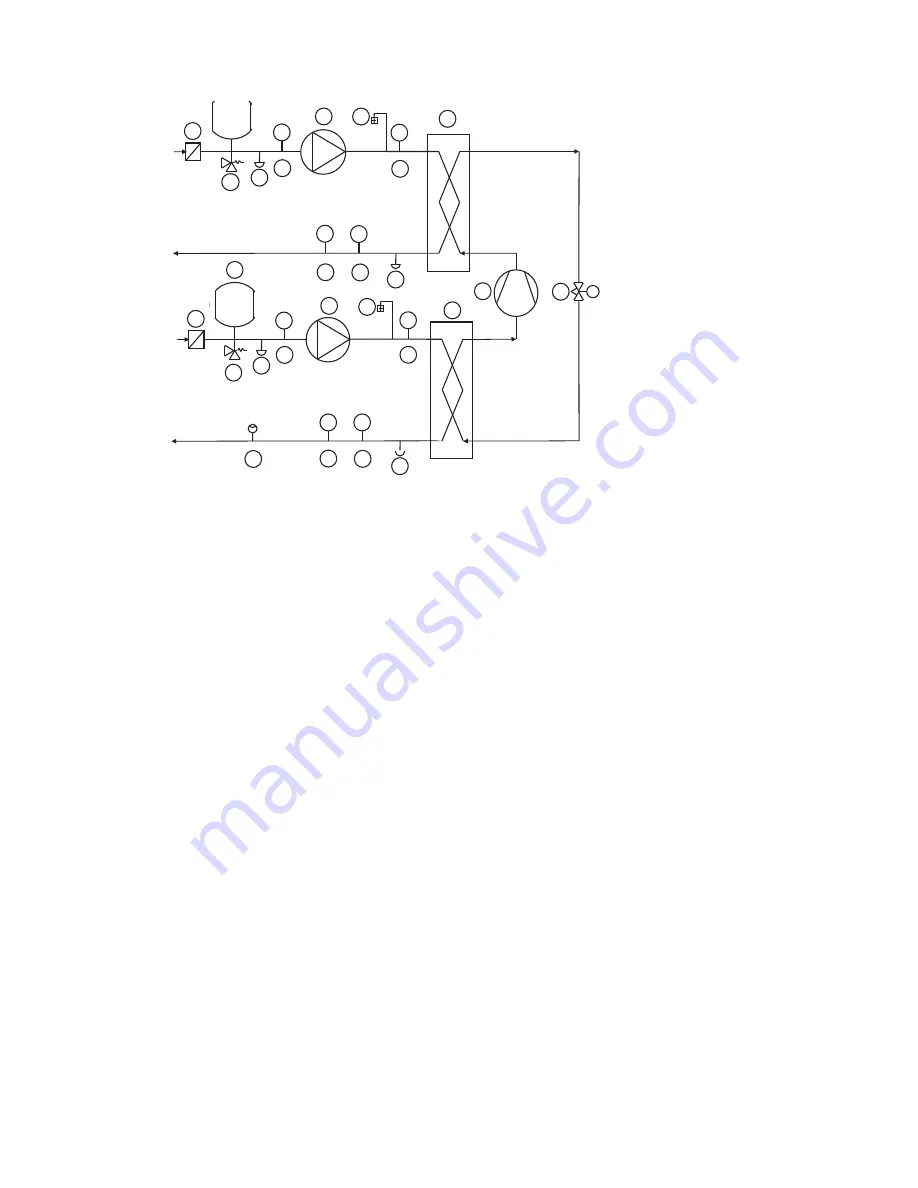
25
Typical water piping diagram, BW10 units with hydronic modules
Components of unit and hydronic module
1
Victaulic screen filter
2
Expansion tank
3
Safety valve
4
Water pump
5
Air vent
6
Water drain valve
7/8 Entering/leaving pressure sensor
9/10 Entering/leaving temperature probe
12 Flow switch BW10 option 272 (sizes 020-045 only)
13 Compressor
14 Evaporator
15 Condenser
16 Expansion device
NOTE: Units without hydronic
module include a flow switch.
2
6
15
10
9
8
5
1
3
4
7
6
14
9
8
5
1
2
4
PT
PT
TT
TT
PT
PT
TT
13
16
TT
12
3
7
10
6
6
Unit water inlet
Condenser water loop
Unit water outlet
Unit water inlet
Unit water outlet
Evaporator water loop
8 - NOMINAL WATER FLOW CONTROL WITH FIXED-
SPEED PUMP
8.1 - General
The water circulation pumps of the BW10 units have been
sized to allow the hydronic modules to cover all possible
configurations based on the specific installation conditions, i.e.
for various temperature differences between the entering and the
leaving water (∆T) at full load, which can vary between 2.5 and
7 K for evaporators and 3 and 18 K for condensers.
This required difference between the entering and leaving water
temperature determines the nominal system flow rate. It is above
all absolutely necessary to know the nominal system flow rate
to allow its control via a manual valve.
Manual control valves for the unit are not supplied and must be
installed upstream and downstream of the evaporator and
condenser water loops to ensure correct flow control.
With the pressure loss generated by the control valve in the
hydronic system, the valve is able to impose the system
pressure/flow curve on the pump pressure/flow curve, to obtain
the desired operating point (see example).
The pressure drop reading in the plate heat exchanger is used to
control and adjust the nominal system flow rate. The pressure
drop is measured with the pressure sensors connected to the
heat exchanger water inlet and outlet.
Use this specification for the unit selection to know the system
operating conditions and to deduce the nominal air flow as well
as the plate heat exchanger pressure drop at the specified
conditions. If this information is not available at the system
start-up, contact the technical service department responsible for
the installation to get it.
These characteristics can be obtained from the technical
literature using the unit performance tables or the Electronic
Catalogue selection program for all conditions.
8.2 - Water flow control procedure
As the total system pressure drop is not known exactly at the
start-up, the water flow rate must be adjusted with the control
valve to obtain the specific flow rate for this application.
Proceed as follows:
Open the valve fully.
Start-up the pump using the forced start command (refer to the
controls manual) and let the pump run for two conse-cutive
hours to clean the hydronic circuit of the system (presence of
solid contaminants).
Read the hydronic module pressure drop by taking the
difference of the readings at the machine connected to the
hydronic module inlet and outlet. Compare this value after two
hours of operation.
Содержание BW10 020-090
Страница 30: ...30...
Страница 42: ...VMGFT102...