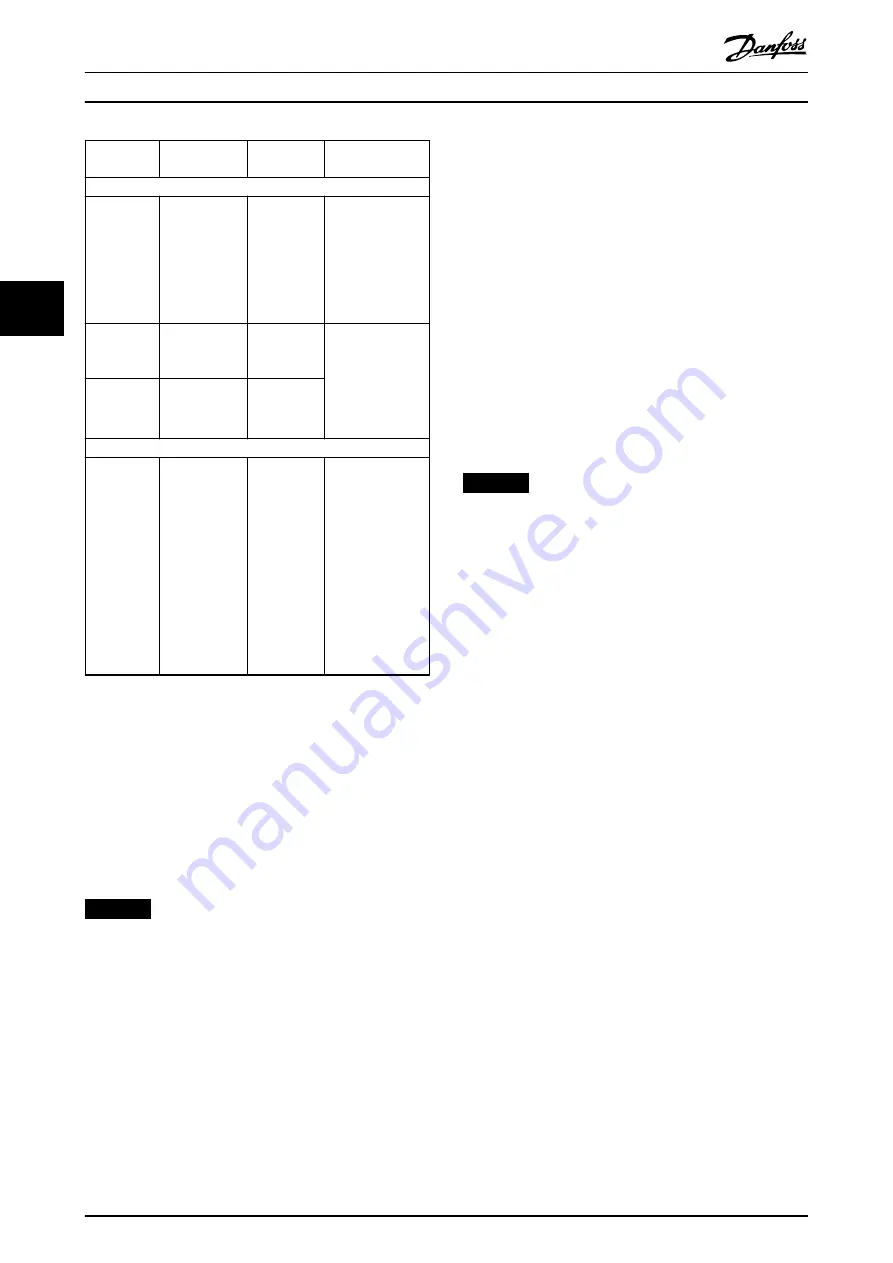
Terminal
Parameter
Default
setting
Description
Serial communication
61
–
–
Integrated RC filter
for cable shield.
ONLY for
connecting the
shield when
experiencing EMC
problems.
68 (+)
Parameter
group 8-3* FC
port settings
–
RS485 interface. A
control card switch
is provided for
termination
resistance.
69 (-)
Parameter
group 8-3* FC
port settings
–
Relays
01, 02, 03
Parameter 5-40
Function Relay
[1] Control
Ready
Form C relay
output. These
relays are in
various locations
depending on the
frequency
converter configu-
ration and size.
Usable for AC or
DC voltage and
resistive or
inductive loads.
Table 4.2 Terminal Descriptions - Serial Communication
4.8.2 Wiring to Control Terminals
Control terminal connectors can be unplugged from the
frequency converter for ease of installation, as shown in
For details about STO wiring, refer to
NOTICE
Keep control cables as short as possible and separate
them from high-power cables to minimize interference.
1.
Loosen the screws for the terminals.
2.
Insert sleeved control cables into the slots.
3.
Fasten the screws for the terminals.
4.
Ensure that the contact is firmly established and
not loose. Loose control wiring can be the source
of equipment faults or less than optimal
operation.
See
chapter 9.5 Cable Specifications
for control terminal
cable sizes and
chapter 7 Application Examples
for typical
control cable connections.
4.8.3 Enabling Motor Operation
(Terminal 27)
A jumper wire is required between terminal 12 (or 13) and
terminal 27 for the frequency converter to operate when
using factory default programming values.
•
Digital input terminal 27 is designed to receive
24 V DC external interlock command.
•
When no interlock device is used, wire a jumper
between control terminal 12 (recommended) or
13 to terminal 27. The jumper provides an
internal 24 V signal on terminal 27.
•
Only for GLCP: When the status line at the
bottom of the LCP reads
AUTO REMOTE COAST
, it
indicates that the unit is ready to operate but is
missing an input signal on terminal 27.
NOTICE
UNABLE TO START
The frequency converter cannot operate without a signal
on terminal 27, unless terminal 27 is reprogrammed.
4.8.4 Mechanical Brake Control
In hoisting/lowering applications, it is necessary to
control an electro-mechanical brake.
•
Control the brake using any relay output or
digital output (terminal 27).
•
Keep the output closed (voltage-free) as long as
the frequency converter is unable to keep the
motor at standstill, for example due to the load
being too heavy.
•
Select
[32] Mechanical brake control
in
parameter
group
5-4* Relays
for applications with an electro-
mechanical brake.
•
The brake is released when the motor current
exceeds the preset value in
parameter 2-20 Release Brake Current
.
•
The brake is engaged when the output frequency
is less than the frequency set in
parameter 2-22 Activate Brake Speed [Hz]
, and only
if the frequency converter carries out a stop
command.
If the frequency converter is in 1 of the following
situations, the mechanical brake immediately closes.
•
In alarm mode.
•
In an overvoltage situation.
•
STO is activated.
•
Coast command is given.
Electrical Installation
VLT
®
Midi Drive FC 280
20
Danfoss A/S © 10/2017 All rights reserved.
MG07A402
4
4
Содержание VLT Midi Drive FC 280
Страница 1: ...ENGINEERING TOMORROW Operating Guide VLT Midi Drive FC 280 vlt drives danfoss com ...
Страница 2: ......