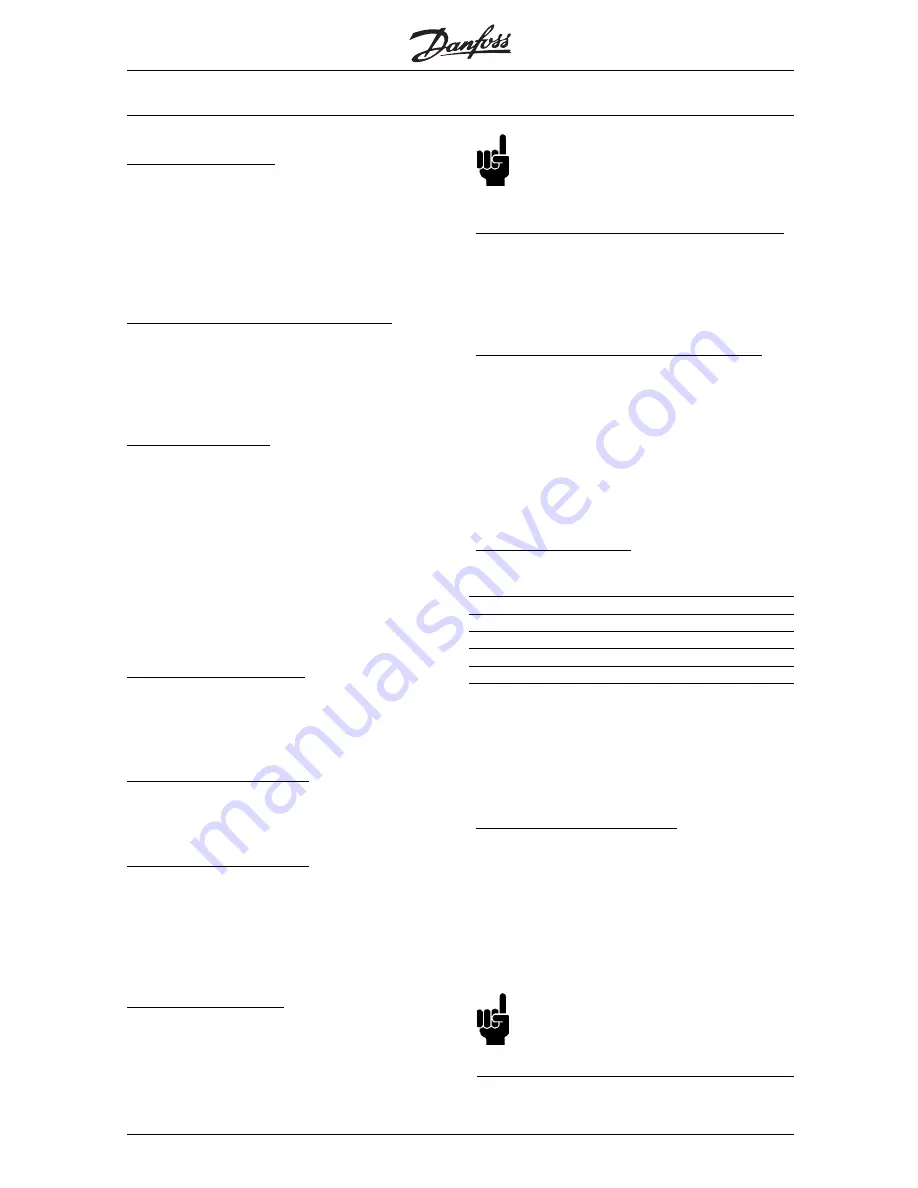
VLT® 5000/ 5000 FLUX/ 6000 HVAC/
8000 AQUA PROFIBUS
Bit 04, Quick stop/Ramp
Quick stop using the ramp time of parameter 212.
In the case of bit 04 = "0", a quick stop occurs.
In the case of bit 04 = "1", the frequency converter
can start if the other start conditions are satisfied.
Note: The selection in parameter 503 determines
how bit 04 is linked with the corresponding
function of the digital inputs.
Bit 05, Save output frequency/Ramp possible
In the case of bit 05 = "0", the current output frequency is
being maintained even if the reference value is modified.
In the case of bit 05 = "1", the frequency converter can
perform its regulating function again; operation occurs
according to the respective reference value.
Bit 06, Ramp stop/Start
Normal ramp stop using the ramp times of the
parameters 207/208 or 209/210.
In addition, activation of the output relay 01 or 04
if the output frequency is 0 Hz if Relay 123 has
been selected in parameter 323 or 326.
Bit 06 = "0" leads to a stop.
In the case of bit 06 = "1", the frequency converter
can start if the other start conditions are satisfied.
Note: The selection in parameter 505 determines
how bit 06 is linked with the corresponding
function of the digital inputs.
Bit 07, Without function/Reset
Reset after switching off.
In the case of bit 07 = "0", no reset occurs.
In the case of a slope change of bit 07 to "1",
a reset occurs after switching off.
Bit 08, Fixed speed 1 OFF/ON
Activation of the preprogrammed speed in parameter
509 (bus JOG 1). JOG 1 is only possible if bit
04 = "0" and bit 00 - 03 = "1".
Bit 09, Fixed speed 2 OFF/ON
Activation of the preprogrammed speed in parameter
510 (bus JOG 2). JOG 2 is only possible if bit
04 = "0" and bit 00 - 03 = "1".
If both JOG 1 and JOG 2 are activated (bit 08 and 09 =
"1"), then JOG 1 has the higher priority, i.e. the speed
programmed in parameter 509 will be used.
Bit 10, Data not valid/valid
Is used to notify the VLT5000 series whether the
process data channel (PCD) should respond to
modifications by the master (bit 10 = 1) or not. The
function can be inverted in parameter 805.
NB!:
In the case of bit 10 = 0, the VLT does
not respond to the Control word or the
main reference value.
Bit 11, Without function/Frequency correction DOWN
Is used to reduce the speed reference value by
the amount given in parameter 219.
In the case of bit 11 = "0", no modification of
the reference value occurs.
In the case of bit 11 = "1", the reference value is reduced.
Bit 12, Without function/Frequency correction UP
Is used to increase the speed reference value by
the amount given in parameter 219.
In the case of bit 12 = "0", no modification of
the reference value occurs.
In the case of bit 12 = "1", the reference
value is increased.
If both - slowing down and accelerating - are activated
(bit 11 and 12 = "1"), slowing down has priority, i.e.
the speed reference value will be reduced.
Bit 13/14, Setup selection
Bit 13 and 14 are used to choose between the four
parameter setups according to the following table:
Setup
Bit 14
Bit 13
1
0
0
2
0
1
3
1
0
4
1
1
The function is only possible if
External Selection
has been chosen in parameter 004.
The selection in parameter 507 determines
how bit 13/14 is linked with the corresponding
function of the digital inputs.
Bit 15, Without function/Reversion
Reversion of the rotational direction of the motor. In
the case of bit 15 = "0", no reversion occurs. In
the case of bit 15 = "1", a reversion takes place.
Please note that the reversion in the factory setting in
parameter 506 has been selected as "terminal". Bit
15 only causes a reversion if bus, bus or terminal or
bus and terminal has been selected (bus and terminal
only in connection with terminal 9, however).
NB!:
Unless otherwise indicated, the bit of the Control
word is linked with the corresponding function
of the digital inputs as a logical "or" function.
MG.90.G1.02 - VLT is a registered Danfoss trademark
24
Содержание VLT 5000 Series
Страница 63: ......