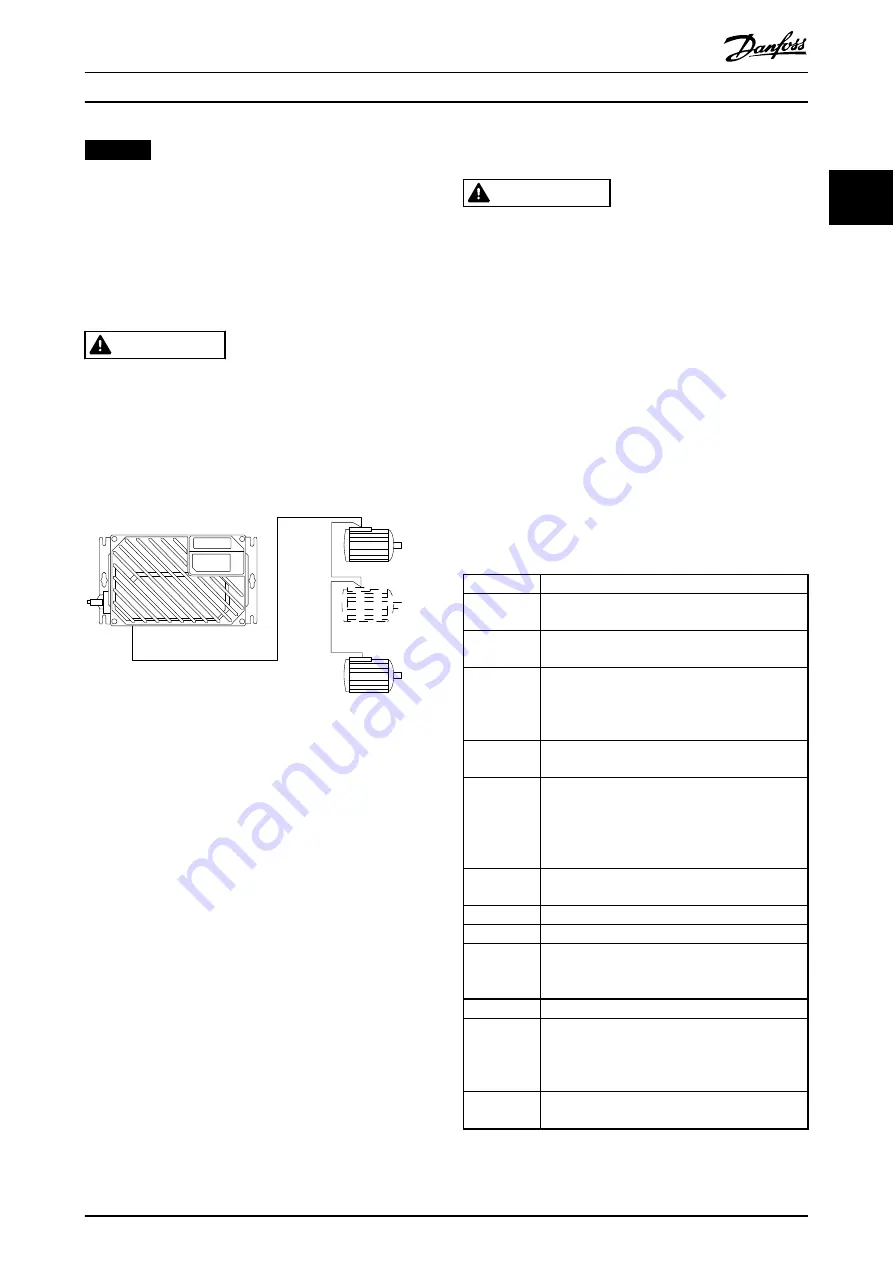
NOTICE
•
Installations with cables connected in a
common joint as in
, is only
recommended for short cable lengths
(maximum 10 m (32.8 ft)).
•
When motors are connected in parallel,
parameter 1-29 Automatic Motor Adaptation
(AMA)
cannot be used.
CAUTION
INSUFFICIENT MOTOR PROTECTION
The electronic thermal relay (ETR) of the frequency
converter cannot be used as motor protection for the
individual motor in systems with parallel-connected
motors. Provide further motor protection by thermistors
in each motor or individual thermal relays. Circuit
breakers are not suitable as protection.
130BB706.10
Illustration 2.15 Parallel Connection of Motors
Problems can arise at start-up and at low RPM values,
when motor sizes differ widely. Motors of low rated motor
power have a relatively high ohmic resistance in the stator.
This high resistance calls for a higher voltage at start and
at low RPM values. To resolve such a problem:
•
reduce the load during startup, on the motor of
lowest rated motor power
•
configure parallel connections only between
motors of comparable rated motor power
2.4.5 Control Wiring
WARNING
UNINTENDED START
When frequency converter is connected to AC mains
input power, the motor can start at any time. The
frequency converter, motor, and any driven equipment
must be in operational readiness. Failure to be in
operational readiness when the frequency converter is
connected to AC mains could result in death, serious
injury, equipment, or property damage.
•
It is recommended that control wiring is rated for
600 V.
•
Isolate control wiring from high-power
components in the frequency converter.
•
If the frequency converter is connected to a
thermistor, for PELV isolation, ensure control
wiring is reinforced/double insulated.
•
See
chapter 8.2 General Specifications
for control
terminal wiring sizes and maximum loads.
Terminal No. Function
01, 02, 03
Relay 1 output. Useable for AC or DC voltage and
resistive or inductive loads.
04, 05, 06
Relay 2 output. Useable for AC or DC voltage and
resistive or inductive loads.
12, 13
24 V DC digital supply voltage. Useable for digital
inputs and external transducers. To use the 24 V
DC for digital input common, programme
parameter 5-00 Digital I/O Mode
for PNP operation.
18, 19, 32, 33 Digital inputs. Selectable for NPN or PNP function
in
parameter 5-00 Digital I/O Mode
. Default is PNP.
27, 29
Digital inputs or outputs. Programmable for either
parameter 5-01 Terminal 27 Mode
for terminal 27
and
parameter 5-02 Terminal 29 Mode
for 29
selects input/output function. Default setting is
input.
35
Common (-) for external 24 V control back up
supply. Optional.
36
Ex 24 V control back up supply. Optional.
37
Safe Stop. See Safe Stop installation for details.
20
Common for digital inputs. To use for digital input
common, programme
parameter 5-00 Digital I/O
Mode
for NPN operation.
39
Common for analog output.
42
Analog output. Programmable for various
functions in parameter group 6-5*. The analog
signal is 0-20 mA or 4-20 mA at a maximum of
500
Ω
.
50
10 V DC analog supply voltage. 15 mA maximum
commonly used for a potentiometer or thermistor.
Installation
Operating Guide
MG04F402
Danfoss A/S © 05/2016 All rights reserved.
19
2
2