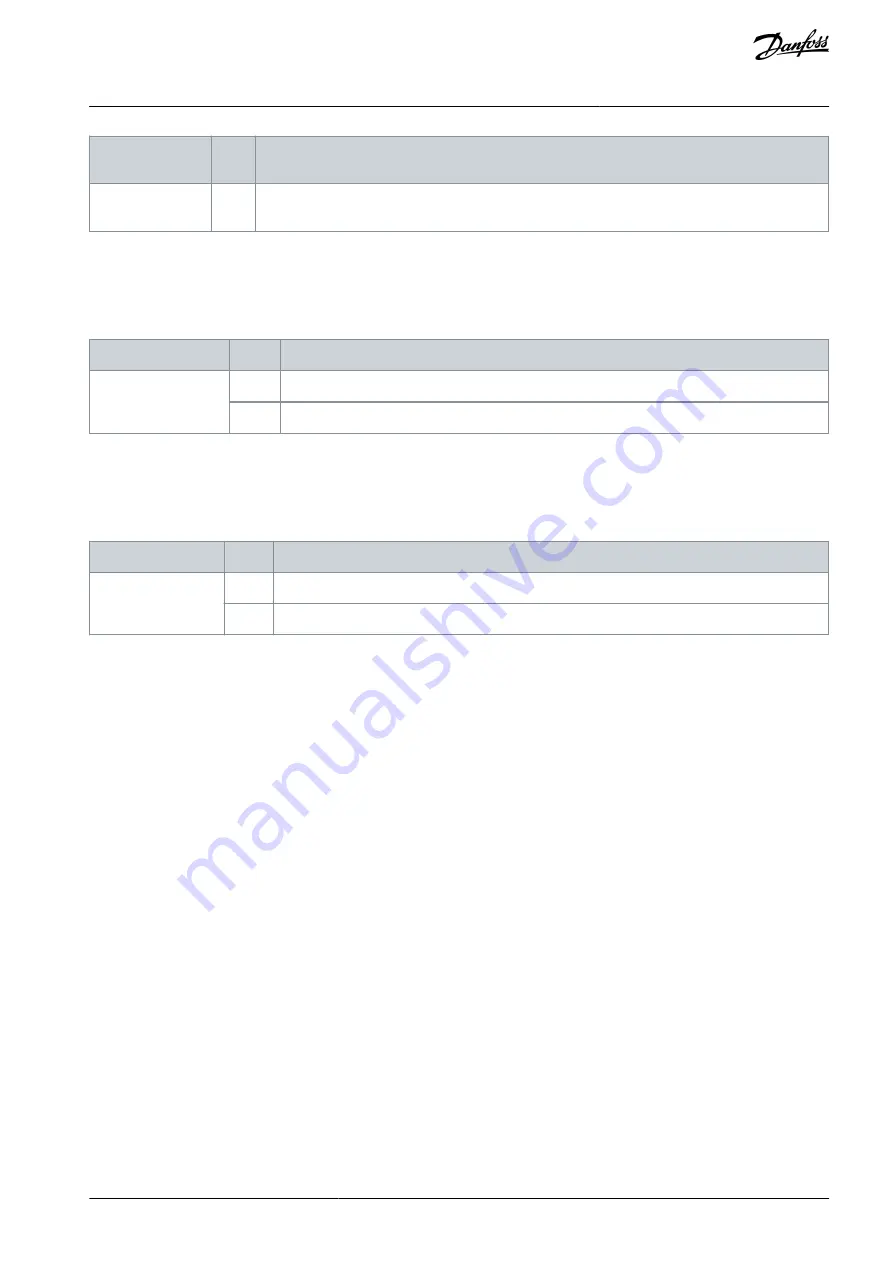
•
•
•
•
•
•
•
•
•
•
•
•
•
Character posi-
tion
Code Description
DE
Signal lights and reset STO/SS1 with emergency push- safely limited speed (HTL
encoder)
The signal light and reset button option includes signal lights on the control compartment door for run and fault states of the AC
drive. The door also has a button for the reset function of the drive.
5.7.6.10 Emergency Switch Off
Table 63: Door-mounted Option Type Codes
Character position
Code
Description
28–29
D2
Emergency switch off + emergency push-button
DA
Signal lights and reset emergency switch off and emergency push-button
The emergency switch off option uses an input contactor to disconnect the drive from mains. Pushing the emergency stop push-
button on the control compartment door opens the control circuit of the input contactor.
5.7.6.11 STO with Emergency Push-button on Door
Table 64: Door-mounted Option Type Codes
Character position
Code
Description
28–29
D3
STO with emergency push-button (no functional safety)
DB
Signal lights and reset STO with emergency push-button (no functional safety)
This option provides the STO (Safe Torque Off) function via an emergency push-button mounted on the door of the control com-
partment. The control terminals of the control card are extended from inside the drive module and routed out to the terminal block
set -XD2 in the control compartment. The emergency push-button is wired between terminals -XD2.10 and -XD2.19.
Activating the emergency push-button prevents the unit from generating the voltage required to rotate the motor. The option pro-
vides:
Safe Torque Off (STO), as defined by EN IEC 61800-5-2.
Stop Category 0, as defined in EN 60204-1.
5.8 Connecting Motor, Mains, and Ground Cables
5.8.1 Power Cabling and Grounding Considerations
Motor and mains connections
Size the wiring according to the input current of the drive. For maximum wire sizes, see the
Electrical Data
section.
Use cables rated for 75 °C (167 °F) of insulation for UL installations.
Comply with local and national electrical codes for cable sizes.
Follow motor manufacturer wiring requirements.
Motor wiring knockouts or access panels are provided on the pedestal of IP21/IP54 (NEMA 1/NEMA 12) units.
Do not wire a starting or pole-changing device (for example Dahlander motor or slip ring induction motor) between the drive
and the motor.
Ground connection
Ground the drive in accordance with applicable standards and directives.
Use a dedicated ground wire for input power, motor power, and control wiring.
Do not ground 1 drive to another in a daisy chain fashion.
Keep the ground wire connections as short as possible.
Follow motor manufacturer wiring requirements.
AQ357954340588en-000201 / 130R0881 | 81
Danfoss A/S © 2020.09
Electrical Installation
VLT® Refrigeration Drive FC 103
Operating Guide