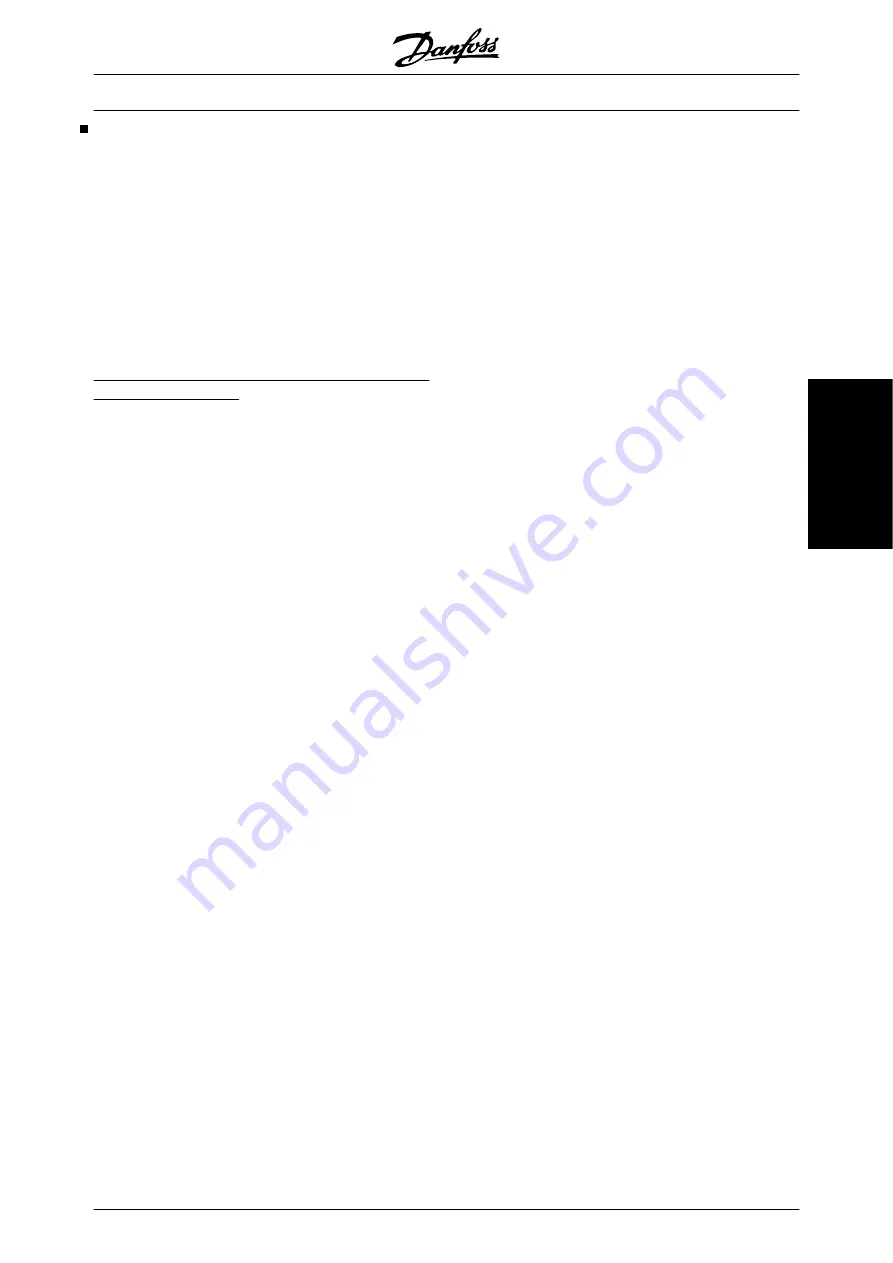
Electrical installation - EMC precautions
The following is a guideline to good engineering prac-
tice, when installing drives. Following these guidelines
is advised, where compliance with EN 61000-6-3, EN
61000-6-4, EN 55011 or EN 61800-3
First environ-
ment
is required. If the installation is in EN 61800-3
Second environment,
i.e. industrial networks or in an
installation that has its own transformer, it is accepta-
ble to deviate from these guidelines. It is however not
recommended. See also
CE labelling,
Emission
and
EMC test results
under special conditions in the Design
Guide for further details.
Good engineering practice to ensure EMC-correct
electrical installation:
•
Use only braided screened/armoured motor
cables and braided screened/armoured con-
trol cables. The screen should provide a min-
imum coverage of 80%. The screen material
must be metal, not limited to but typically cop-
per, aluminium, steel or lead. There are no
special requirements for the mains cable.
•
Installations using rigid metal conduits are
not required to use screened cable, but the
motor cable must be installed in conduit sep-
arate from the control and mains cables. Full
connection of the conduit from the drive to the
motor is required. The EMC performance of
flexible conduits varies a lot and information
from the manufacturer must be obtained.
•
Connect the screen/armour/conduit to earth
at both ends for motor cables as well as for
control cables. In some cases, it is not pos-
sible to connect the screen in both ends. In
these cases, it is important to connect the
screen at the frequency converter. See also
Earthing of braided screened/armoured con-
trol cables
.
•
Avoid terminating the screen/armour with
twisted ends (pigtails). Such a termination in-
creases the high frequency impedance of the
screen, which reduces its effectiveness at
high frequencies. Use low impedance cable
clamps or EMC cable glands instead.
•
It is important to ensure good electrical con-
tact between the mounting plate on which the
frequency converter is installed and the metal
chassis of the frequency converter. However,
this does not apply to IP 54 units as they are
designed for wall-mounting and VLT
5122-5552 380-500 V, 5042-5602 525-690 V
and VLT 5032-5052 200-240 V in IP20/
NEMA 1 enclosure and IP 54/NEMA 12 en-
closure.
•
Use starwashers and galvanically conductive
installation plates to secure good electrical
connections for IP00 and IP20 installations.
•
Avoid using unscreened/unarmoured motor
or control cables inside cabinets housing the
drive(s), whenever this can be avoided.
•
An uninterrupted high frequency connection
between the frequency converter and the
motor units is required for IP54 units.
The illustration shows an example of an EMC-correct
electrical installation of an IP 20 frequency converter;
the frequency converter has been fitted in an installa-
tion cabinet with an output contactor and connected to
a PLC, which in this example is installed in a separate
cabinet. In IP 54 units and VLT 5032-5052, 200-240 V
in IP20/IP21/NEMA 1 enclosure screened cables are
connected by using EMC conduits to ensure proper
EMC performance. See illustration. Other ways of
making the installation may have as good an EMC
performance, provided the above guide lines to engi-
neering practice are followed.
Please note, that when the installation is not carried
through according to the guideline as well as when
unscreened cables and control wires are used, some
emission requirements are not complied with, al-
though the immunity requirements are fulfilled. See the
section
EMC test results
in the Design Guide for further
details.
VLT
®
5000 Design Guide
MG.52.B2.02 - VLT
®
is a registered Danfoss trademark
77
Electrical installation