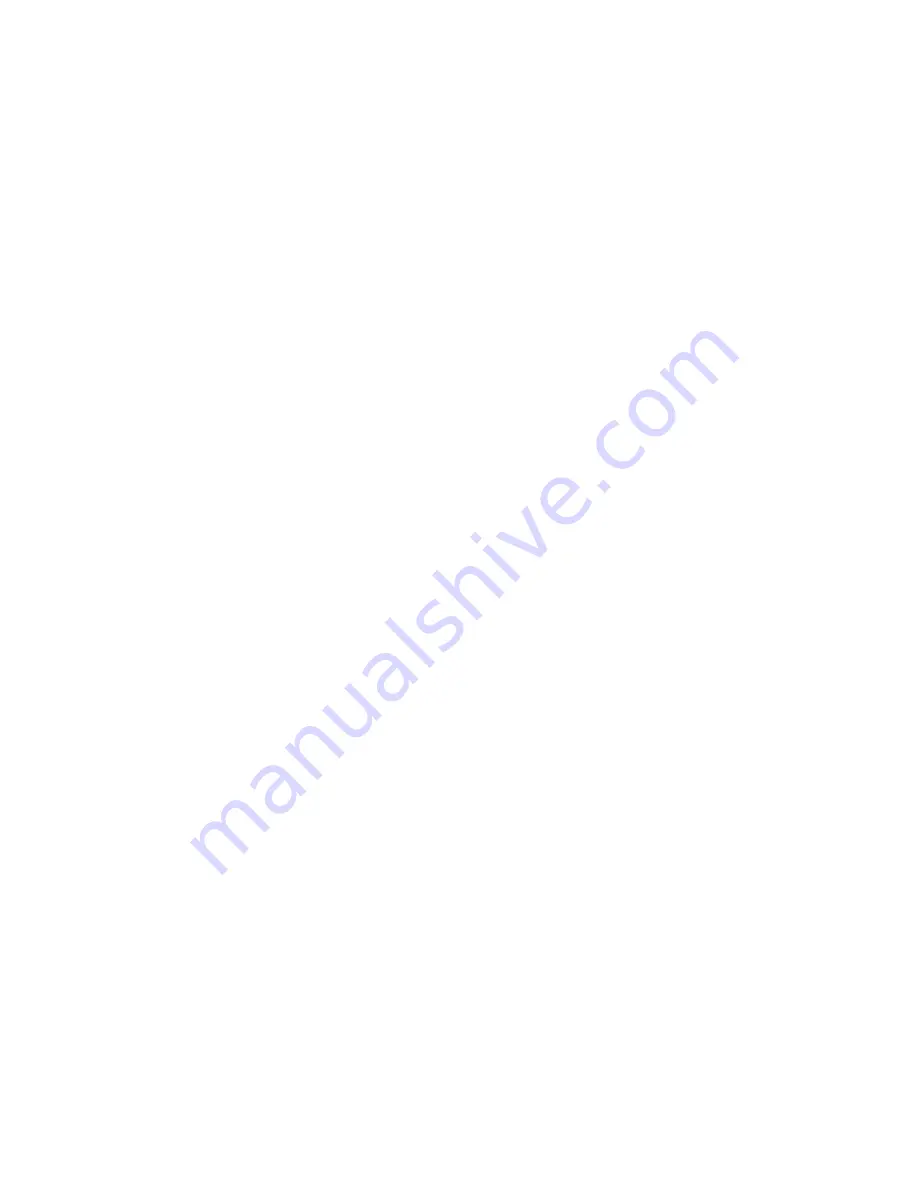
36
14 - MAINTENANCE
During the unit operating life the service checks and tests must
be carried out in accordance with applicable national
regulations.
If there are no similar criteria in local regulations, the
information on checks during operation in annex C of standard
EN 378-2 can be used.
External visual checks: annex A and B of standard EN378-2.
