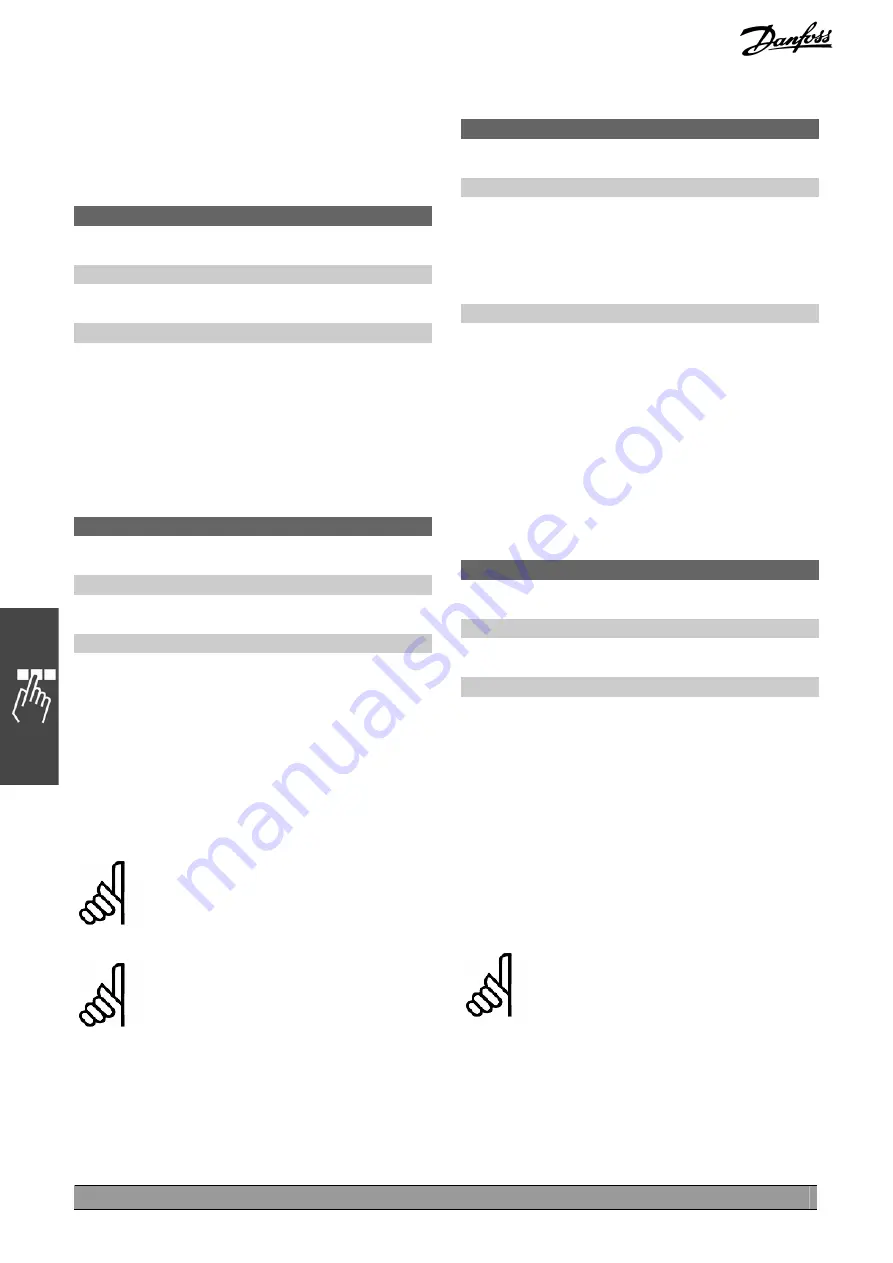
MCO 305 Design Guide
__ Parameter Reference __
¾
default setting
[ ]
value for use in communication via serial communication port
190
MG.33.L4.02 – VLT
®
is a registered Danfoss trademark
When working with a normal PID algorithm the
FFVEL must always be the same as the D factor in
order to achieve typical dampening D.
32-66 Acceleration Feed-forward
FFACC
Range
0 – 100000
¾
0
Function
Set the base acceleration whenever you have
limited the bandwidth. Thus you will prevent the
control from not accelerating at all due to the limit
set.
Acceleration Feed-forward
indicates the value
with which the acceleration forward feed is
completed.
For a normal PID algorithm this value is equal to 0.
32-67 Max. Tolerated Position Error
POSERR
Range [unit]
1 – MLONG [qc]
¾
20000
Function
The
Maximum Tolerated Position Error
defines the
tolerance allowed between the current actual
position and the calculated command position. If
the value defined with POSERR is exceeded then
the position control is turned off and a position
error is triggered.
The
Position Error
does not affect the positioning
accuracy, but merely determines how precisely the
theoretically calculated path of motion must be
followed, without an error being triggered.
NB!:
For safety reasons the
Position Error
selected should not be too large since this
could be dangerous for both the machine
and its operator.
NB!:
On the other hand, if the values for the
Maximum Tolerated Position Error
are too
small this could result in frequent errors.
As a guideline, it is wise to set the quadruple of
encoder counts per revolution. This corresponds to
one encoder rotation.
32-68 Reverse Behavior for Slave
REVERS
Option
¾
Reversing allowed
[0]
Reversing only allowed when master
is reversed
[1]
Reversing
blocked
[2]
Function
REVERS determines the behavior while moving in
reverse (moving in a negative direction): whether
reverse is allowed, only allowed when the master is
reversed or not allowed in general.
The corresponding limitation is always valid, i.e. for
drive synchronization (SYNCP, SYNCV, SYNCM,
SYNCC, etc.), for positioning commands (CVEL),
and even for
Testrun
.
In order to prevent automatic reversing during the
Testrun
adjust the value to 1 or 2.
32-69 Sampling Time for PID control
TIMER
Range [unit]
1 – 1000 [ms]
¾
1
Function
The TIMER parameter determines the sampling
time of the control algorithm. For example, in-
crease the value of the factory settings
– for very low pulse frequency, such as from 1 to
2 qc per sampling time. You need at least 10 to
20 qc per sampling time.
– Or for very slow systems with a long dead time.
If 1 ms is used here for control, large motors will
vibrate.
Accordingly, the value should not be set higher
than 1000 (= 1 s). This would be a very slow
control.
NB!:
Note that is has a direct effect on the PID
loop e.g. if you double the TIMER the par.
32-60
Proportional Factor
has twice the
effect.
Содержание MCO 305
Страница 4: ......