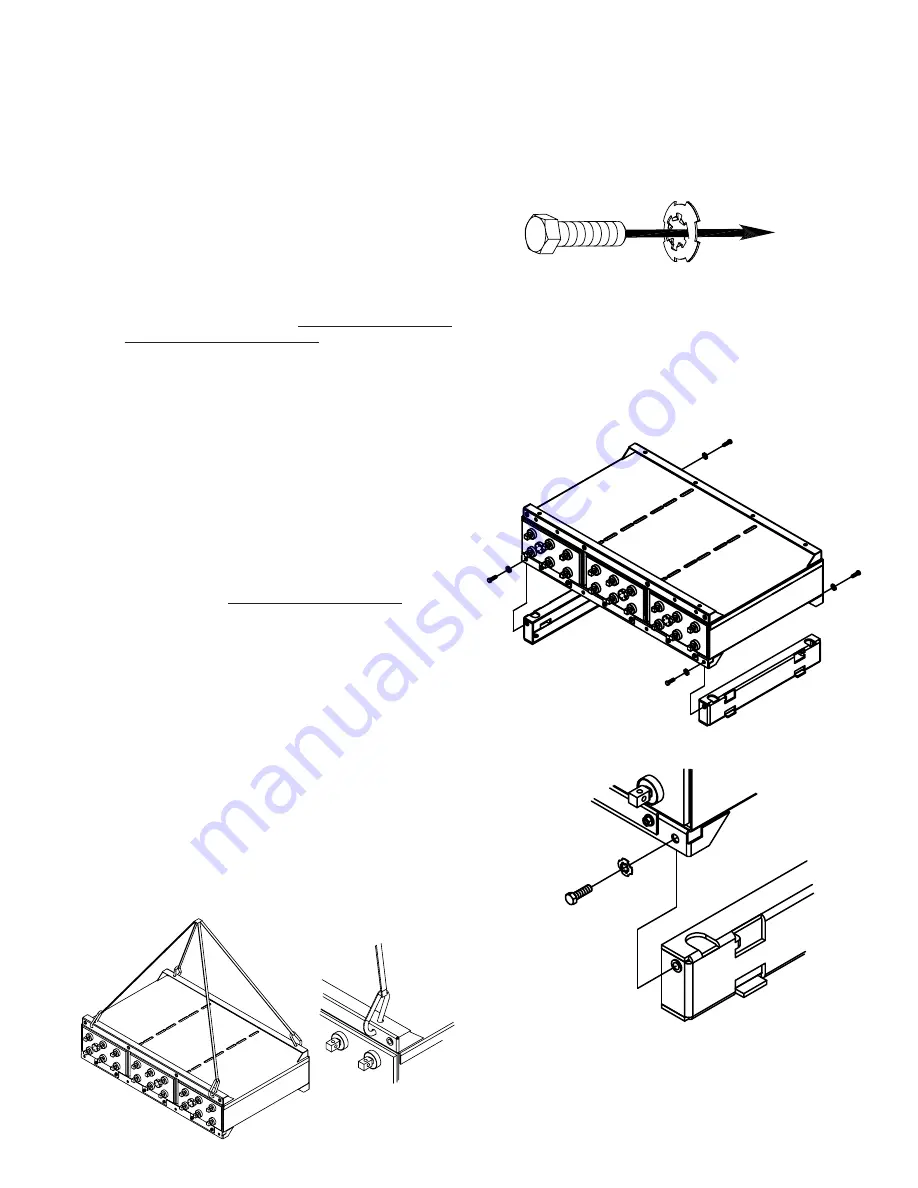
4.
Anchor holes can be marked and drilled with bases in place.
Consult Appendix C for anchor hole pattern. All anchor
holes in base are required to be used to meet seismic re-
quirements. Consult local building codes for anchor
bolt requirements. Anchor bolts not included due to site
specific requirements.
5.
Remove hardware holding modules together and holding
modules to skid. Hardware removed from modules will
be reused to attach modules to bases and to each other.
Hardware holding modules to skid can be discarded.
6. Module / Base Shimming
a. Prior to installation, the floor on which the battery
string is to be installed should be level and capable of
supporting the weight of the battery string. A 1° taper
on a floor can result in a ½" variation at the top of one
eight-high stack of modules. This can be compounded
by the tolerance of each module.
b. Standard steel shim stock such as AISI/SAE 1010 can be
used. Stainless steel is not required since these batteries
are AGM and should not be exposed to a corrosive
environment. Shim dimensions will vary depending on
the location and levelness. Shims are not provided by
East Penn due to site specific requirements.
c. If floors are not level, shim material can be placed under
each of the base supports within a battery string until
they are level. All base supports within a battery string
must be level with each other – do not level individual
bases as this could cause variation in height from one
stack to another.
d. It is recommend to place an interstack connector on the
system to ensure no stress will be placed on the cell
posts. Reference Safety Section of this manual and
battery schematic for all necessary precautions. If the
connector is aligned, it may be removed and the module
installation can continue.
e. Reference Appendix C for
Base Support layout dimensions
f. Once all the modules are installed and aligned, joining
plates (pg b.7 Part 3) which are provided with the parts
kit should be installed at the top of every stack. This
provides an additional tool to ensure levelness.
g. Assuming these guidelines are followed, the electrical
connections can be installed easily without any issues
of misalignment or undue stress on the cell posts.
CAUTION: Never lift more than one module at a time with
the supplied lifting slings.
7. Install modules onto bases using supplied lifting straps.
Two straps required to lift each module. Consult below
diagram for proper sling attachment.
8. Module connecting hardware is furnished with a dragon tooth
washer in place of a lock washer and flat washer.
The dragon tooth washer is used to enhance the electrical
conductivity of the grounding system within a stack of
modules. To ensure the dragon tooth washer is installed
correctly; the curve of the washer must face away from the
bolt head. Stack to stack grounding electrical conductivity
is the responsibility of the installer.
b.5
9. Installed battery string should be compared to battery string
layout drawing for correctness. As each module is installed
all hardware should be checked for proper torque before
proceeding to next module.
a. Connecting the module to the base will require four 3/8-16
x 1.25" bolts. One bolt for the front and one bolt for the
rear required for each base. Consult “Hardware Torque
Requirements” (pg b.4) for proper torque values.
b. Connect the modules to each other with eight 3/8-16 x
1.25
"
bolts & dragon tooth washers. Four for the front and
four in the rear of each module. Procedure to be repeated
until all modules are installed. Consult “Hardware Torque
Requirements” (pg b.14) for proper torque values.