Corrosion checks: annex D of standard EN 378-2. These
controls must be carried out:
•
After an intervention that is likely to affect the resis-tance
or a change in use or change of high-pressure refrigerant,
or after a shut down of more than two years. Components
that do not comply, must be changed. Test pressures above
the respective component design pressure must not be
applied (annex B and D).
•
After repair or significant modifications or significant
system or component extension (annex B).
•
After re-installation at another site (annexes A, B and D).
•
After repair following a refrigerant leak (annex D). The
frequency of refrigerant leak detection can vary from once
per year for systems with less than 1% leak rate per year
to once a day for systems with a leak rate of 35% per year
or more. The frequency is in proportion with the leak rate.
NOTE: High leak rates are not acceptable. The necessary
steps must be taken to eliminate any leak detected.
NOTE 2: Fixed refrigerant detectors are not leak detectors, as
they cannot locate the leak.
14.1 - Soldering and welding
Component, piping and connection soldering and welding
operations must be carried out using the correct procedures and
by qualified operators. Pressurised containers must not be
subjected to shocks, nor to large temperature variations during
maintenance and repair operations.
Any technician attending the machine for any purpose must be
fully qualified to work on refrigerant and electrical circuits.
WARNING: Before doing any work on the machine ensure
that the power is switched off. If a refrigerant circuit is
opened, it must be evacuated, recharged and tested for leaks.
Before any operation on a refrigerant circuit, it is necessary
to remove the complete refrigerant charge from the unit with
a refrigerant charge recovery unit.
All removal and refrigerant draining operations must be
carried out by a qualified technician and with the correct
material for the unit. Any inappropriate handling can lead to
uncontrolled fluid or pressure leaks.
If an oil draining or recovery operation becomes necessary, the
fluid transfer must be made using mobile containers.
14.2 - General unit maintenance
•
Keep the unit itself and the space around it clean and free
of obstructions. Remove all rubbish such as packing
materials, as soon as the installation is completed.
•
Regularly clean the exposed pipework to remove all dust
and dirt. This makes detection of water leaks easier, and
they can be repaired before more serious faults develop.
•
Confirm that all screwed and bolted connections and joints
are secure.
•
Secure connections prevent leaks and vibration from
developing.
•
Check that all foam insulation joints on the heat exchanger
piping are in good condition.
14.3 - Refrigerant undercharge
If there is not enough refrigerant in the system, this is indicated
by gas bubbles in the moisture sight glass.
If the undercharge is significant, large bubbles appear in the
moisture sight glass, and the suction pressure drops. The
compressor suction superheat is also high. The machine must be
recharged after the leak has been repaired.
Find the leak and completely drain the system with a
refrigerant recovery unit. Carry out the repair, leak test and
then recharge the system.
IMPORTANT: After the leak has been repaired, the circuit
must be tested, without exceeding the maximum low-side
operating pressure shown on the unit name plate.
The refrigerant must always be recharged in the liquid phase into
the liquid line. The refrigerant cylinder must always contain at
least 10% of its initial charge. For the refrigerant quantity per
circuit, refer to the data on the unit name plate.
During applications with option 272 (brine to water) and with
positive evaporation, bubbles will appear in the sight-glass.
This is normal, when the charge is optimised for improved
efficiency in brine applications.
14.4 - Refrigerant guidelines
Refrigeration installations must be inspected and maintained
regularly and rigorously by specialists. Their activities must be
overseen and checked by properly trained people. To minimise
discharge to the atmosphere, refrigerants and lubricating oil
must be transferred using methods which reduce leaks and
losses to a minimum.
•
Leaks must be repaired immediately.
•
If the residual pressure is too low to make the transfer
alone, a purpose-built refrigerant recovery unit must be
used.
•
Compressor lubricating oil contains refrigerant. Any oil
drained from a system during maintenance must therefore
be handled and stored accordingly.
•
Refrigerant under pressure must never be discharged to
the atmosphere.
Содержание BW10 020-090
Страница 30: ...30...
Страница 42: ...VMGFT102...