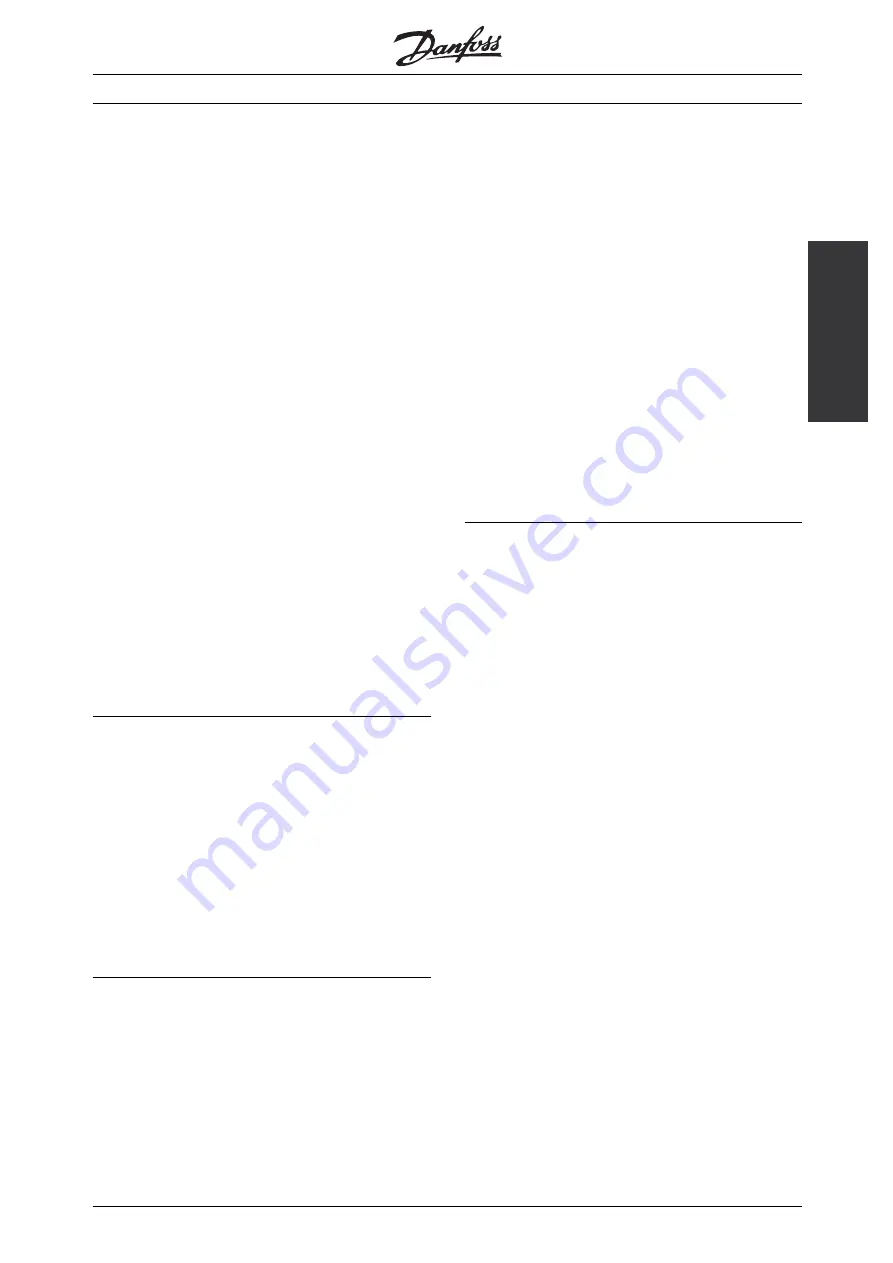
VLT® 5000 Crane
Introduction
VLT 5000 Crane controls the mechanical brake
of the crane. It holds the load when speed is
below the set minimum value.
VLT 5000 Crane monitors that the system brake
holds and releases the load as required. In case
of faults,
Brake fault 2
is displayed.
Load determination and speed measuring will ensure
that the working range is not exceeded. For each
load contact the max. allowed motor speed is set
(parameters 701 and 702). VLT 5000 Crane cuts off
automatically when motor speed for the activated
load contact exceeds the value recorded
Positioning
The reference signal is higher than minimum. The
condition for VLT ready is fulfilled. 24V is applied
to terminal 17 (parameter 301).
During positioning the speed is limited to 750 RPM
for VLT 5052-5072, 1125 RPM for VLT 5102, 1500
RPM for VLT 5152-5202, respectively, and system
brake is not activated at 0 RPM.
Quick stop with brake
If control signal to terminal 27(parameter 304)
is removed, the motor ramps down according
to the alternative ramp (parameter 212) and the
brake is activated momentarily.
■
Operating Status at Local Operation
It is only possible to change to local operation from
Control Ready
. Besides, parameter 003 must be
set for
Local
and parameter 010 for
Enable
. VLT
5000 Crane can be operated over the control panel
or over parameters 004 - 009. This state acts
as
Normal operating state
, however there are no
load functions and monitoring of system brake.
This means that the whole working range from 0
- 3000 RPM can be used and the crane system
brake is controlled at approx. 0 RPM.
■
Fault Status at Remote and Local Control
Brake fault 1
VLT 5000 Crane monitors in the state VLT ready that
the system brake holds the load as required. If that is
not the case,
Brake fault 1
applies and the load is slowly
lowered according to the speed set in parameter 704.
Brake fault 2
VLT 5000 Crane monitors in the state normal operation,
that the system brake releases the load as required.
If that is not the case
Brake fault 2
applies. The unit
will cut in the system brake again. This means that the
system brake signal is deactivated. This ensures that
the load is held. Then the inverter section is disabled.
Brake fault 2
may also occur during commissioning
if the encoder connection is not correct.
At reference 0 the unit goes back to the state VLT ready.
Function fault
VLT 5000 Crane monitors several functions. Should
severe faults occur, the unit will trip automatically.
For fault types, see
Trouble-shooting
To reset the fault switch off/switch on the mains
supply and press the stop/reset button.
■
System Components
Motor
Select the motor type for the rated output in question
in parameters 102-106, 150-155..
Incremental Encoder
The encoder must meet the following requirements:
•
Pulses pr. revolution, see parameter 329
•
Outputs: A (0º), inv. A, B (90º), inv. B, Z, inv. Z
•
Supply: +5 V ±5%
•
Max. current (5V supply): 200mA
Note that outputs must be compatible with RS 422!
Brake resistor
See data for calculation in
Control with brake function
.
MG.50.N4.02 - VLT is a registered Danfoss trademark
11